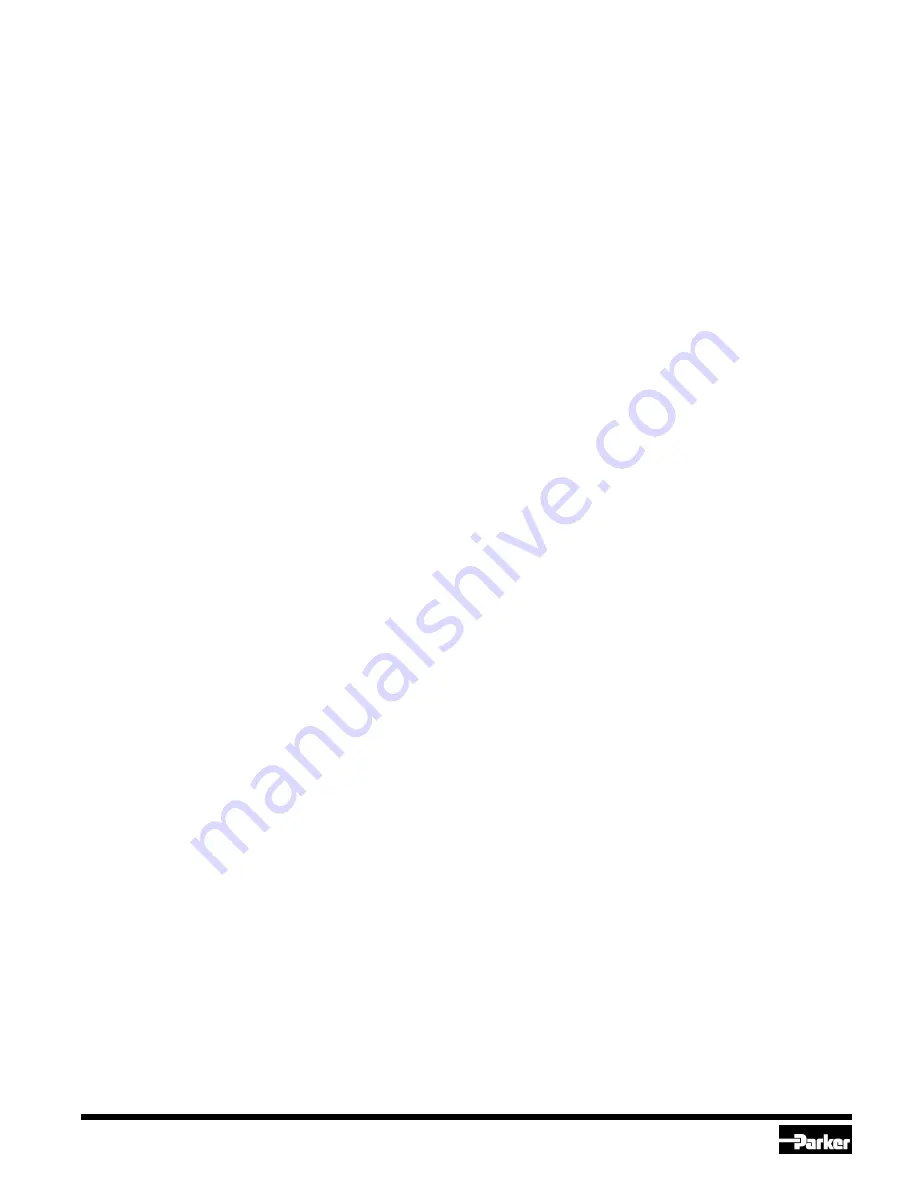
Refrigerating Specialties Division
5
top of the pipe column where it is welded in position in a manner
similar to a butt weld joint with a backup ring. The engagement length
of the Fitting will assist in proper alignment with the pipe column. Two
fittings are available: One intended for U.S. Standard Schedule 40, 3"
or 4" pipe and one intended for 75 mm or 100 mm metric tubing. The
top of the active length of the probe will be 3/4" (1.9 cm) below the top
surface of the Pipe Column Fitting.
