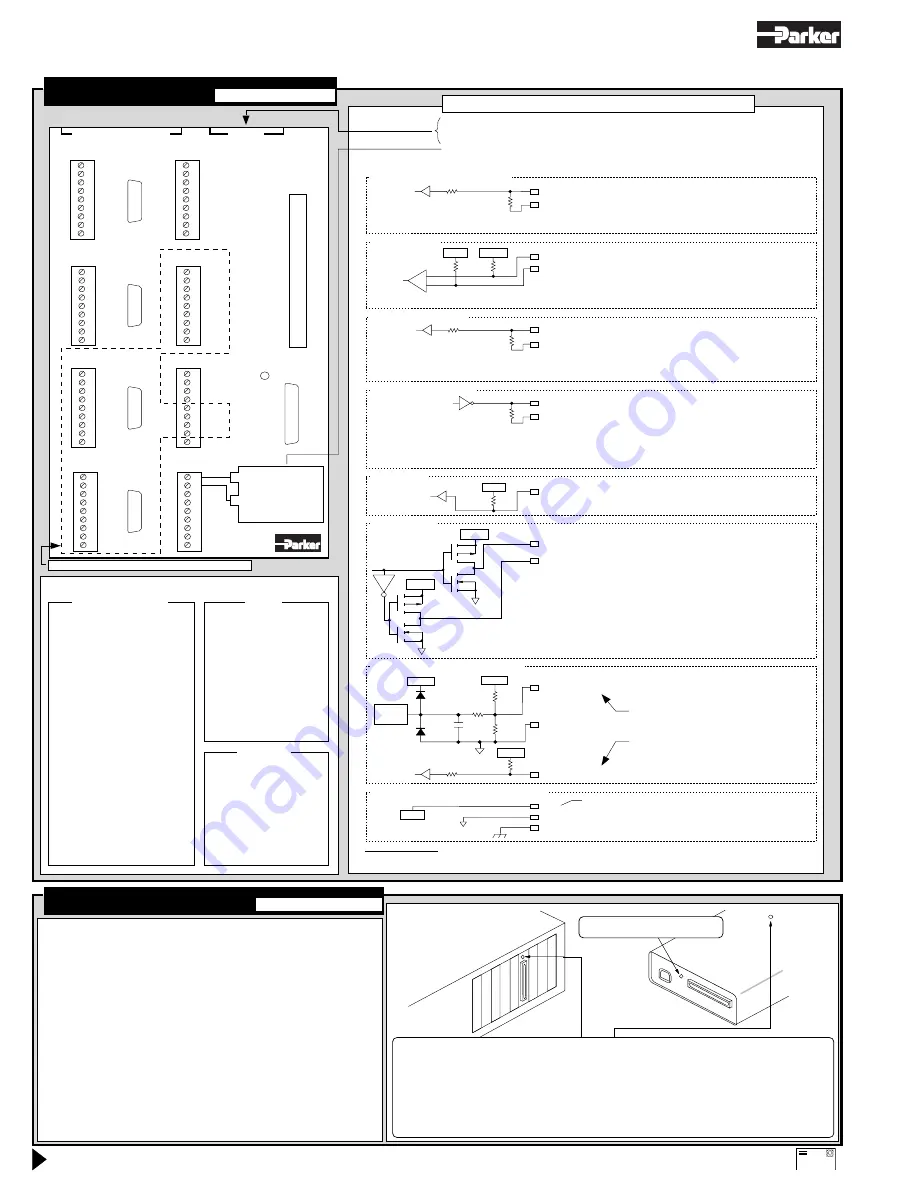
AT6200 & AT6400 Indexers
Automation
AT6n00
ENCODER 4
ENCODER 3
ENCODER 2
ENCODER 1
3POS
3NEG
3HOM
GND
4POS
4NEG
4HOM
GND
SHLD
LIMITS 1/2
TRG-A
GND
TRG-B
GND
TRG-C
GND
TRG-D
GND
SHLD
1
+5V
GND
+5V
OUT-P
IN-P
GND
AUX-P
P-CUT
GND
n-AXIS INDEXER
AC INPUT
1POS
1NEG
1HOM
GND
2POS
2NEG
2HOM
GND
SHLD
1
D
R
I
V
E
1
D
R
I
V
E
2
D
R
I
V
E
3
D
R
I
V
E
4
STATUS
SHLD
GND
Z-
Z+
B-
B+
A-
A+
+5V
1
SHLD
GND
Z-
Z+
B-
B+
A-
A+
+5V
1
SHLD
GND
Z-
Z+
B-
B+
A-
A+
+5V
1
SHLD
GND
Z-
Z+
B-
B+
A-
A+
+5V
1
LIMITS 3/4
1
1
1
2
2
TRIGGERS
AUXILIARY
49
50
49
50
GREEN : READY
RED : NOT READY
OFF: NO POWER
P
R
O
G
R
A
M
M
A
B
L
E
O
U
T
P
U
T
S
P
R
O
G
R
A
M
M
A
B
L
E
I
N
P
U
T
S
J
O
Y
S
T
I
C
K
External
DC power input
(+5VDC @ 1.6A)
Required for DC AUX boards;
power input alternative for AC
AUX boards.
