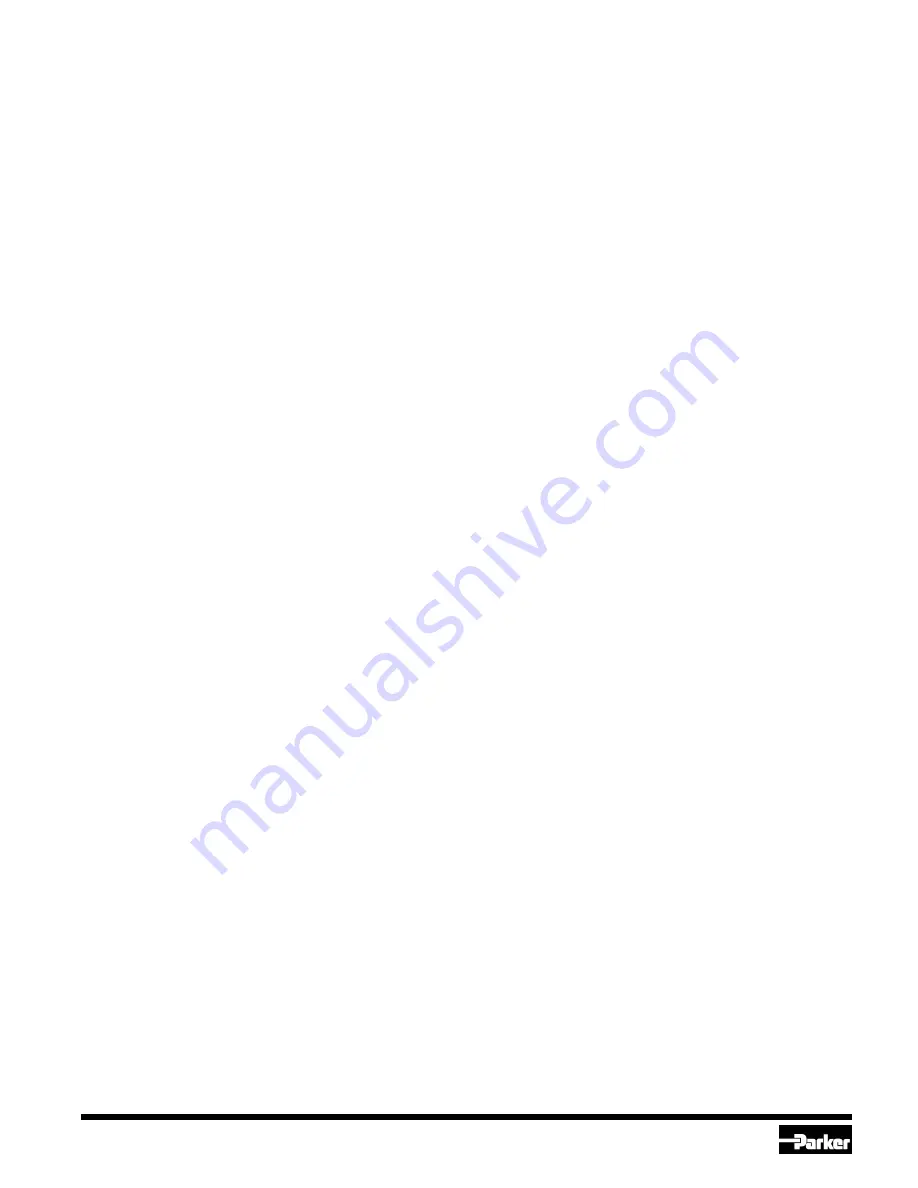
Refrigerating Specialties Division
9
Next the probe should be zeroed. This is especially important if the
column is something other than 4" (100mm) in diameter and/or if the
application utilizes a halocarbon refrigerant. If the probe is not zeroed
properly several readjustments of the “Zero” and “Gain” control may
be necessary since the “Zero” adjustment will effect the “Gain” and
the “Gain” adjustment will effect the “Zero”. With a halocarbon
refrigerant, if the span (gain) a adjustment is not made at the probe, a
large adjustment to the “Gain” will have to be made at the controller.
This is what makes the zeroing of the probe so important. To zero the
probe, wire the probe into the Controller (as described earlier) and
check the reading on the Controller LED (or use a voltmeter and check
the voltages at the probe connector or controller as described earlier)
when there is no refrigerant in the column. The LED should read
approximately zero (or the voltage should read between -.005 and
+.005 volts D.C.). If a reading other than zero is present, adjust the
“Zero” pot on the probe circuit board until it is correct. Remember, the
“Zero” LED on the probe circuit board will light up below approximately
zero volts.
Next, fill the vessel and the Pipe Column to a known level at or above
the 50% level. Ideally, this would be at the center of a sight glass. The
LED should now be at a per cent level that corresponds with the level
of the liquid. If not, adjust the “Gain” screw on the front panel of the
controller until the LED agrees with this known level of the refrigerant.
If the adjustment makeup is more than 10%, which will be the case if
Freon is used as a refrigerant, this adjustment should be made at the
probe with the “Span” (gain) adjustment pot for the most accuracy. If
the adjustment is to be made at the probe, the return voltage from the
probe should be checked to make sure that it matches the LED reading
on the Controller. (For example, a .5 volt return signal should read 50
per cent on the LED). If these two readings do not match, the “GAIN”
control on the front panel of the Controller should be adjusted until
they do.
