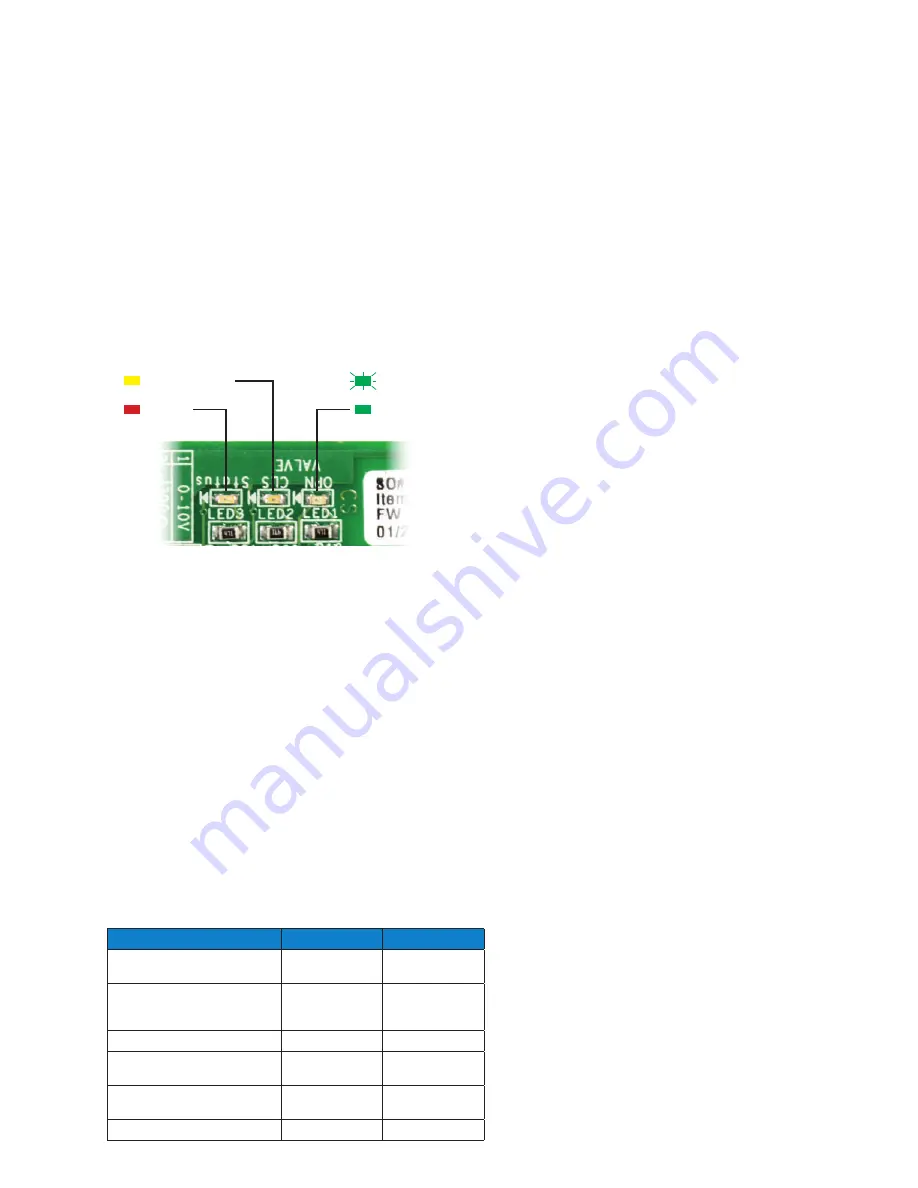
Bulletin 100-50-2.1 –
Page 5
To force the valve shut during operation for test purposes, turn
switch 8 to the “ON” position. To resume normal operation,
turn switch 8 “OFF”. Changing the valve direction set by DIP
switch #5 does not affect the pumpdown direction.
Visual Indicators:
The IB-G has three LEDs to visually show the status of the valve
and board. See Figure 3. The RED LED is a status LED and
will be on when that IB-G has power. The YELLOW LED is
the Close Valve LED; it will only be on when the valve is fully
closed. The GREEN LED is the Valve Open LED and will flash
in different sequences depending on valve position. The GREEN
LED will flash once for valve positions >0% and including 10%,
twice for valve positions >10% and including 20%, etc. The
GREEN LED will remain on when the valve is fully open.
