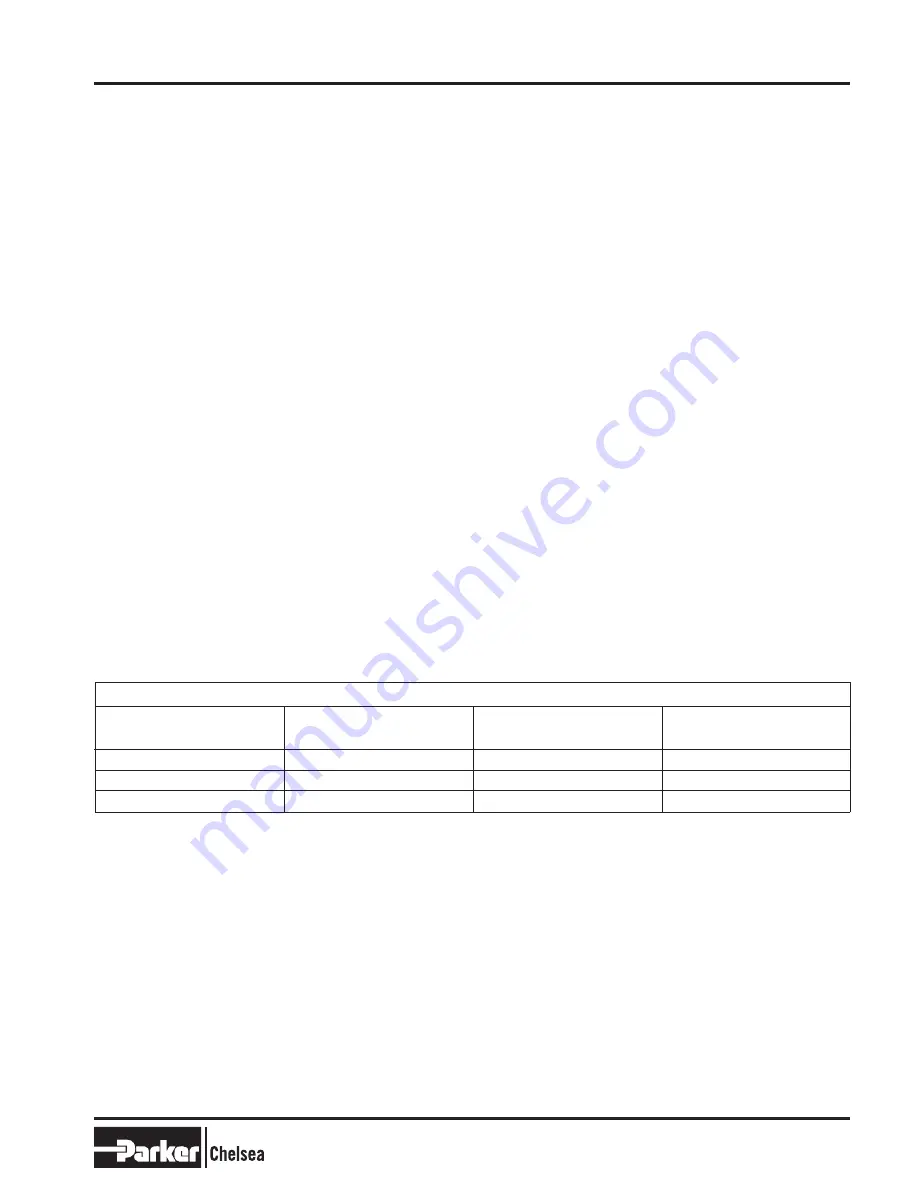
Bulletin HY25-1380-M1/US
Owner’s Manual
Parker Hannifin Corporation
Chelsea Products Division
Olive Branch, MS 38654 USA
7
Installation Instructions
Spicer
®
Universal Joint Operating Angles
Prop.
Max. Normal
Prop.
Max. Normal
Shaft R.P.M.
Operating Angle
Shaft R.P.M.
Operating Angle
3000
5° 50'
1500
11° 30'
2500
7° 00'
1000
11° 30'
2000
8° 40'
500
11° 30'
Above based on angular acceleration of 100 RAD/SEC
2
An auxiliary power shaft transmits torque from the power source to the driven accessory.
The shaft must be capable of transmitting the maximum torque and R.P.M. required of the
accessory, plus any shock loads that develop.
An auxiliary power shaft operates through constantly relative angles between the power source
and the driven accessory, therefore, the length of the auxiliary power shaft must be capable of
changing while transmitting torque. This length change, commonly called “slip movement”, is
caused by movement of the power train due to torque reactions and chassis deflections.
Joint operating angles are very important in an auxiliary power joint application. In many cases,
the longevity of a joint is dependent on the operating angles. (See chart below)
This information is limited to 1000 through 1310 series applications. For applications requiring a series
larger than 1310, contact your local Chelsea distributor
.
Determining Shaft Type
1) Solid or tubular?
a) In applications requiring more than 1000 R.P.M. or where the application necessitates a highly
bal anced auxiliary power shaft, a tubular shaft should be used.
b) Spicer’s solid shafting auxiliary power joints are designed for 1000 or less R.P.M. intermittent
service such as:
Driving small hydraulic pumps
Driving winches
Driving low speed product pumps
2) Joint Series should be determined using the chart on the following page.
Function of Auxiliary Power Shafts
10-Bolt Powershift P.T.O.s