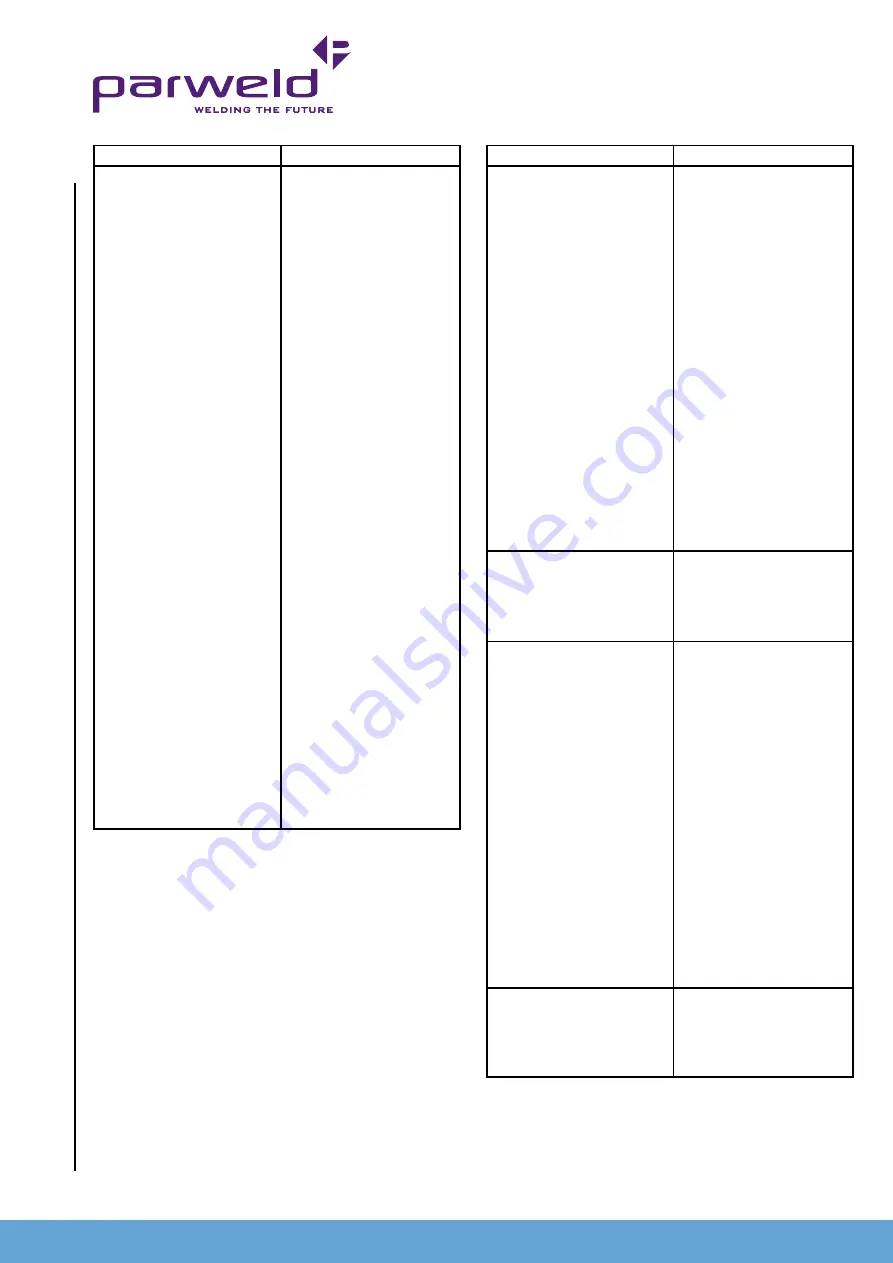
www.parweld.com
www.parweld.com
10
CO
ntr
O
lS
problem
Cause/Corrective action
Porosity - small cavities or holes
Resulting from gas pockets in
weld metal.
Inadequate shielding gas
coverage. Check for proper
gas flow rate.
Remove spatter from gun
nozzle.
Check gas hoses for leaks.
Eliminate drafts near welding
arc.
Place nozzle 6-13 mm from
work piece Hold gun near bead
at end of weld until molten
metal solidifies.
Wrong gas. Use welding
grade shielding gas; change to
different gas.
Dirty welding wire. Use clean,
dry welding wire. Eliminate
pickup of oil or lubricant on
welding wire from feeder or
liner.
Work piece dirty. Remove all
grease, oil, moisture, rust,
paint, coatings, and dirt from
work surface before welding.
Use a more highly deoxidizing
welding wire (contact supplier).
Welding wire extends too far
out of nozzle.
Be sure welding wire extends
not more than 13 mm beyond
nozzle.
problem
Cause/Corrective action
Incomplete fusion to base metal
Work piece dirty. Remove all
grease, oil, moisture, rust,
paint, coatings, and dirt from
work surface before welding.
Insufficient heat input. Select
higher voltage range and/or
adjust wire feed speed.
Improper welding technique.
Place stringer bead in proper
locations) at joint during
welding.
Adjust work angle or widen
groove to access bottom
during welding.
Momentarily hold arc on
groove side walls when using
weaving technique.
Keep arc on leading edge of
weld puddle. Use correct gun
angle of 0 to 15 degrees.
Excessive Penetration – weld
metal melting through base
metal and hanging underneath
weld.
Excessive heat input. Select
lower voltage range and
reduce wire feed speed.
Increase travel speed.
Lack Of Penetration - shallow
Fusion between weld metal and
Base metal.
Improper joint preparation.
Material too thick. Joint
preparation and design must
provide access to bottom of
groove while maintaining
Proper welding wire extension
and arc characteristics.
Improper weld technique.
Maintain normal gun angle of
0 to 15 degrees to achieve
maximum penetration. Keep
arc on leading edge of weld
puddle. Ensure welding wire
extends not more than 13 mm
beyond nozzle.
Insufficient heat input. Select
higher wire feed speed and/or
select higher voltage range.
Reduce travel speed.
Burn-Through - weld metal
melting
Completely through base metal
Resulting in holes where no
metal remains.
Excessive heat input. Select
lower voltage range and
reduce wire feed speed.
Increase and/or maintain
steady travel speed.
Содержание XTM303C
Страница 1: ...Operator Manual ISSUE 3 XTM303C...
Страница 15: ...www parweld com 15...