The top of the Pipe should be cut square and ground with a 37.5
degree bevel to match the bevel on the Fitting. The Pipe Column Fitting
is made of C 1018 steel.
Insert the Probe Assembly into the 1" - 12 Machine Screw Thread
with gasket in place (not a pipe thread) and tighten to a torque of 75 ft.
lbs. or 10.4 M. kg. The terminal box is rigidly fastened to the threaded
steel attachment so do not attempt to turn the terminal box to a different
position or to tighten the threaded Probe Assembly joint by applying
torque to the terminal box.
If the Pipe Column has refrigerant pressure in it, this must be bled
before loosening the Probe Assembly.
Pressure test the Pipe Column system for leaks.
CONTROLLER: See Fig. 1. The Controller should be installed in a
convenient, safe location where it will not be vulnerable to damage by
material handling equipment, where it can be easily seen by those
concerned with management of the refrigeration system and within a
reasonable and sensible distance from the Probe Assembly. Allow
space below the Controller for connection of the Cable and other
electrical wires.
PROBE CABLE: R/S provides a 30 ft. length of cable complete with
probe end connector, which can be shortened as required at the
controller end. The controller electronics will permit the controller and
probe to be as much as 5000 ft. apart. For installations requiring more
than 30 -ft. of cable, the probe should be ordered with the female end
of the connector only and the required cable purchased from a separate
source. The four wire cable used is stranded 22 AWG communications
cable. The maximum voltage applied to the cable is 15 volts.
PROBE CONNECTORS: Figure 5 describes how to wire the cable to
the connector. Also shown is the terminal orientation at the probe
assembly. The orientation of the housing when it is installed over the
terminal block will determine the way the housing faces when it is
plugged into the probe assembly. The field conditions at the probe
should be considered when determining the orientation of the
connector. For example, with outdoor installations where the probe
connection is exposed to the elements, it is advisable to install the
strain relief facing downwards to prevent moisture from penetrating
through the cable seal. Consideration should also be given to those
installations where the probe might come in contact with water if the
area is being hosed down for cleaning purposes (such as conveyor
belts in close proximity to vessels). The most reliable way to keep
water out is to use conduit. Use figure 4 as a guide to wire the probe
into the controller. The cable should be fed through the strain relief on
the controller. The cable should be fed through the strain relief on the
controller enclosure and connected to terminal block number 1 (TB1).
The connection is shown in figure 1. Tighten the strain relief so that
the cable is not inadvertently pulled out.
USE OF CONDUIT: The design of the ELL allows for the use of 1/2"
conduit if local electrical code or specifications require it. The hole in
the controller where the strain relief is located is 13/16" (2.06 cm)
diameter. If conduit is desired, the strain relief can be removed and a
conduit connection can be made at that point. At the probe end, the
conduit connection is made by removing the strain relief nut, grommet,
and washer from the female Q/D connection.
POWER CONNECTIONS: See Fig. 4. Connect the correct single phase
current to terminal block TB3, terminals 1, 2 and 3. Terminals 1 and 3
are used for the 110/50, 120/60 or 240/60 power lines. For either 110V
or 120V terminal 1 or 3 can be the neutral. TERMINAL 2 should be
used ONLY for the GROUND or EARTH CONNECTION.
All units may be used with any of the power sources listed above, but
it is necessary to BE SURE THE SHUNT PLUG ABOVE TB3 IS IN
THE CORRECTION POSITION. With the Shunt Plug in the left hand
position, “120 VAC” is revealed at the right hand end of the plug and
the Controller is suitable for either 110V/50Hz or 120V/60Hz power
supply. With the Shunt Plug right hand position, “240 VAC” is revealed
at the left hand end of the plug and the Controller is suitable for 220V/
50 Hz or 240V/60 Hz power supply. THE SHUNT PLUG MUST BE IN
THE PROPER POSITION BEFORE THE ELECTRIC POWER IS
CONNECTED TO THE CONTROLLER.
