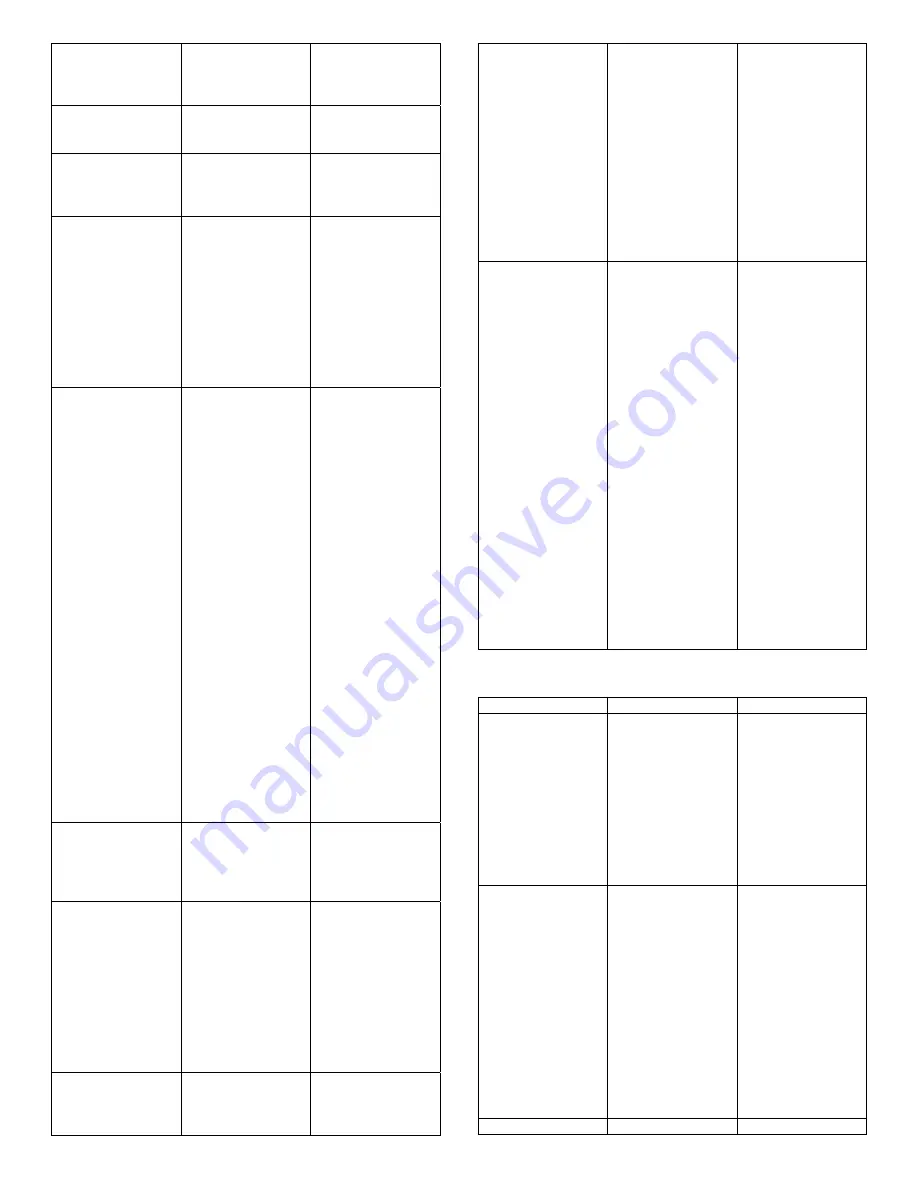
excessive
penetration in butt
joint
Uneven leg length
in fillet joint
Wrong placement
of filler rod
Re-position filler
rod
Electrode melts
when arc is struck
Electrode is
connected to the
‘+’ terminal
Connect the
electrode to the
‘-‘ terminal
Dirty weld pool
(a) Electrode
contaminated
through contact
with work piece or
filler rod material
(b) Gas
contaminated with
air
(a) Clean the
electrode by
grinding off the
contaminates
(b) Check gas
lines for cuts and
loose fitting or
change gas
cylinder
Electrode melts or
oxidizes when an
arc is struck
(a) No gas flowing
to welding region
(b) Torch is
clogged with dust
(c) Gas hose is cut
(d) Gas passage
contains impurities
(e) Gas regulator
is turned off
(f) Torch valve is
turned off
(g) The electrode
is too small for the
welding current
(a) Check the gas
lines for kinks or
breaks and gas
cylinder contents
(b) Clean torch
(c) Replace gas
hose
(d) Disconnect gas
hose from torch
then raise gas
pressure to blow
out impurities
(e) Turn on
(f) Turn on
(g) Increase
electrode diameter
or reduce the
welding current
Poor weld finish
Inadequate
shielding gas
Increase gas flow
or check
gas line for gas
flow problems
Arc flutters during
TIG welding.
(a) Tungsten
electrode is too
large for the
welding current
(b) Absence of
oxides in the
Weld pool.
(a) Select the right
size electrode.
Refer to basic TIG
welding guide.
(b) Refer basic
TIG welding
guide for ways to
reduce arc
flutter
Welding arc
cannot be
established
a) Connect the
work clamp to
the work piece or
connect the
(a) Work clamp is
not connected to
the work piece or
the work/torch
work/torch leads to
the right
welding terminals
(b) Torch lead is
disconnected
(c) Gas flow
incorrectly set,
cylinder empty or
the torch
valve is off
leads are not
connected to the
right
welding terminals
(b) Connect it to
the ‘.’ terminal
(c) Select the right
flow rate,
change cylinders
or turn torch
valve on
Arc start is not
smooth
(a) Tungsten
electrode is too
large for the
welding current
(b)The wrong
electrode is being
used for the
welding job
(c) Gas flow rate is
too high
(d) Incorrect
shielding gas is
being used
(e) Poor work
clamp connection
to work piece
(a) Select the right
size electrode
(b) Select the right
electrode type.
Refer to basic TIG
welding guide
(c) Select the
correct rate for the
welding job. Refer
to basic TIG
welding guide
(d) Select the right
shielding gas.
Refer to basic TIG
welding guide
(e) Improve
connection to work
piece
MMA welding problems
Description Possible
cause Remedy
Gas pockets or
voids in weld
metal (porosity)
(a) Electrodes are
damp
(b) Welding
current is too high.
(c) Surface
impurities such as
oil, grease, paint,
etc
(a) Dry electrodes
before use
(b) Reduce
welding current
(c) Clean joint
before welding
Crack occurring in
weld metal soon
after solidification
commences
(a) Rigidity of joint.
(b) Insufficient
throat thickness.
(c) Cooling rate is
too high.
(a) Redesign to
relieve weld joint
of severe stresses
or use crack
resistance
electrodes.
(b) Travel slightly
slower to allow
greater build up in
throat.
(c) Preheat plate
and cool slowly.
A gap is left by
(a) Welding
(a) Increase