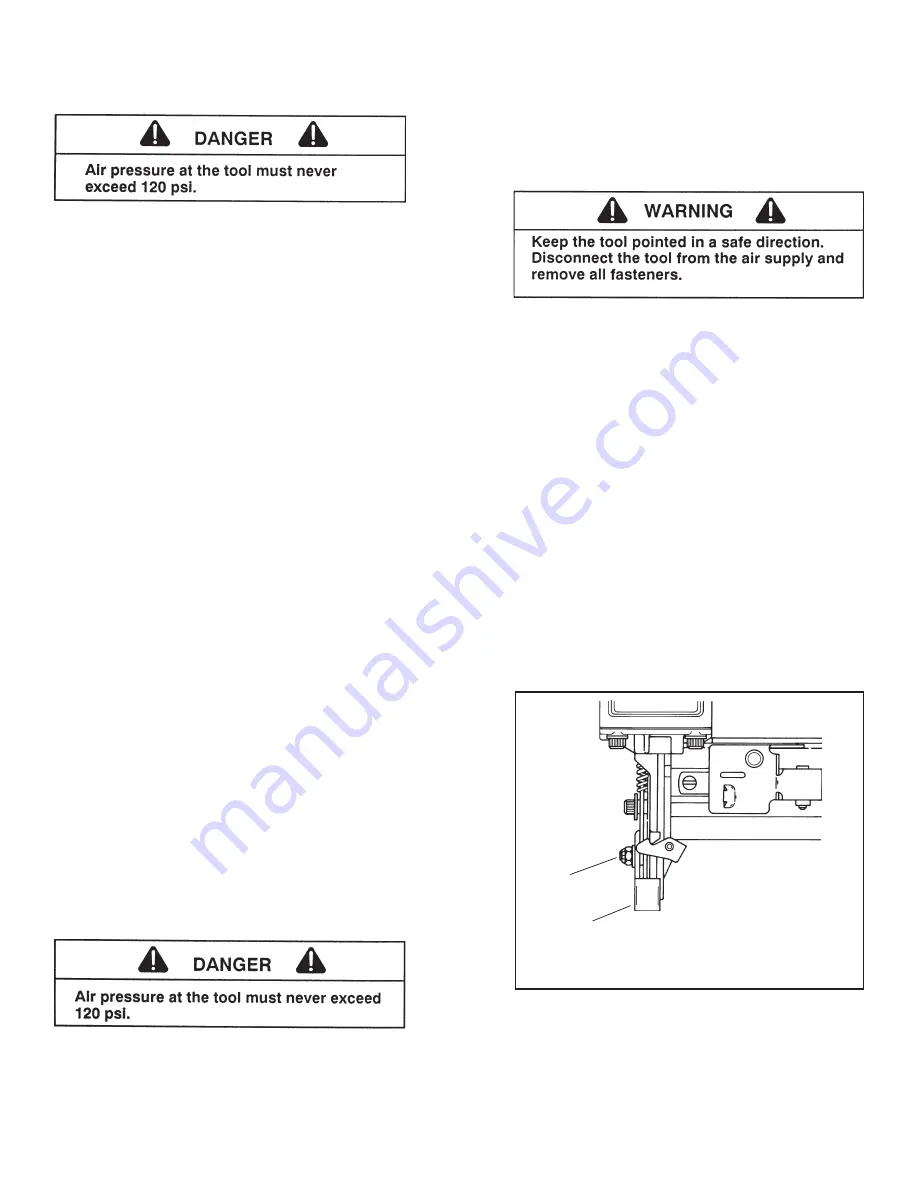
TOOL INSTALLATION
Your Paslode tool comes ready for immediate use
and can be installed by following these steps:
1. SAFETY - All tool operators and their immediate
supervisors must become familiar with the operator
safety instructions before operating the tool. The
instructions are on page 2 of this manual.
2. Included wuth each tool are one copy of this
Safety and Maintenance manual and one copy of
the Tool Schematic. Keep these publications for
future reference. An ownership registration card is
also included. This card must be completed and
returned to Paslode immediately to register your
ownership.
3. The plastic cap in the air inlet of the tool must be
removed before the male fitting is installed. The fit-
ting must be a male pneumatic type that discharges
the air from the tool when the air line is discon-
nected.
4. Install a filter/regulator/lubricator unit, with a
gauge as close as practical to the tool, preferably
within ten feet. Refer to the Air Systems section of
this manual for air hose requirements and lengths.
In general, no other special installation is required.
5. If the operator is working at a bench or table,
it is usually best to run the air line underneath the
bench. A small tray under the benchtop can hold
the fastener supply and the tool when not in use.
6. If this tool does not work when it is first connect-
ed, do not try to make repairs. Call your Paslode
representative immediately.
TOOL OPERATION
Depth of Drive Adjustment
(On tools equipped with this feature)
The depth of drive adjustment is made by
adjusting the work contacting element. The
lock nut is loosened to allow the element to be
moved up or down. You will need a 3/8 inch
open end or 5/32 inch hex socket wrench to
make this adjustment.
If the tool is overdriving (the fastener head or
crown is driven below the work surface), the
work contacting element should be moved
downward. If the fasteners stand up (the head
or crown is not flush with the surface), the work
contacting element should be moved up.
Adjust the work contacting element until the
fastener head or crown depth meets job re-
quirements.
LOCK
NUT
WORK
CONTACTING
ELEMENT
MOVE UP
TO INCREASE
DRIVE DEPTH
MOVE DOWN
TO INCREASE
DRIVE DEPTH
➔
➔
5