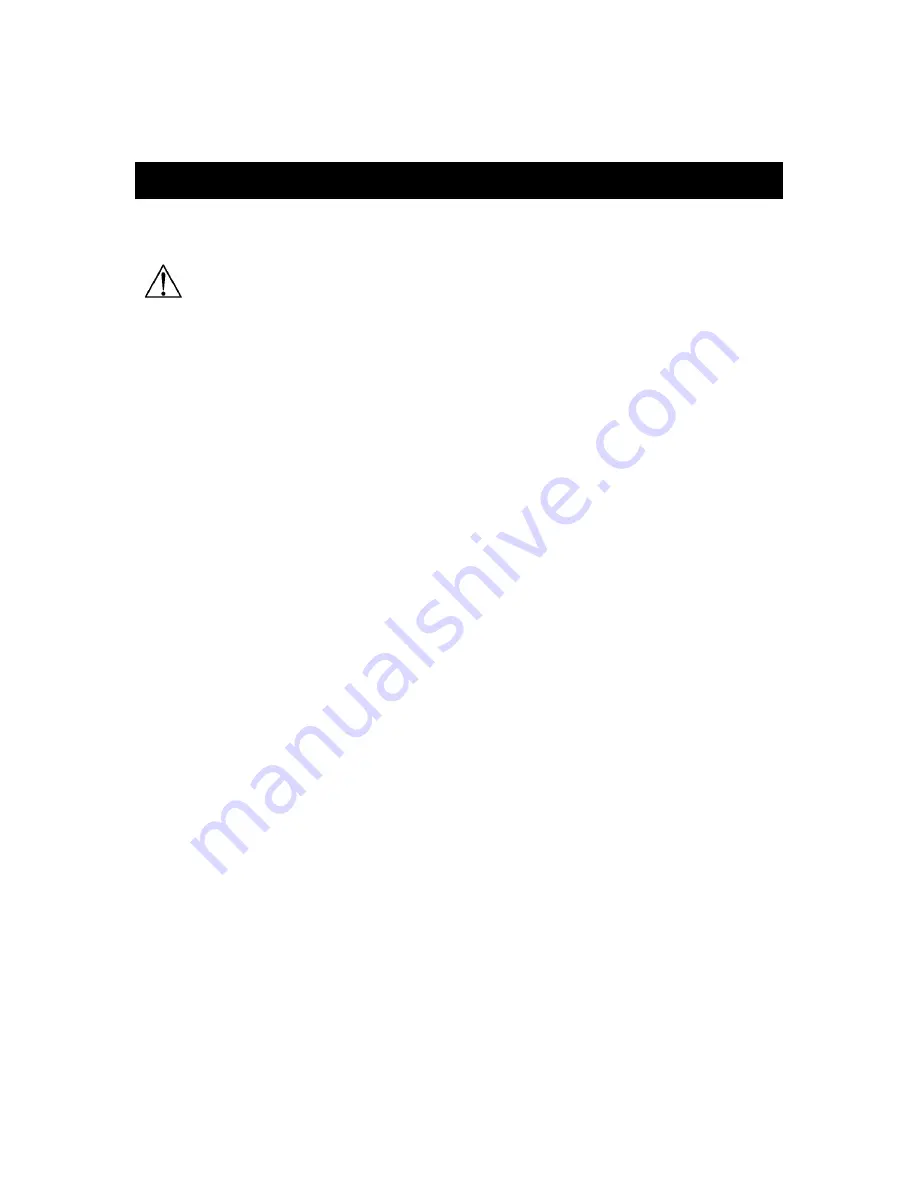
TROUBLESHOOTING
This section will help to diagnose common problems and will give suggestions to solve
them.
T
O PREVENT INJURY
,
ALWAYS
DISCONNECT
THE
AIR
SUPPLY
HOSE
WHEN ADJUSTING
,
SERVICING OR DISASSEMBLING THE TOOL
.
F
IRST
:
C
HECK THE
C
OMPRESSED AIR SUPPLY
Many of problems come from a faulty or inadequate compressed air supply system.
Before attempting to repair the tool, the following points should be checked:
• check the pressure at the output of the compressor; adjust to 80-100 psi
(5.5-7.0 bar) as required
• check the tank pressure of the compressor & adjust the start/stop limits
• check the air delivery system; a 3/8" hose is recommended
• use fewer tools simultaneously; do not exceed the capacity of the compressor or of
the delivery system
• drain water from the compressor
S
ECOND
:
C
HECK FOR AIR LEAKS
At rest, this tool should not have any air leak. Before attempting to repair the tool and
replace parts, check the following:
• Check rings and replace if necessary
• The top edge of main cylinder should be free of dents.
• Clean & lubricate the head assembly; re-assemble the head assembly carefully
• Check interior of head for scratches
T
OOL DOES NOT DRIVE FASTENERS
• Check that there are fasteners in the feeder channel
• Make sure the feeder clip is engaged behind the fasteners
• Check the front end of the feeder channel for burrs or damages
• Check the safety mechanism
• Check if the driver is stuck in down position (see below)
• Check for obstruction in the fastener ejection area