The position of the Shunt Plug is changed by pulling it out away from
the panel, repositioning one place to the left or right as may be required
and re-inserting into the shunt receptacle. CONNECTING THE
WRONG SUPPLY VOLTAGE TO THE CONTROLLER MAY DESTROY
THE PRINTED CIRCUIT BOARD.
4-20 MILLIAMP SIGNAL CONNECTION: The terminals for the 4-20
milliamp signal are located on the front of the main circuit board of the
controller. The signal can be obtained from terminals 7 and 8 at terminal
block number one (TB1). The location is shown in figure 4. The 4-20
milliamp signal and the relay operation are based on the reading of
the liquid crystal display on the front panel. Terminal number 7 is the
positive and terminal 8 is the negative. The signal is D.C.
See also page 6, Fig. 7 for typical suggested wiring diagrams.
Adjustment
Once the unit is calibrated all adjustments are made at the controller.
See fig. 1 which illustrates the ELL-3 five level Controller cover panel.
The ELL-1 and ELL-2 are similar except that the quantity of auxiliary
switch sections is reduced to suit the particular Controller. All
adjustments are made with a small flat tip screwdriver.
CALIBRATION: At start-up time the factory calibrations should be
checked to coincide with the actual field conditions. This is done with
the adjustments marked “Initial Calibrations Only” on the controller
and the adjustment pots located on the probe circuit board (see figure
6). The probe will be calibrated at the factory for a 4" (100mm) column
with ammonia as the refrigerant. If the probe is installed in a smaller
diameter column the probe will read above zero with the column empty.
The smaller the column diameter, the higher the reading on the Light
Emitting Diode (LED) will be until the unit is properly zeroed. If Freon
is used as the refrigerant instead of ammonia the “Gain” on the front
panel and/or probe will have to be raised significantly since Freon has
a lower capacitance than ammonia.
The probe has two adjustment pots with two Light Emitting Diodes
(LEDs) located on its circuit board (see fig. 6). One adjustment pot
and LED is used for zeroing the probe and the other adjustment pot
and LED is used for setting the probe span (gain). The “Span”
adjustment pot will probably never have to be adjusted. The supply
signal to the probe is plus 15 volts and minus 15 volts D.C. When
adjusted properly the probe sends a zero to one volt signal back to
the controller. The “Zero” LED comes on when the probe return voltage
falls below approximately zero volts. The “Span” LED comes on when
the probe return voltage goes above approximately one volt.
Although not always required, it helps to have a digital volt meter
during the set-up of the ELL. There are two locations on the ELL where
probe input and output voltages can be checked during set up or while
troubleshooting. At the controller, voltages can be read at terminal
block number one (TB1). The zero to one volt return signal is at
terminals 1 and 3 (see fig. 4). At the probe, these voltages can be
read from inside the female Q/D connector (see fig. 5, Q/D wiring
instructions). The zero to one volt return signal is at terminals 1 and
common (shown as ground on the terminal block). The zero to one
volt return signal corresponds to approximately zero to 100% on the
controller LED when the unit is properly calibrated.
The controller zero should be checked first. Check the position of the
shunt plug (as it should correspond to supply voltage) and connect
power to the Controller, but leave the probe disconnected from the
Controller. The Digital should read zero and there should be no sign
at the left of the LED. If it is not at zero, or if there is a minus (-) sign at
the left of the LED, turn the “Zero” adjusting screw (located on the
front panel of the Controller) to make the LED read approximately
zero.
(continued page 9)
Содержание ELL-1
Страница 3: ...Refrigerating Specialties Division 3...
Страница 6: ...Refrigerating Specialties Division 6...
Страница 8: ...Refrigerating Specialties Division 8 Electronic Liquid Level Kits 204643...
Страница 10: ...Refrigerating Specialties Division 10...