Input Signal Settings (Table 1):
The IB-G can be configured to accept 0-10VDC or 4-20mA
analog signal. To configure the input signal, place the jumper
on the desired setting. The 4-20mA selection offers several
impedance choices based on the external controller. If 4-20mA
is selected, ensure that the impedance of the control circuit
matches that of the external controller requirements. This will
ensure that the maximum valve position, at 20mA, is obtained.
Where possible, it is recommended to use a constant current
design in the external controller to ensure a proper 4-20mA
control signal is supplied to the IB-G.
Valve Selection (Table 2):
This selection must be set to match the step motor valve used
on the system. The IB-G was designed for use with Sporlan
step motor valves. All other valve manufacturers must be tested
and qualified by the end user prior to use to ensure proper valve
operation. Reference Table 4 for valve information.
Figure 3
DIP Switch Settings (Table 3):
The IB-G has a DIP switch table that accommodates systems
that used the legacy Sporlan IB series control boards. Configure
the IB-G with the power off. If switches are moved during
normal operation, the IB-G will re-initialize the valve and the
new settings will take effect.
Bipolar/Unipolar – This selection must be set to match the step
motor valve used on the system. The IB-G supports Sporlan
SER, CDS and SEH series bipolar valves and SER, ESX and
SEV series unipolar valves. Ensure that the valve max steps is
set accordingly; see Table 2.
STD Direction/REV Direction – This selection allows the
valve to operate in reverse direction. STD direction closes
the valve based on increasing control signal. To reverse the
valve direction, turn the DIP switch #5 to “ON”. This selection
does not affect the force close direction when the “CLS” and
“REF”, “OPN” and “REF” or forced close DIP switch #8 is
turned on.
STD Response/Quick – This selection speeds up valve
response to changes in the control signal. Generally, DIP switch
#6 is turned ‘ON’ when used in expansion valve applications.
200pps/400pps – This selection allows bipolar valves to be
operated either at 200pps (pulses per second) or 400pps. DIP
switch #7 can be placed in the ‘ON’ position to enable 400pps.
Generally the faster step rate is used on larger chillers or where
a faster valve open/close time is desired. Note: the faster step
rate is not offered on unipolar valves.
STD Operation/Close Valve – This selection allows for the
valve to be manually closed via DIP switch #8. By turning
this ‘ON’, the valve will move to the 0%, closed position. This
feature can be used for service and troubleshooting. The switch
must be turned to ‘OFF’ to resume normal operation.
4. Troubleshooting
When properly configured and installed, the IB-G requires
no maintenance. There may be instances; however; where
system troubleshooting is required. If a problem arises, it is
recommended to revisit the wiring first to ensure proper
wire location on the terminals and that all wires are tightened
accordingly.
Test the valve:
The resistance of the motor winding may be tested without
opening the system.
1. Remove power from the external controller and IB-G.
2. Remove valve leads from the IB-G.
3. Measure the resistance between black and white leads of
the valve.
• For the SEI, SDR-4, CDS-9 and CDS-17 valves, the
resistance should be 75Ω ±10% at 71°F (21.7°C).
• For the SER-AA thru SER-D, SERI, CDS-4 and CDS-7
valves, the resistance should be 100Ω ±10% at 71°F (21.7°C).
4. Measure the resistance between the green and red leads.
This value should be within ±5% of the resistance between
the black and white leads recorded in step 3.
5. Measure the resistance from any lead to the valve body.
Resistance should be infinite (open).
Table 4
VALVE TYPE
STEP STROKE
MOTOR TYPE
SDR-1x, SDR-2, SDR-2x,
SEI-1/2 thru SEI-11
1596
Bipolar
CDS-2,4,7, SER-AA, SER-A,
SER-B, SER-C, SER(I)-G,
SER(I)-F, SER(I)-J, SER(I)-K
2500
Bipolar
SDR-3, SDR-3x, SEI-30
3193
Bipolar
CDS-9, CDS-16, CDS-17,
SDR-4, SEH
6386
Bipolar
SER-B-U, SER-C-U,
SER-D-U, SER-E-U
1596
Unipolar
ESX, SEV, CEV
500
Unipolar
Status
Valve 100%
Valve Position
Valve Closed