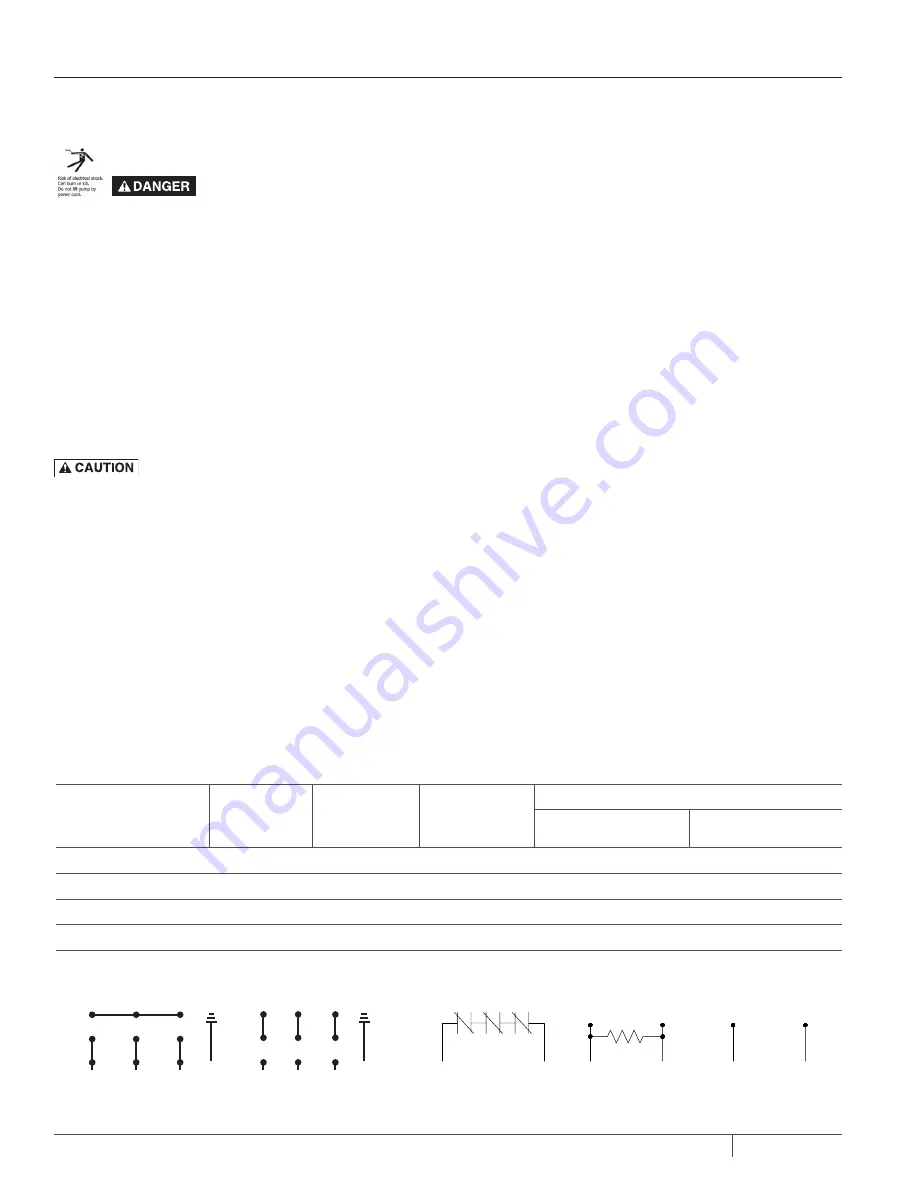
8
E-03-601 (02-15-22)
MAKING ELECTRICAL CONNECTIONS
ElECTROCUTION HAZARD:
Must be
installed by a qualified professional. Disconnect all electrical
power before installation or servicing the pump.
All electrical wiring must be in accordance with local codes,
and only competent electricians should make the installations.