There are three ways that the probe span can be adjusted. The first
would be to make the adjustment at the probe and have someone
watch the LED or voltmeter at terminals 1 and 3 at the controller until
the reading matched what is actually in the column. The second would
be to take the voltage reading at the probe Q/D connector as described
earlier. In this case the voltage reading at the probe should correspond
to the level in the column (For example: .5 volts = 50%, 1 volt = 100%,
etc.). The third approach, though not always practical, would be to
have the ability to fill the column to the 100 per cent level and then
turn the span adjustment at the probe until the span LED lights up,
since the LED lights up when the return voltage goes over 1 volt. One
volt would show up as 100% on the Controller. An arrow at the top of
the LED indicates that the liquid reading is above the 100 per cent
level. Caution: If this method is used, make sure the column is not
filled completely with liquid refrigerant and isolated, so that liquid
expansion could occur. The controller is now calibrated to agree with
the particular field conditions.
It should be noted that in a few cases where Freon is used as a
refrigerant the “Span” adjustment at the probe may not make it up to
the voltage desired. If this is the case adjust the span on the probe as
high as possible and then the “Gain” on the Controller should be
adjusted until the level on the LED matches the level in the column.
The percent of liquid level shown on the LED is a percent of the Active
Length of the Probe, which may not be the same as the total height of
the vessel. The setting of the “Gain” adjustment is greatly simplified if
one or more sight glasses have been installed in the Pipe Column at
heights which correspond exactly to even percentage numbers of the
Probe Active Length. See Fig. 2 and the text on page 2 which describes
how this can be done.
ADJUSTING OPERATING LEVEL: The Level Control operates one
relay with the ability to adjust its differential to as much as 98% or as
little as 2% of its HIGH LEVEL SETTING. Each Auxiliary Switch also
operates one relay, but the differential is factory set at 4% of total
active length and is non-adjustable.
“TEST” and “SET” SWITCHES: For the Level Control and for each
Auxiliary Switch there is a three position toggle switch that can be
held in either the “Test” or the “Set” position, but is spring loaded to
return to the middle or normal run position when released.
The purpose of the “TEST” position is to check the operation of the
relay and any circuit(s) connected to it. When in the “Test” position the
relay is energized. (Except for the Level Control “High Test” position
which is
de-energized because this is its normal functioning position that
must be checked.) When the toggle is released the relay may or may not
change position depending upon the existing level of the liquid and the
actual set-point of the switch.
With the toggle held in the “SET” position the adjusting screw below
the toggle can be turned to adjust the set-point, which will be seen on
the LED as the adjustment is made. While this is being done, with the
toggle in the “SET” position, the coil of the relay will be de-energized
and its contacts will be in their normal position. Also, after a set-point
has been made, that set-point can be recalled by moving the toggle to
the “SET” position. Usually the operator will mark the “SET” point on
the silver writing surface after the setting has been made and confirmed
to be right.
LEVEL CONTROL ADJUSTMENT: The Controller MUST BE
CALIBRATED BEFORE ATTEMPTING TO MAKE ANY
ADJUSTMENTS. (See also “Calibration”). Set the Level Control “High”
set-point first. Hold the toggle in the “Set” position and turn the
adjustment screw until the LED indicates the desired set-point. This
can be set at any level between 0 and 100% of the active probe length.
The Level Control “Low” set-point adjustment is actually a differential
adjustment and can be set at any level between 2% and 98% of the
“High” set-point. Subsequent changes of the Level Control “High” set-
point will require a recheck (or resetting) of the “Low” set-point.
While SETTING the Level Control “High” and “Low” set-points the relay
will be de-energized and the set-points only are shown on the Digital/
Bar Graph Display. While TESTING the “High” the relay is de-energized;
while TESTING the “Low” the relay is energized.
ADJUSTING AUXILIARY SWITCHES 2, 3, 4 and 5: The set-point
range of the auxiliary switches is 0 to 100% of the active probe length.
To set the “Low” level hold the low level toggle in the “Set” position and
turn the adjustment screw below the toggle. To set the “High” level
hold the high level toggle in the “Set” position and turn the adjustment
screw below the toggle.
The “High” level, obviously, must always be set above the “Low” level.
While setting the levels the relays will be de-energized and the
set-points will be shown on the Digital/Bar Graph.
MARKING SURFACES: The silver colored surfaces on the face of
the Controller are prepared to accept marking with a soft pencil. Thus,
when settings have been made and purposes selected for the Control
Level or the auxiliary switches, notations can be written on the panel
to suit a specific set of circumstances. These notations can be erased
and changed as required.
CAUTIONS: While holding a toggle in a “Set” position it is keeping
that relay in a de-energized mode. It is IMPORTANT to make sure
that the level of the liquid in the vessel DOES NOT go beyond a safe
point during this time.
When a toggle is in the “Test” position it is energizing the relay (except
during testing of the Level Control “High” position when the relay is
de-energized) and whatever is connected to that relay is also being
operated. Thus, an alarm will “sound” if it is connected to that relay, or
lights will turn “On”, or if the compressor or pump is to shut down, it
will do so. However, how a relay is wired, normally opened or normally
closed, will determine the result of that switching action.
ALL LEVEL SETTINGS must be made AFTER the “Zero” and “Gain”
adjustments have been made since the relay trip settings are related
to this basic calibration of the Controller.
Содержание ELL-1
Страница 3: ...Refrigerating Specialties Division 3...
Страница 6: ...Refrigerating Specialties Division 6...
Страница 8: ...Refrigerating Specialties Division 8 Electronic Liquid Level Kits 204643...
Страница 10: ...Refrigerating Specialties Division 10...