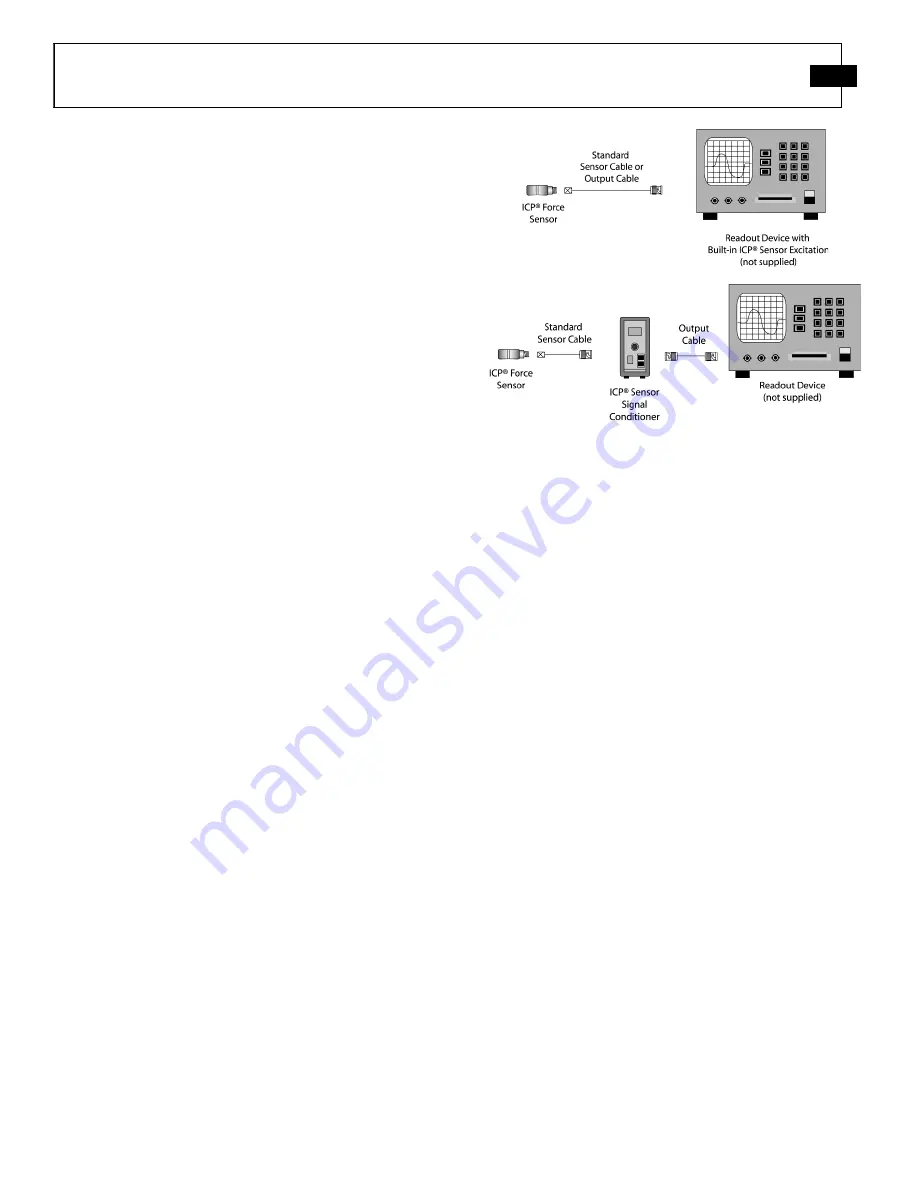
ICP
FORCE SENSOR OPERATION MANUAL
8
For best results, the applied force should be distributed evenly
over the contact surface of the sensor. Care should be taken to
limit the bending moment induced into the sensor by edge
loading or off-axis loading of the sensor. This is accomplished
by applying a force to the sensor as close as possible to the
center of the sensor. In the event sensor is to be installed to
measure a unit under test with a much larger area than that of
the sensing surface of sensor, such as a large metal plate, it may
be necessary to use an arrangement of two to four sensors in a
measuring platform. Independent sensor output can be
monitored or the sensors can be connected electrically in
parallel to measure the resulting summed forces when used in a
multiple sensor type arrangement.
TYPICAL ICP
SYSTEM CONFIGURATION
Sensors with built-in ICP
circuitry require a constant-current
excitation voltage for operation. The enclosed specification
sheet provides specific power requirements. Required supply
voltage is normally 20 to 30 VDC, while the constant current
required ranges from 2 to 20 mA.
PCB standard battery-powered signal conditioners are factory
set at 2 mA and may be used to adequately drive a 5.5 kHz
signal using a typical PCB 29 pF/ft. cable to a desired 5-Volt
full scale output, or about 175 feet (53 meters). PCB line signal
supplies are factory set at 4 mA (and adjustable from 2 to 20
mA), enabling signals to be transmitted over hundreds of feet
(meters), depending on the frequency of interest.
It is necessary to supply the sensor with a 2 to 20 mA constant
current at +20 to +30 VDC through a current-regulating diode
or equivalent circuit, contained in all PCB signal conditioners.
See Guide G-0001B for powering and signal conditioning
information pertaining to all ICP
instrumentation.
Most of the line powered signal conditioners manufactured by
PCB have an adjustable current feature allowing a choice of
input currents from 2 to 20 mA. In general, for lowest noise
(best resolution), choose the lower current ranges. When
driving long cables (to several thousand feet(meters)), use
higher current, up to 20 mA maximum. Consult a factory
applications engineer or local distributor to determine if higher
current settings are required.
For sensor operation, connect the sensor to the signal
conditioner as shown in the typical ICP
sensor systems below.
Compete system operation requires the connection of the force
sensor to a signal conditioner, then to a readout device
(oscilloscope, meter, recorder, or A-to-D board) or to a readout
device with built-in ICP
sensor excitation. Insert the cable
center pin into the sensor electrical receptacle. Tighten the
coaxial cable to the sensor by turning the cable nut by hand to
ensure good electrical contact.
Do not spin the sensor onto
the cable
as this will fatigue the electrical center pin resulting
in an intermittent connector or damaged cable.
Figure 15 - Typical ICP
System Configurations
6.0 POLARITY
Compressive forces upon an ICP
force sensor produce a
positive-going voltage output. Tensile forces produce a
negative-going voltage output. Sensors with reversed polarity
are available upon request.
Содержание 208A11
Страница 17: ......