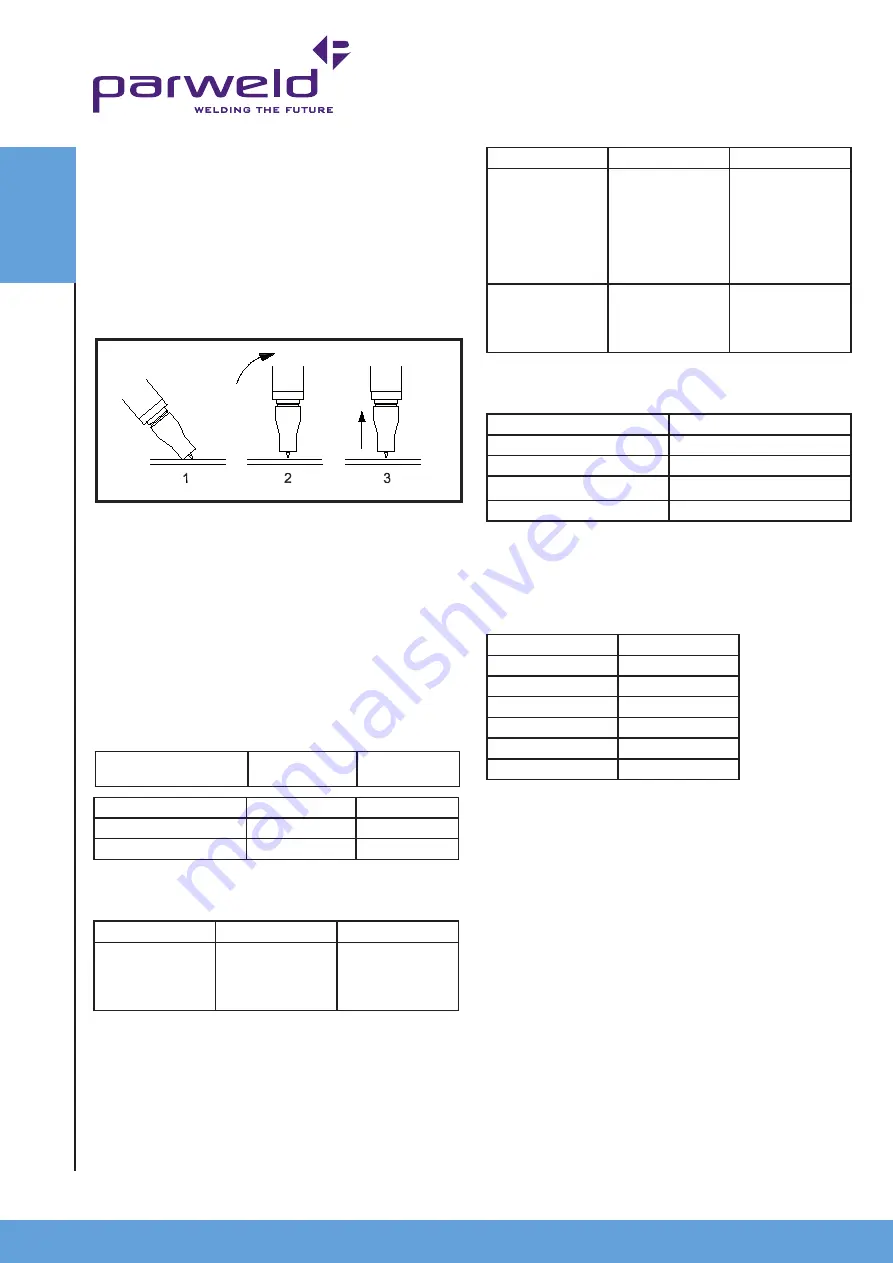
www.parweld.com
8
0.040” (1.0mm)
15-30
20-60
1/16” (1.6mm)
60-120
75-150
3/32” (2.4mm)
100-180
150-250
Tungsten electrode types
Type
Application
Colour
Thoriated 2%
DC welding of mild
steel,
Stainless steel and
Copper
Red
Torch starting in Lift TIG mode
Ensure the gas supply is switched on to the machine. Briefly contact
the tip of the tungsten electrode down onto the work piece with the
torch at around 70
0
from vertical. Depress the trigger to start the gas
flow and switch on the power, lift the torch up from the work piece
to draw out an arc. To prevent melting of the end of the tungsten the
machine will increase the output current when it detects the rise in
arc voltage as the tungsten is lifted from the work piece. At the end
of the weld release the torch trigger and the power will slope down
and switch off.
Type
Application
Colour
Ceriated 2%
DC welding of mild
steel, Stainless
steel, Copper
AC welding
of aluminium,
magnesium and
their alloys
Grey
Zirconiated
AC welding
of aluminium,
magnesium and
their alloys
White
Guide for selecting filler wire diameter
Filler wire diameter
Current range
1/16” (1.6 mm)
20 - 90
3/32” (2.4 mm)
65 - 115
1/8” (3.2 mm)
100 - 165
3/16” (4.8 mm)
200-350
The filler wire diameter specified is a guide only, other diameter
wires may be used according to the welding application.
Shielding gas selection
Alloy
Shielding gas
Aluminium & alloys
Pure Argon
Carbon steel
Pure Argon
Stainless steel
Pure Argon
Nickel alloy
Pure Argon
Copper
Pure Argon
Titanium
Pure Argon
Machine setup for TIG welding
DC TIG welding
1)Connect the torch to the - connection and the gas hose to the gas
outlet.
2) Connect the trigger control plug on the torch to the trigger socket.
3) Connect the Earth lead to the + connection.
4) Set the process mode to 2T or 4T if you prefer a latching trigger
action. (Note in 4T position you must press and release to start the
process and press and release again to stop the process. When
stopping in 4T mode holding down the trigger button will activate the
slope down, releasing the button will switch off the arc)
5) Select HF start (bottom position)
6) Dial up the welding amperage required
O
pera
tIO
n
Torch starting in HF mode
Ensure the gas supply is switched on to the machine. Hold the torch
with the tip of the tungsten approx 2-3 mm from the job. Depress the
trigger to start the gas flow and switch on the power. At the end of
the weld release the torch trigger and the power will slope down and
switch off. (Note in 4T position you must press and release to start
the process and press and release again to stop the process. When
stopping in 4T mode holding down the trigger button will activate
the slope down, releasing the button will switch off the arc) when
starting the arc the HF will only fire for a few seconds so if the arc is
not started withing this tine the starting process should be repeated
by releasing the trigger and depressing again.
TIG welding guide ranges
Electrode diameter
AC current
(amps)
DC current
(amps)
Содержание XTT-182 DV
Страница 1: ...Operator Manual ISSUE 1 XTT 182 DV...
Страница 12: ...www parweld com FAULT FINDING 12...