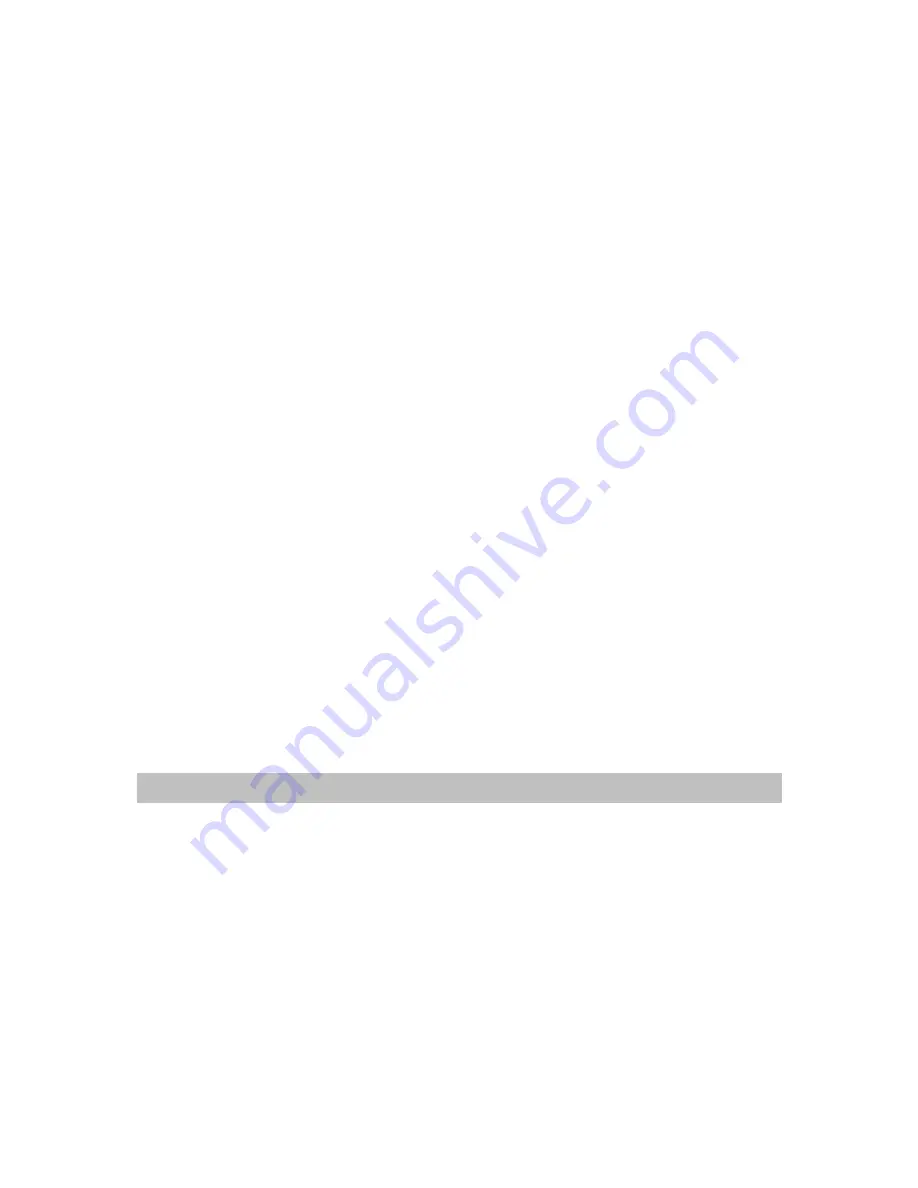
Parker Hannifin S.p.A. - Divisione S.B.C. LVD User’s Manual
51
Pr66:67 Motor position via CanBus
. On receipt of the SYNC (Pb70.8=1) Pr62:63 is copied
into Pr66:67 and, if feedback transmission is enabled (b70.2=1) it is automatically
transmitted via CanBus.
Pr68:69 Master module.
If utilising the electronic cam function in Pr68:69, the master
module must be programmed in steps.
b70.1
Feedback.
Default=0. If set to 0 feedback is provided by the resolver, if set to 1
encoder feedback is adopted (X5); in this latter case parameters Pr58 and Pr59 are
used to standardise pulses/revolution at 4096.
b70.2
Feedback transmission enable
. Default=0. If set to 1, Pr66:67 is transmitted via
CanBus on receipt of the SYNC type 0.
b70.3
Enable real time mode.
Default=0. If set to 1, enable the CanBus real time mode.
b70.4
Low speed mode.
Default=0. If set to 1, the transmission rate of the CanBus real
time mode is 500kbps, otherwise the transmission rate is 1Mbps.
b70.5
Servo error
. b70.5 is set to 1 if the absolute value of the position error exceeds the
value entered in Pr56. If b70.5 is utilised, it must be reset by the user following
servo-errors, e.g. by means of the PLC program.
b70.6
Feedback transmission enable
. Default=0. If set to 1, Pr66:67 is transmitted via
CanBus on receipt of the SYNC type 1.
b70.7
Feedback sampling.
If b70.7 is 0 the position sent back on receiving SYNC frame
has been frozen at previous sampling time of the position loop; if b70.7 is 1 the
position will be frozen on the SYNC received.
b70.8
Axis catch/release
.
On receipt of the SYNC, b70.8 switches to 1; after performing the
SYNC procedure it is automatically reset. The SYNC procedure copy Pr55 on Pr54, Pr65:64
on Pr61:60 and Pr63:62 on Pr67:66.
b70.9
Cam encoder master.
Default=0. If b70.9=0, X5 is the encoder master input for the
electronic cam; if b70.9=1 a virtual encoder master is enabled and Pr51 define the
speed.
b70.10 Reset type 1
. Resets the motor position and reference.
b70.11 Reset type 2
. Sets motor position and reference to the absolute shaft position.
b70.12 Reset type 3
. Sets reference to motor position.
b70.13 Cam stop.
When this bit is set to 1 the cam is stopped at the end of the module.
b70.14
Start 32 point cam.
b70.14 = 1 initialises and activates the 32 point cam.
b70.15
Start 128 point cam.
b70.15 = 1 initialises and activates the 128 point cam.
3.16 Block diagrams
The main block diagram provides a graphic description of how to use the drive. Each rectangular
block represents one or more read/write parameters, each rhomboid shape represents read-only
parameters. In the diagram there are other functional blocks such as: greater than..., equal to, the
smallest among..., logical and/or; we have used standard symbols for all these blocks. Binary
parameters are shown as switches and the position depicted is the default value.