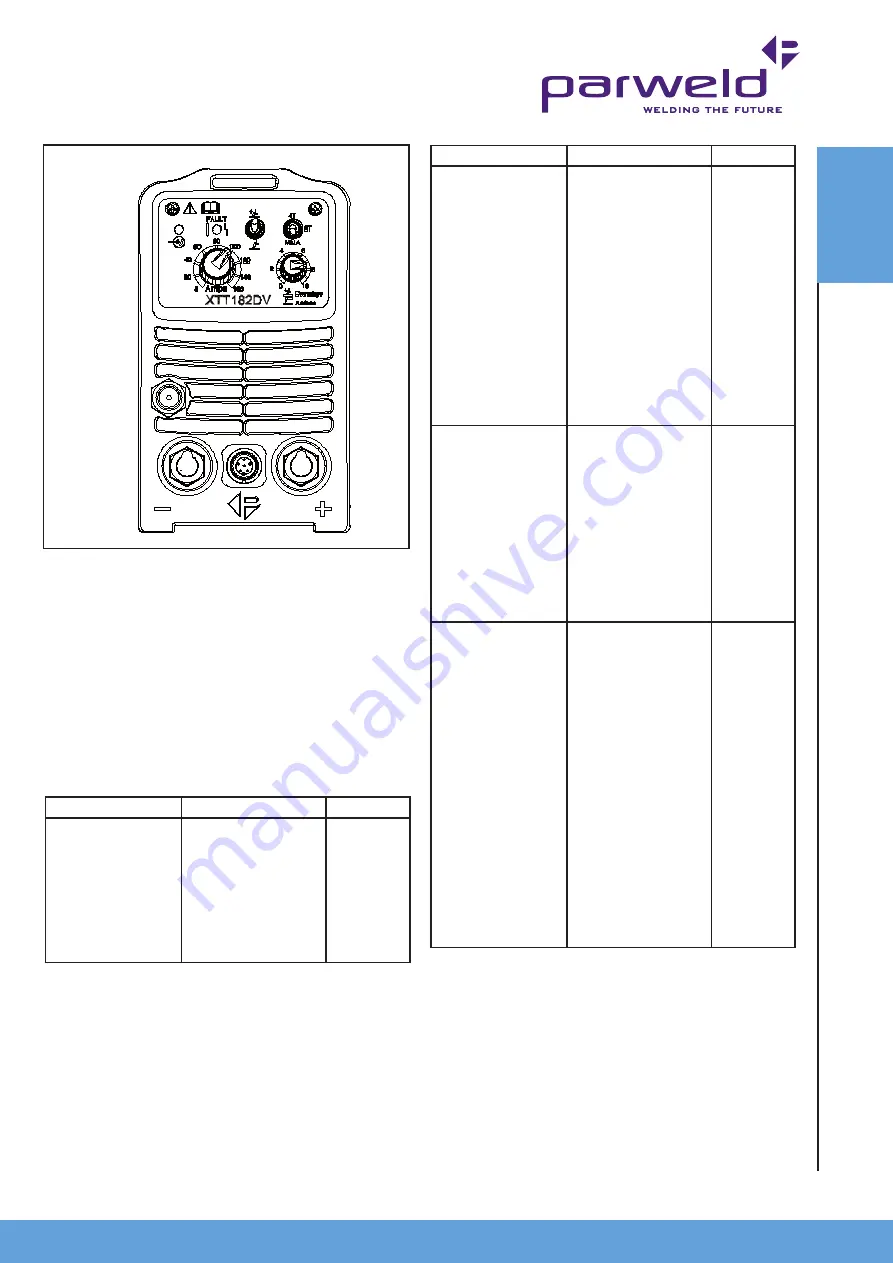
www.parweld.com
www.parweld.com
9
O
pera
tIO
n
1
2
3
1
4
5
6
7
7)
Set the down slope at 5 seconds
You are now ready to weld. The above settings are a guide and you
should adjust to suit the job you are welding if you are unfamiliar
with the machine try to adjust only one parameter at a time so you
become familiar with its effect.
7.0 Fault Finding
MMA welding problem
Description
Possible cause
Remedy
Gas pockets or voids
in weld metal (porosity)
(a) Electrodes are damp
(b) Welding current is
too high.
(c) Surface impurities
such as oil, grease,
paint, etc
(a) Dry
electrodes
before use
(b) Reduce
welding
current
(c) Clean
joint before
welding
Description
Possible cause
Remedy
Crack occurring in
weld metal soon after
solidification.
(a) Rigidity of joint.
(b) Insufficient throat
thickness.
(c) Cooling rate is too
high.
(a) Redesign
to relieve
weld joint
of severe
stresses or
use crack
resistance
electrodes.
(b) Travel
slightly
slower to
allow greater
build up in
throat.
(c) Preheat
plate and
cool slowly.
A gap is left by failure
of the weld metal to fill
the root of the weld
(a) Welding current is
too low.
(b) Electrode too large
for joint.
(c) Insufficient gap
(d) Incorrect sequence
(a) Increase
welding
current
(b) Use
smaller
diameter
electrode.
(c) Allow
wider gap
(d) Use
correct build-
up sequence
Portions of the weld
run do not fuse to the
surface of the metal or
edge of the joint.
(a) Small electrodes
used on heavy cold plate
(b) Welding current is
too low
(c) Wrong electrode
angle
(d) Travel speed of
electrode is too high
(e) Scale or dirt on joint
surface
(a) Use
larger
electrodes
and preheat
the plate
(b) Increase
welding
current
(c) Adjust
angle so the
welding arc
is directed
more into the
base metal
(d) Reduce
travel speed
of electrode
(e) Clean
surface
before
welding.
Содержание XTT-182 DV
Страница 1: ...Operator Manual ISSUE 1 XTT 182 DV...
Страница 12: ...www parweld com FAULT FINDING 12...