Complete wiring diagrams are glued to the inside cover of the
panel. It is VERY IMPORTANT to check all wires for grounds with
an ohmmeter or Megger meter after the connections are made
as one grounded wire can cause considerable trouble
.
NOTICE
FM rated models are only to be used in
60hz applications.
NOTICE
If equipment is not properly wired and protected as
recommended, the warranty is void.
The 230 volt 3 phase pump has a dual marked
nameplate. For ordinary location pumps, voltage may be rewired
by qualified personnel. For hazardous location pumps, voltage
may be rewired by the manufacturer or a Class I, Div I equipment
qualified electrician. Once the voltage is changed, the factory
cord tag indicating 230 volt 3 phase must be removed.
For record keeping purposes, we suggest the pump be marked
externally with the new voltage and qualified personnel that
performed the change. Pumps shipped from the factory as 460
volt 3 phase cannot be rewired to any other voltage.
TO RE-WIRE THE PUMP FROM 230V TO 460V 3 PHASE
Only a 230V pump from the factory is considered dual voltage, a
cord label clearly states the factory wound voltage.
1. Remove all six (#7) cap screws then raise the cord cap
assembly enough to slip a prying instrument on opposite
sides between the cord cap casting and the motor housing.
Take care to not damage the o-ring or the machined
surfaces of the castings. Doing so could void FM agency
certifications.
2. While prying evenly on both sides; separate the cord cap
casting from the motor housing, the assembly is airtight
and will have a vacuum effect when disassembling.
3. Once separated, the cord cap can be inverted and rotated
to the outside of the pump assembly, and a bolt can be
re-used to secure the upside down cord cap to the motor
housing for ease of rewiring.
Refer to the wiring diagram within this manual for wiring
details. Once all electrical connections are finished and secure
(a crimped electrical connector is best to prevent issues due
to vibration if required), the cord cap should be re-attached
reversing the steps above. Ensure the o-ring is in place and
perform a hi-pot test for safety once everything is complete.
HEAT SENSORS AND SEAL FAILURE CONNECTIONS
Be sure heat sensor wires are connected in series with the starter
coil. Connections are provided on the terminal strip.
DUAL VOLTAGE
3 PHASE MOTOR WIRING
230V 3ø
460V 3ø
GREEN
GREEN
R
(L3)
W
(L2)
BL
(L1)
R
(L3)
W
(L2)
BL
(L1)
1
2
3
7
8
9
4
5
6
1
2
3
7
8
9
4
5
6
INSTALLATION
SYSTEM TYPE
NUMBER OF
CONTROL WIRES
NUMBER OF
POWER LINES
NUMBER OF
GROUND WIRES #8
HEAT SENSOR & SEAL FAILURE
NUMBER OF SENSOR
WIRES
NUMBER OF GROUND
WIRES
Simplex
4
3
1
3
1
Simplex with Alarm
6
3
1
3
1
Duplex
6
6
2
6
2
Duplex with Alarm
8
6
2
6
2
NUMBER OF CONDUCTORS REQUIRED BETWEEN CONTROL PANEL AND NEMA 4 JUNCTION BOX
Power lines and control wires can be carried in conduit or can be underground buried cable
HEAT SENSORS
IN MOTOR WINDINGS
BLACK
WHITE
MOTOR HEAT SENSORS
ELECTRODE
ELECTRODE
RED
ORANGE
330KΩ
HAZARDOUS RATED ONLY
SEAL FAILURE
ELECTRODE
ELECTRODE
RED
ORANGE
NON-HAZARDOUS RATED ONLY
SEAL FAILURE
HEAT SENSORS AND SEAL FAILURE CONNECTIONS
FOR ANY VOLTAGE MOTOR
Содержание HPS4HDX
Страница 3: ...3 E 03 601 02 15 22 PAGE INTENTIONALLY LEFT BLANK ...
Страница 17: ...17 E 03 601 02 15 22 WIRINGDIAGRAMS ...
Страница 18: ...18 E 03 601 02 15 22 WIRINGDIAGRAMS ...