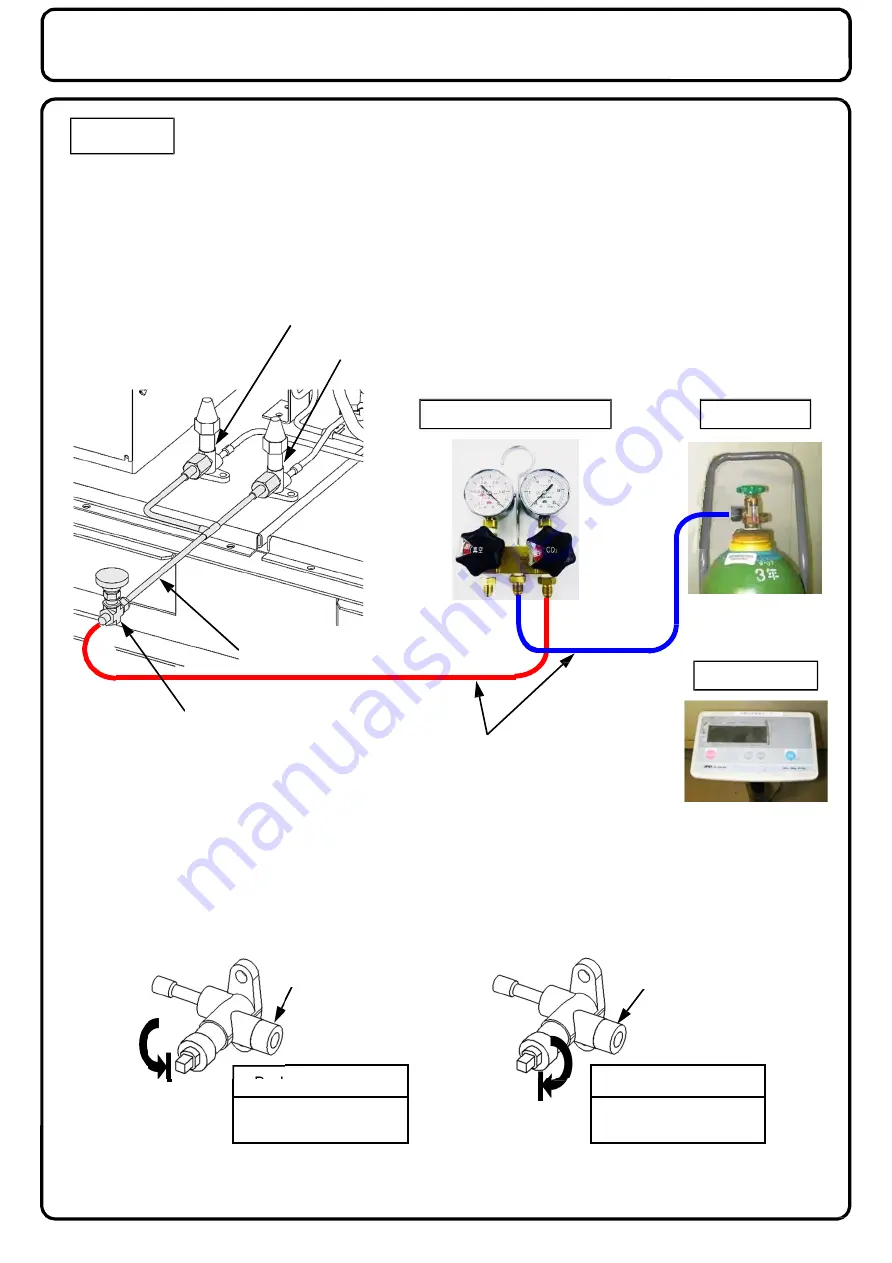
Refrigerant Charging Procedure
3) Check that the joint valve is closed and set the high pressure service valve to the back
seated position (the access port is open), and the low pressure service valve to the front
seated position.
Note:
Do not charge the refrigeration unit with liquid refrigerant from the low pressure side
under any circumstances.
4) Adjust the zero point of the platform scale.
Caution
Make sure to close the vacuum valve of CO
2
manifold gauge set.
1. Preparation for refrigerant charging
1) Connect the joint valve of the service piping (SPK-TU125) and the manifold gauge set
exclusively for CO
2
refrigerant by using a CO
2
charge hose or 1/4" pipe.
2) Place a CO
2
refrigerant cylinder on a platform scale, and connect the manifold gauge set by
using a CO
2
charge hose or 1/4" pipe.
Charging
valve
Low side
gauge
High side
gauge
Platform scale
CO
2
manifold gauge set
Service piping
Joint valve
CO
2
charge hose or 1/4" pipe
Low pressure service valve
High pressure service valve
CO
2
cylinder
Access port is closed.
Front seated positon
Turn the stem fully
clockwise
Back seated positon
Turn the stem fully
counterclockwise
Access port is open.
11
Содержание OCU-CR1000VF8A
Страница 25: ...Exploded View OCU CR1000VF8A 25 ...
Страница 26: ...Exploded View OCU CR1000VF8A 26 ...
Страница 27: ...Exploded View OCU CR1000VF8A 27 ...
Страница 28: ...Memo 28 ...