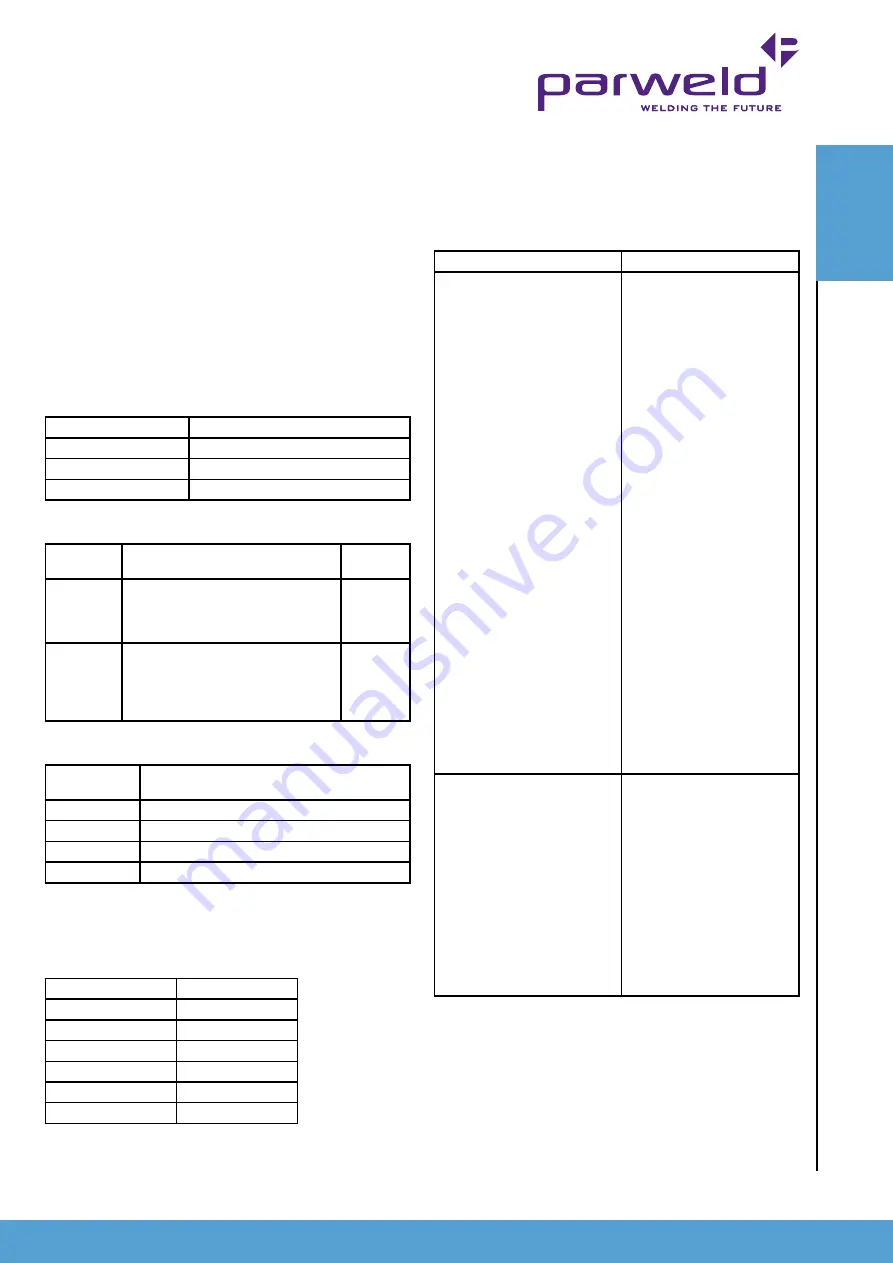
www.parweld.co.uk
13
ACCESSORIES
tIG WelDInG GuIDe ranGeS
Electrode diameter
DC current (amps)
0.040” (1.0mm)
30 – 60
1/16” (1.6mm)
60 – 115
3/32” (2.4mm)
100 – 165
tunGSten eleCtrODe tYpeS
Electrode
type
Welding application
Colour
code
Thoriated
2%
DC welding of mild steel, stainless
steel and copper. Excellent arc
starting, long life, high current carrying
capacity.
RED
Ceriated
2%
DC welding of mild steel, stainless
steel, copper, aluminium, their alloys
longer life, more stable arc, easier
starting, wider current range, narrower
more concentrated arc
GREY
GuIDe FOr SeleCtInG FIller WIre DIaMeter
Filler wire
diameter
DC current range
1/16” (1.6 mm)
20 - 90
3/32” (2.4 mm)
65 - 115
1/8” (3.2 mm)
100 - 165
3/16” (4.8 mm)
200-350
The filler wire diameter specified is a guide only, other diameter
wires may be used according to the welding application.
SHIelDInG GaS SeleCtIOn
Alloy
Shielding gas
Aluminium & alloys
Pure Argon
Carbon steel
Pure Argon
Stainless steel
Pure Argon
Nickel alloy
Pure Argon
Copper
Pure Argon
Titanium
Pure Argon
7.0
Fault finding
7.1 MIG WELDInG PROBLEMS
problem
Cause/Corrective action
Porosity - small cavities or holes
Resulting from gas
pockets in weld metal.
Inadequate shielding
gas coverage. Check for
proper gas flow rate.
Remove spatter
from gun nozzle.
Check gas hoses for leaks.
Eliminate drafts
near welding arc.
Place nozzle 6-13 mm from
work piece Hold gun near
bead at end of weld until
molten metal solidifies.
Wrong gas. Use welding
grade shielding gas; change
to different gas.
Dirty welding wire. Use
clean, dry welding wire.
Eliminate pickup of oil or
lubricant on welding wire from
feeder or liner.
Work piece dirty. Remove all
grease, oil, moisture, rust,
paint, coatings, and dirt from
work surface before welding.
Use a more highly deoxidizing
welding wire (contact supplier).
Welding wire extends too
far out of nozzle.
Be sure welding wire
extends not more than 13
mm beyond nozzle.
Incomplete fusion to base metal
Work piece dirty. Remove all
grease, oil, moisture, rust,
paint, coatings, and dirt from
work surface before welding.
Insufficient heat input. Select
higher voltage range and/or
adjust wire feed speed.
Improper welding technique.
Place stringer bead in
proper locations) at joint
during welding.
Adjust work angle or widen
groove to access bottom
during welding.
(as a guide only 1.0mm material thickness = 30amps of welding
Current)
7. You are now ready to begin, switch on the gas. Lightly touch the
Tungsten Electrode to the work piece and draw the torch away
extending the arc to around 3-5mm
Содержание XTM 405i
Страница 1: ...Operator Manual ISSUE 1 XTM 405i XTM 505i...
Страница 17: ...www parweld co uk 17 FAULT FINDING...