+
–
1
Internal Schematics
POS, NEG, HOM, P-CUT, or TRG-x
6
.
8 K
Ω
74HCxx
47 K
Ω
ISO GND
Chassis GND
+5VDC
GND
AUX-P (connect to the +5V terminal on the AUXILIARY
connector, or to an external supply of up to 24VDC)
Specs: HCMOS-compatible*; voltage range = 0-24VDC.
Limits, P-CUT, & Trigger Inputs
+1.8VDC
22 K
Ω
–
+
22 K
Ω
+5VDC
+5V
SHLD
5V Load Limit (for all I/O connections):
1.5A for AT6400-120; 1.0A for AT6200 AC &
AT6400-240. Limit for DC AUX boards depends on
external power supply.
Specs: Differential comparator. Use 2-phase quadrature encoders;
max. frequency = 1.6 MHz; min. time between transitions = 625 ns.
TTL voltage levels (Low
≤
0.4V, High
≥
2.4V); range = 0-5VDC.
A–, B–, or Z–
A+, B+, or Z+
Encoder Inputs
Terminals found on multiple connectors
Specs: Differential line driver output.
Signal high
≥
3.5VDC @ +30mA; signal low
≤
1.0VDC @ -30mA.
+output for each differential driver is active high;
-output for each driver is active low.
Step pulse width is 0.3 µs to 20 µs (depends on the value of the
PULSE command—default is 0.3 µs).
Step+, Di, or S (pins 1, 2, or 11)
Drive Outputs
+5VDC
GND
GND
+5VDC
Step–, Direction–, or Shutdown– (pins 9, 10, or 12)
+5VDC
1 K
Ω
74HCxx
Specs: HCMOS-compatible*; voltage range = 0-5VDC.
Drive Fault or In-Position (pin 5 or 4)
Drive Inputs
General-purpose Programmable Input
6
.
8 K
Ω
74HCxx
47 K
Ω
IN-P (Connect to the +5V terminal on the AUXILIARY connector,
or to an external supply of up to 24VDC. To sink current, connect
to a GND terminal.)
Specs: HCMOS-compatible*; voltage range = 0-24VDC.
Programmable Inputs
General-purpose Programmable Output
4
.
7 K
Ω
7 4 0 6
(open collector)
OUT-P (connect to the +5V terminal on the AUXILIARY
connector, or to an external supply of up to 24VDC)
Specs: Open collector output.
Max. voltage in OFF state (not sinking current) = 24V,
max. current in ON state (sinking) = 30mA.
Programmable Outputs
150 K
Ω
49
.
9 K
Ω
0
.
1 µF
10
.
0 K
Ω
35 V
35 V
+5VDC
8 Channel
8-bit
A/D
Converter
ISO GND
Specs: Voltage range = 0-2.5VDC, 8-bit.
Must not exceed 5VDC.
Analog Channel Inputs (pins 1-4)
Joystick Analog and Digital Inputs
Ground (pin 14)
Axes Select, Velocity, Release, Trigger, or Auxiliary (pins 15-19)
6
.
8 K
Ω
74HCxx
47 K
Ω
+5VDC
+5VDC
Specs: HCMOS-compatible*; voltage
range = 0-24VDC.
Power Input:
AT6200 AC AUX Board............90-264VAC, 50/60 Hz, 0.75A @ 240VAC, single-phase.
AT6400 120V AUX Board........90-132VAC, 50/60 Hz, 1.5A @ 120VAC, single-phase.
