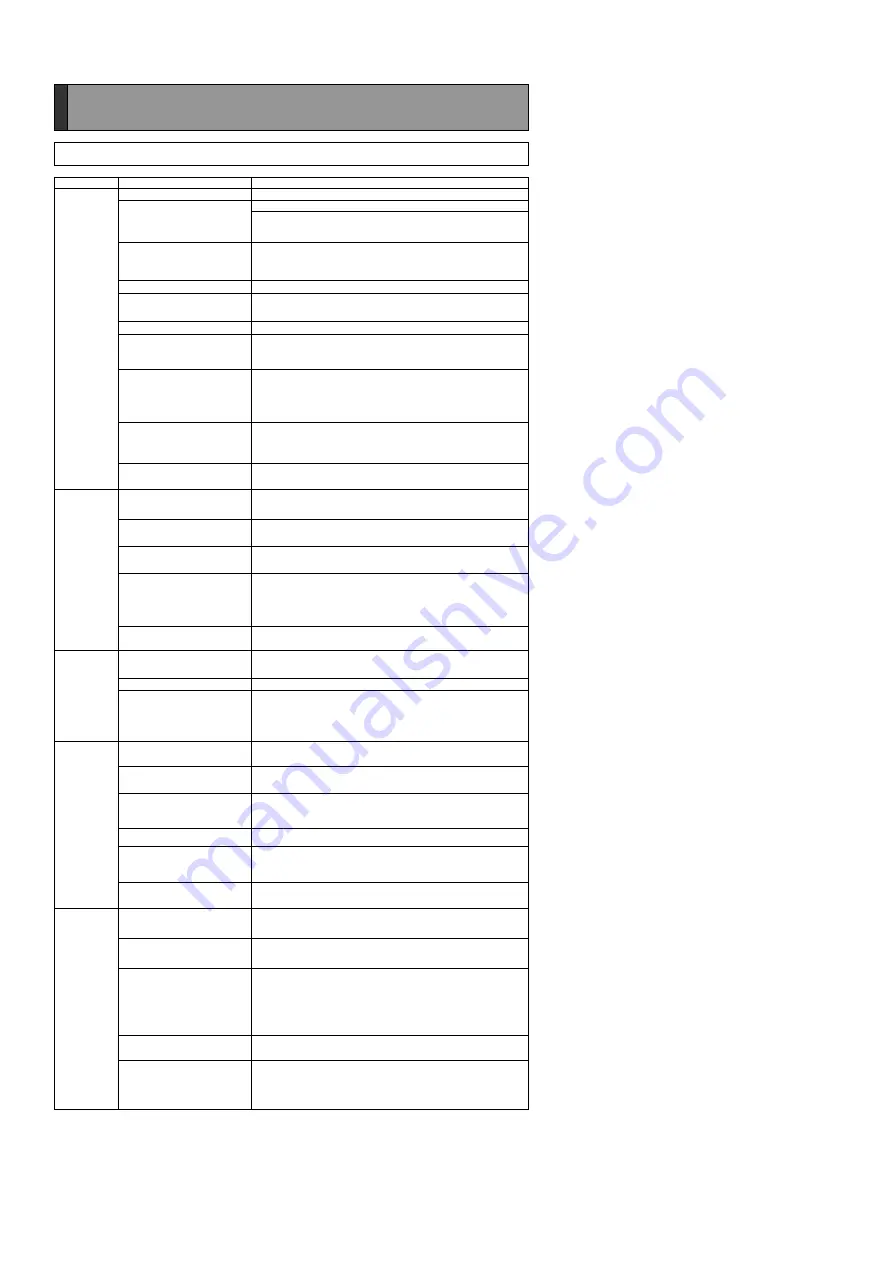
Page
#
Fault Analysis
Fault Analysis
Compressor can
not start
Blown fuse
Air switch tripping
Check the air switch, confirm whether it is the electric type, check whether
there is leakage or short circuit in the power circuit, and repair it in time.
