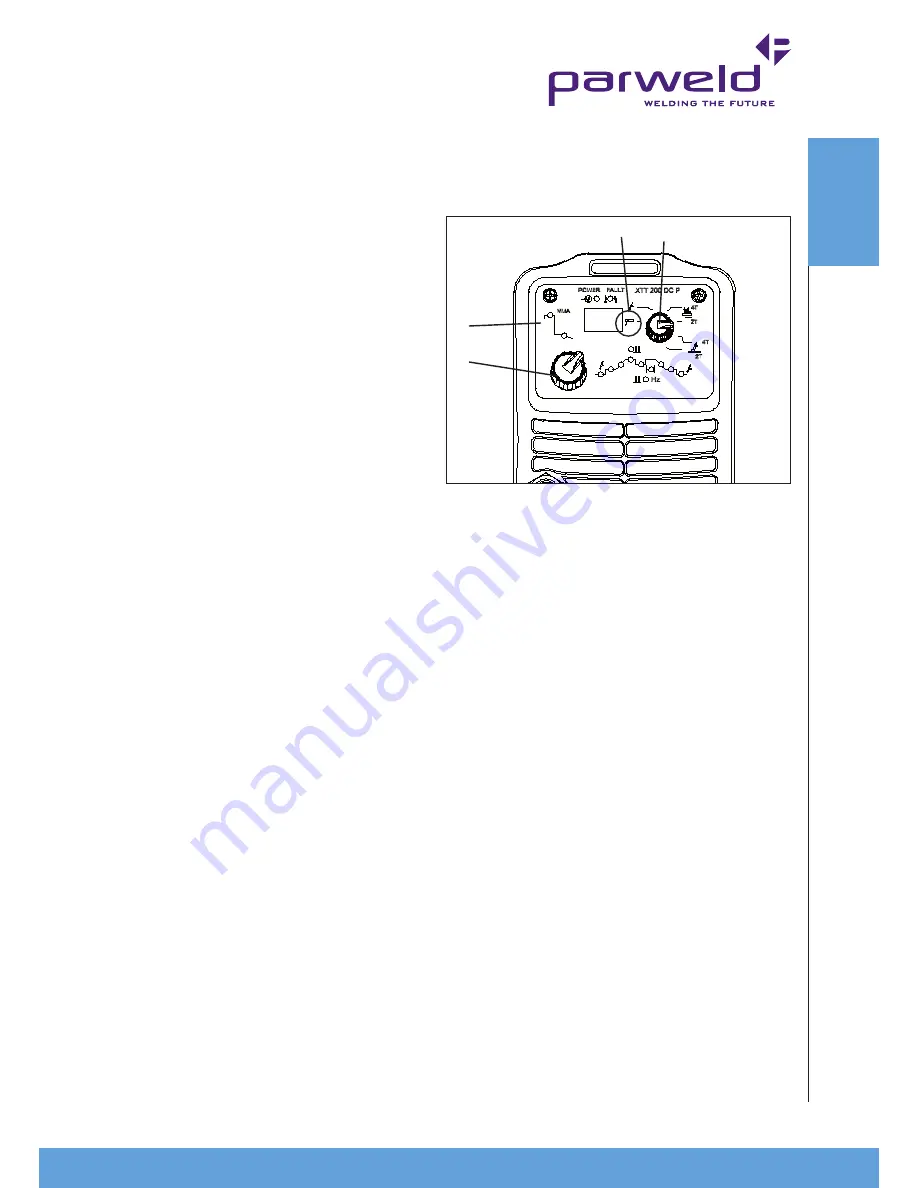
www.parweld.com
www.parweld.com
7
In areas, not subjected to abnormal vibration or shock.
In areas not exposed to direct sunlight or rain.
Place at a distance of 12” (300 mm) or more from walls or similar
that could restrict natural airflow for cooling.
5.3 Input and grounding connection
WarnInG
Before starting the installation, check that your power supply
is adequate for the voltage, amperage, phase, and frequency
specified on the Machine nameplate.
Operate the welding power source from a single-phase 50/60 Hz,
AC power supply. The input voltage must match one of the electrical
input voltages shown on the input data label on the unit nameplate.
Refer to the specifications table for voltage tolerances.
Have a qualified electrician connect the input plug. For long runs
over 30m, larger copper wires should be used. The green/yellow
wire in the input cable connects to the frame of the machine. This
ensures proper grounding of the machine when the machine plug is
inserted into the receptacle.
5.4 Output polarity Connections
Electrode polarity
MMA electrodes are generally connected to the ‘+’ terminal and the
work lead to the ‘-‘terminal
But if in doubt consult the electrode manufacturer’s literature.
IF TIG welding the torch should always be connected to the ‘-’
terminal.
5.5 torch installation
MMA cable connections
Connect electrode lead to positive terminal
TIG welding cable connection
Connect the TIG torch to the - terminal. Depending upon the
termination of the torch it may be necessary to fit a power adaptor so
the gas hose can be fitted to the Gas outlet connection. The trigger
wires should be connected to the trigger socket on the front panel
using a suitable plug.
5.6 Work return lead connection
MMA cable connections
Connect work lead to negative terminal
TIG welding
Connect the work return lead to the + terminal
6.0 Operation
WarnInG
When using an open arc process, it is necessary to use correct
eye, head, and body protection.
6.1 MMA Welding Guide
Machine setup
O
pera
tIO
n
Rotate process selector knob A to position 1. Using the main control
B rotate to (2) select the welding current or Arc force. Press the
button to adjust the parameter while the display flashes.
Effects of MMA welding various materials
High tensile and alloy steels
The two most prominent effects of welding these steels are the
formation of a hardened zone in the weld area, and, if suitable
precautions are not taken, the occurrence in this zone of under-bead
cracks. Hardened zone and under-bead cracks in the weld area may
be reduced by using the correct electrodes, preheating, using higher
current settings, using larger electrodes sizes, short runs for larger
electrode deposits or tempering in a furnace.
Manganese steels
The effect on manganese steel of slow cooling from high
temperatures is enbrittlement. For this reason it is absolutely
essential to keep manganese steel cool during welding by quenching
after each weld or skip welding to distribute the heat.
Cast iron
Most types of cast iron, except white iron, are weldable. White iron,
because of its extreme brittleness, generally cracks when attempts
are made to weld it. Trouble may also be experienced when welding
white-heart malleable, due to the porosity caused by gas held in this
type of iron.
Copper and alloys
The most important factor is the high rate of heat conductivity of
copper, making preheating of heavy sections necessary to give
proper fusion of weld and base metal.
A
1
2
B
Содержание XTT-200 DC P
Страница 1: ...Operator Manual ISSUE 1 XTT 200 DC P...
Страница 12: ...www parweld com FAULT FINDING 12...