AT6400 240V AUX Board........90-264VAC, 50/60 Hz, 0.75A @ 240VAC, single-phase.
AT6n00 DC AUX Board...........+5VDC (
±
5%) @ 1.6A (connect to the AUXILIARY connector).
* HCMOS-compatible levels: Low
≤
1.00V, High
≥
3.25V.
Compumotor
CONNECTOR TO MAIN BOARD
Troubleshooting
See also pages 23-28
Connections
See also pages 7-20
Pin
Function
49
+5VDC
47
Input or Output #1 (LSB)
45
Input or Output #2
43
Input or Output #3
41
Input or Output #4
39
Input or Output #5
37
Input or Output #6
35
Input or Output #7
33
Input or Output #8
31
Input or Output #9
29
Input or Output #10
27
Input or Output #11
25
Input or Output #12
23
Input or Output #13
21
Input or Output #14
19
Input or Output #15
17
Input or Output #16
15
Input or Output #17
13
Input or Output #18
11
Input or Output #19
9
Input or Output #20
7
Input or Output #21
5
Input or Output #22
3
Input or Output #23
1
Input or Output #24 (MSB)
Even numbered pins are
connected to logic ground.
PROGRAMMABLE
INPUTS & OUTPUTS
Pin
Function
1
Step +
2
Dir
4
In-Position
5
Drive Fault
7
+5VDC Output
8
Shield (chassis gnd)
9
Step Return (–)
10
Direction Return (–)
11
Sh
12
Shutdown Return (–)
13
Isolated Logic gnd
14
Isolated Logic gnd
DRIVE
Pin
Function
1-4
Analog Channels 1-4
8
Shield (chassis gnd)
14
Isolated Logic gnd
15
Axes Select Input
16
Velocity Select Input
17
Release Input
18
Trigger Input
19
Auxiliary Input
23
+5VDC Output
JOYSTICK
Pins 5-7, 9-13, 20-21, 24-25 are reserved
Pins 3, 6, & 15 are reserved
PIN OUTS FOR “D” CONNECTORS
Dashed line denotes features not available on the AT6200.
AUX
Board
PC-AT
Green:High
density
cable
connected.
OFF:Cable not connected properly.
After applying power, the status LED on the AT6n00 PC card will be off and the status LED on the AUX board should be red. If
the LED on the AUX board is off, the AUX board does not have AC power.
After downloading the operating system, the status LEDs on the AUX board and the PC card will turn green indicating the
system is ready for operation. If both status LEDs do not turn green after downloading the operating system, an error has
occurred. The download program (
AT6400
) issues an error message if it cannot find the card or if the download operation is not
successful (refer also to the troubleshooting information in Chapter 2, Troubleshooting).
Board Monitor Alarm (BMA): Detects un-recoverable faults in hardware and software. When the BMA detects fault, the status
LED on AT6n00 PC card turns off. The BMA can be reset by cycling power to the PC-AT, or by re-downloading the AT6n00
operating system.
• LEDs – see illustration (right).
• Status information (see descriptions in
6000 Series Software Reference ):
Axis status (general problem conditions)...
TAS
command
Joystick analog voltage..............................
TANV
command
Joystick digital inputs.................................
TINO
command (bits 1-5)
Limit switches.............................................
TLIM
command
P-CUT input...............................................
TINO
command (bit 6)
Programmable and trigger inputs...............
TIN
command
Programmable outputs...............................
TOUT
command
• P-CUT input terminal must be grounded to GND terminal to allow motion.
• Programmable input functions (
INFNC
command) and drive fault detection
will not be operable until you enable input functions with the
INFEN1
command.
• Incorrect drive fault level (
DRFLVL
command) will prevent motion.
• To help prevent electrical noise, shield all connections at one end only.
• Error messages while programming or executing programs – see the
6000
Series Programmer's Guide.
• Download errors – see page 27.
• Address, transfer mode, and interrupt DIP switch settings – see page 4.
• Technical support – see phone numbers on inside of front cover..›
I/O SPECIFICATIONS AND INTERNAL SCHEMATICS
We welcome your feedback on our products and user guides. Please send your comments to our email address:
Direct your technical questions to your local ATC or distributor, or to the numbers printed on the inside front cover of this document.
Содержание Compumotor AT6200
Страница 5: ......