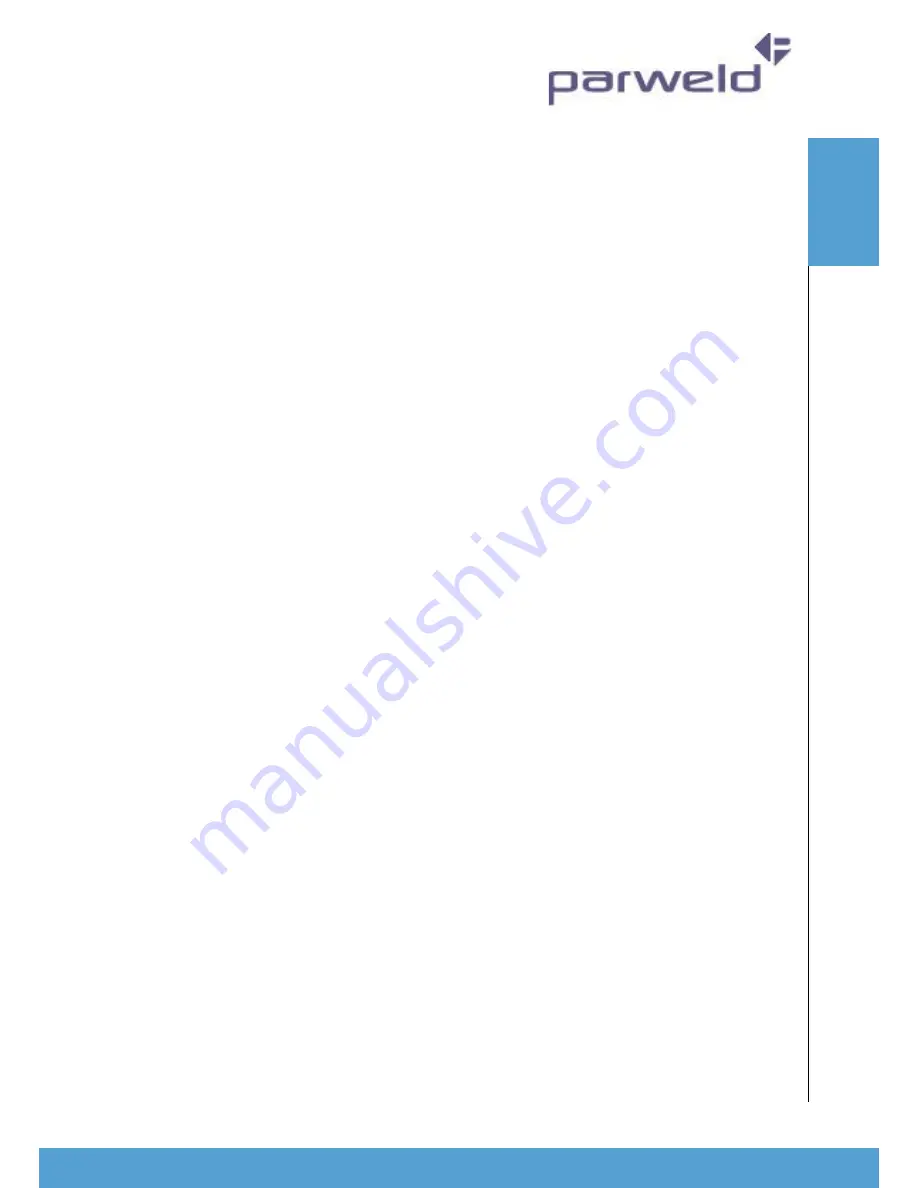
www.parweld.com
www.parweld.com
9
feed speed
Inductance control which controls the smoothness of
the arc
Burn back control which limits the wire stick out at
the end of a weld.
1. Depress the process selector button until the light
for MIG welding is illuminated.
Note: Check that drive rolls, and torch parts are
correct for the wire size and type being used.
2. The optimum idle roll pressure varies with
type of wire, wire diameter, surface conditions,
lubrication, and hardness. As a general rule, hard
wires may require greater pressure, and soft, or
aluminium wire, may require less pressure than
the factory setting. The optimum idle roll setting
can be determined as follows:
3. Press end of gun against a solid object that is
electrically isolated from the welder output and
press the gun trigger for several seconds.
4. If the wire “bird nests”, jams or breaks at the
drive roll, the idle roll pressure is too great. Back
the adjustment knob out 1/2 turn, run new wire.
If the only result was drive roll slippage, loosen
the Hand nut on the central connector and pull
the gun forward about 6” (15cm) away from the
power source. There should be a slight waviness
in the exposed wire. If there is not waviness, the
pressure is too low. Tighten the adjustment knob
1/4 turn, reinstall the gun cable and repeat the
above steps.
6.1.1 Feeding wire electrode
1. When triggering, the electrode and drive
mechanism are electrically “LIVE” relative to work
and ground and remain “LIVE” several seconds
after the gun trigger is release
d.
WARNING
When using an open arc process, it is necessary to
use correct eye, head, and body protection.
2. Position wire over joint. The end of the wire may
be lightly touching the work.
3. Lower welding helmet, operate gun trigger, and
begin welding. Hold the gun so the contact tip to
work distance is about 3/8” (10 mm).
4. To stop welding, release the gun trigger and then
pull the gun away from the work after the arc goes
out.
5. When no more welding is to be done, close valve
on gas cylinder (if used), momentarily operate gun
trigger to release gas pressure and turn off the
machine.
6.1.1 Optimising weld parameters
NOTE These settings are guidelines only. Material
and wire type, joint design, fit up, position, shielding
gas, etc. affect settings. Produce test welds to be sure
they comply to specifications.
Material thickness determines weld parameters.
1. Convert Material Thickness to Amperage (A)
(0.25mm= 1 Amp) 3.2mm = 125 A
2. Select Wire Size
Amperage Range
Wire Size
40 - 145 A
0.8 mm
50 - 180 A
1.0 mm
3. Select Wire Speed (Amperage)
Wire Size
Feed speed
0.8 mm
0.05m/min per Amp
1.0 mm
0.04m/min per Amp
So based on 3.2 mm material thickness amperage
should be 125A if using 1.0mm wire then the wire
feed speed should be
0.04 X 125= 5m/min
Wire speed (amperage) controls weld penetration
4.
Select Voltage. Voltage controls height and width
of weld bead.
Low Voltage: wire stubs into work
High Voltage: arc is unstable (spatter)
Set voltage midway between high/low voltages.
And then fine tune accordingly
6.2 MMA Welding Guide
Controls used
Current control for adjusting the welding current
Arc force (voltage control which controls the hardness
of the arc.
Effects of MMA welding various materials
High tensile and alloy steels
The two most prominent effects of welding these
steels are the formation of a hardened zone in the
weld area, and, if suitable precautions are not taken,
the occurrence in this zone of under-bead cracks.
Hardened zone and under-bead cracks in the weld
area may be reduced by using the correct electrodes,
preheating, using higher current settings, using larger
electrodes sizes, short runs for larger electrode
deposits or tempering in a furnace.
O
pera
tIO
n
Содержание XTI-601 MP
Страница 1: ...INSTRUCTION MANUAL...
Страница 2: ...Operator Manual ISSUE 1 XTI 601 MP...