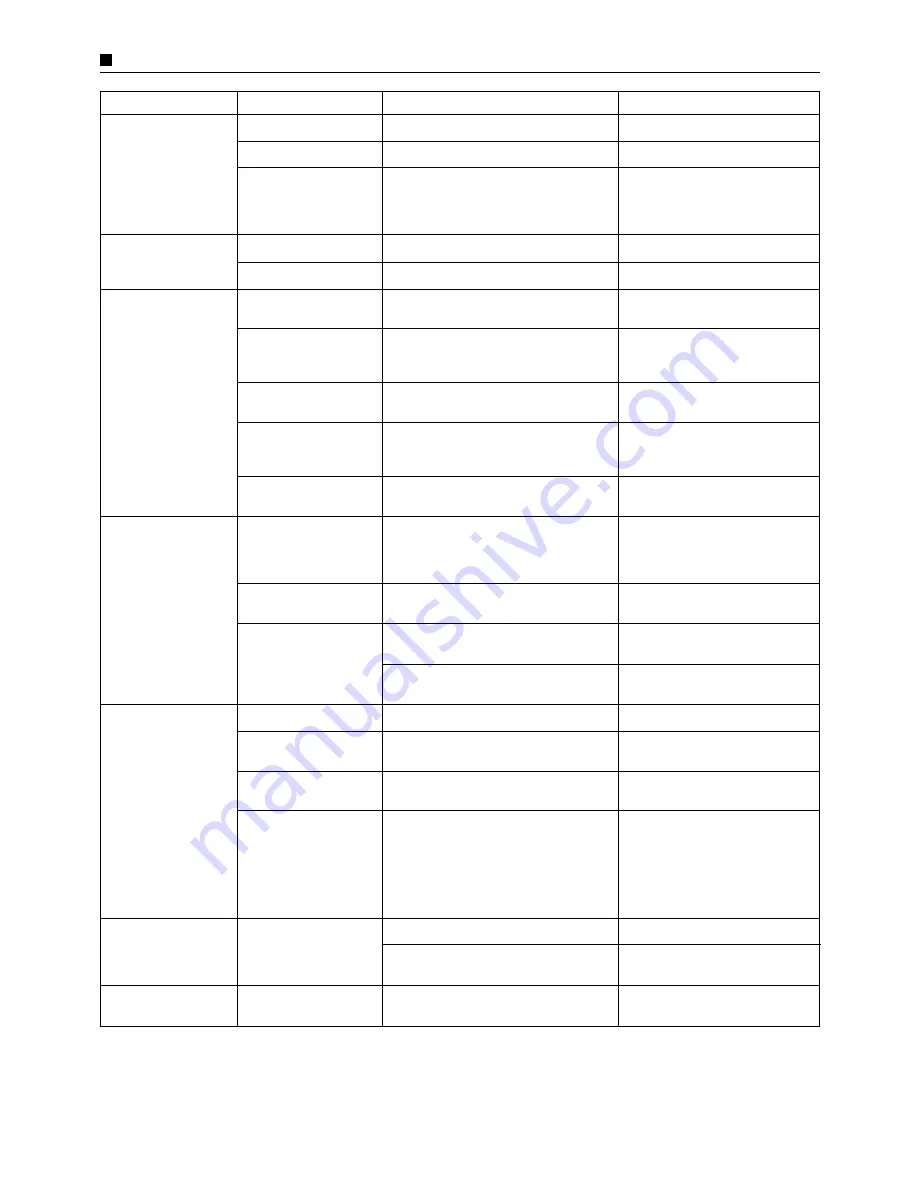
22
CONDITION
CHECKPOINT
METHOD OF INSPECTION
CAUSE / REMEDY
TROUBLE SHOOTING GUIDE
Vacuum cleaner
doesn’t work
Motor abnormal
Motor runs but does
not suction
Noise or vibration
Beater bar does not
rotate
Beater bar does
not stop in upright
position
(*)Dust sensor does
not work properly
Power supply cord
Fuse (Plug for UK only)
Thermal cut-out
Power control
Potentiometer circuit
Hose or suction pipe.
Dust bag / Central filter
Motor continuity
(Mains motor)
Carbon brushes
(Mains motor)
Triac
(Power control circuit)
Dust in motor fan
(Mains motor)
Carbon brushes
(Mains motor)
Beater bar
Beater bar motor
Beater bar ON/OFF
Switch
Beater bar Overcurrent
circuit breaker
Beater bar thermal
cut-out
Safety switch
Dust sensor circuit
Check power supply cord continuity.
Check fuse continuity.
Check thermal cut-out continuity.
Note: Continuity should be checked after
1 hours of removed plug from the mains
socket.
See diagram chart for (Motor abnormal pag. 23)
See diagram chart for (Motor abnormal pag. 23)
Check if there is any blockage in the
hose or suction pipe
Check if dust bag is full or dust
accumulated in central filter.
Check motor continuity across carbon
brush holder tabs.
Check gap between carbon brush and
commutator.
Check triac continuity between (TP5- TP7).
Check dust accumulated in motor fan.
(It could happen if the vacuum cleaner
has been used with a broken bag or
without central filter.
Check uneven wear of carbon brushes.
Check if beater bar unit is correctly
positioned in their holding points.
Check if beater bar holding points are
deformed or broken.
See diagram chart for (Motor abnormal) pag. 23)
Check continuity across ON/OFF
Switch tabs.
Check continuity across circuit
breaker tabs.
Remove thermal cut-out connector and
check continuity between connector
terminals CN22 .
(See schematic diagram)
Note: Continuity should be checked after
1 hour of removed plug from the mains
socket.
Check continuity across safety switch tabs.
Check that safety switch actuator is correctly
assembled.
See diagram chart for (Dust sensor
abnormal pag. 23).
If there is no continuity, replace it.
If there is no continuity, replace it.
If ther is no continuity, replace it.
As indicated on the diagram chart.
As indicated on the diagram chart.
If there is any blockage, remove it.
If paper bag is choked up, replace it.
If central filter is completely dirt, clean
or replace it.
If there is no continuity, replace the
motor.
If there is gap between carbon brush
and commutator, replace both
carbon brushes.
If there is no continuity, replace power
control circuit.
If there is dust accumulated in the
motor fan, replace the motor and
check filter condition. (Never try to
dismantle the motor fan).
If there is uneven wear, replace both
carbon brushes.
If it is not correctly positioned,
reassemble it.
If there are deformed or broken,
replace the cover ass’y.
As indicated on the diagram chart.
If there is no continuity, replace it.
If there is no continuity, replace it.
If there is no continuity, replace it.
If there is no continuity, replace it.
Reassemble it or replace.
As indicated on the diagram chart.
Note: (*) For models MC-E583K, MC-E583 only.
Содержание MC-E581
Страница 15: ...PACKING INSTRUCTIONS 1 2 3 4 ...