Thermal relay action
Check whether the thermal relay is in the operating state, check the power
loop and confirm the cause of excessive current
Compressor built-in protector
action
The built-in protector is the no output signal alarm, used for the motor
overheating alarm, and it should be measured after the power off and wait
for the compressor body down to room temperature.
Frequently-
started
compressor
Oil blockage in the pipeline with
pressure fluctuation
Check the system pipeline, make the pipeline slope to the compressor, add
the oil storage bend and oil stop bend, improve the pipeline process design,
and re-set up the pipeline.
Temperature difference at the end
of the evaporator is small
Reset the temperature difference setting of the evaporator terminal
controller, and cooperate with the pressure difference controller, so that the
compressor start can be controlled during start delay.
Compressor burn down
Measure whether the resistance between the terminals of the compressor is
normal. If the ground resistance of the short-circuit machine is zero, it is
confirmed as the compressor fault and the compressor needs to be
replaced.
Compressor terminal broken
It may caused by the action of built-in protector of the compressor. It
needs to be measured again when the body temperature of the compressor
drops to room temperature
The load does not match with the
capacity provided
Recalculate the loading system and do the match again.
Compressor fault
The invalid disc seal of compressor makes high and low pressure gas in the
air, and the compressor needs to be replaced.
Poor cooling
of terminal
Loss of terminal cooling capacity
is serious
Whether the cold storage door is opened too frequently, whether the cold
storage has the problem of heat loss, whether the air curtain of the cold
storage is damaged, whether the cold storage door is opened frequently,
whether the cold storage is added with commodities beyond the design
load.
Oil seal in pipeline
Check the system pipeline, make the pipeline slope to the compressor, add
the oil storage bend and oil stop bend, improve the pipeline process design,
re-set up the pipeline
Low suction
pressure of
compressor
Abnormal evaporator
Confirm whether the evaporator is too small, or whether the evaporator is
frosted, whether the evaporator fan is normal, whether the expansion valve
selection is too small, or the expansion valve opening adjustment is too
small.
Compressor
body frosting
with low heat
return degree
Ice-blocked for evaporator
Confirm whether the evaporator defrosting is normal, whether the
evaporator heater is intact, whether the defrosting time and cycle and the
temperature setting at the end of defrosting are appropriate, and whether
the evaporator drainage is abnormal
Controller parameters setting in
error
Reset starting delay parameter of compressor
The solenoid valve at the end of
the evaporator is not closed tightly
Check the solenoid valve and replace it after confirming the defect.
Liquid return system
Since system return liquid can implement bad impact on the terminal
cooling, system expansion valve should be adjusted to avoid return liquid.
Large opening of expansion valve Reconfirm the size of the expansion valve and replace it
System matching problem
If the evaporation terminal is too small, the matching design of the system
shall be re-calculated.
Pressure controller setup problem
Change pressure controller Settings (adjust on-off Settings) to reduce
frequent start-on.
Filter plug
If the system is too dirty or contains too much water, replace the filter until
it is in normal condition
Expansion valve fouled
Disassemble the expansion valve strainer and clean the strainer.
Expansion valve opened too large,
compressor frost
Reduce the opening of the expansion valve until the frost is removed from
the compressor
High sound level of compressor
It is caused by the lack of lubricating oil, and lubricating oil needs to be
added in time.
System valve not open
Confirm if the system valves and solenoid valves are open, one by one
according to the system flow chart.
Lack of refrigerant
Through the sigh glass, there are a lot of bubbles or not all liquid flow, and
on this condition the refrigerant needed to be supplemented.
Replace the fuse
Retest the controlled release loop current to confirm whether it is a control
loop problem
Contactor problem
Check the contactor, whether the contact is adhered, and whether the voltage is too low at the startup moment
Whether the controller is in a
protected state
Check whether there is alarm action
Fault
Cause
Method
Power source fault
Measure power supply voltage, phase sequence, etc
Содержание OCU-R200SF
Страница 27: ...26 Page...
Страница 28: ......
Страница 29: ......
Страница 32: ......
Страница 47: ......
Страница 48: ......
Страница 49: ...MT Scroll Unit...