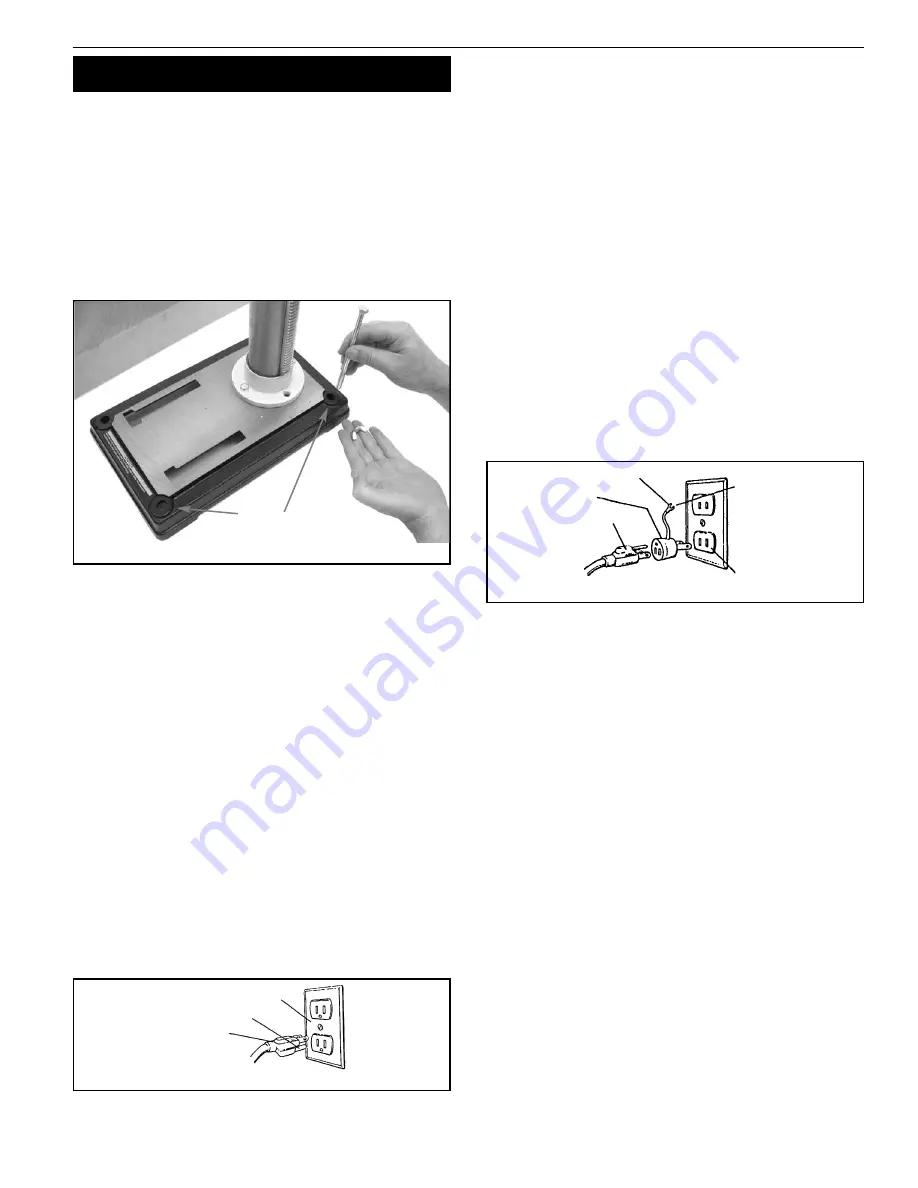
INSTALLATION
MOUNT DRILL PRESS
Refer to Figure 13, page 7.
WARNING:
The drill press must be mounted securely to a stand,
bench or floor to prevent tipping of the machine which could
cause severe personal injury.
•
Drill press must be mounted to flat level surface. Use shims or
machine mounts if necessary.
•
Be sure to bolt drill press to floor or bench securely to prevent
tipping and minimize vibration.
•
Tighten all nuts and bolts that may have loosened during
shipment.
POWER SOURCE
The motor is designed for operation on the voltage and frequency
specified. Normal loads will be handled safely on voltages not
more than 10% above or below the specified voltage.
Running the unit on voltages which are not within the range may
cause overheating and motor burn out. Heavy loads require that
the voltage at motor terminals be no less than the voltage speci-
fied.
Drill press requires a 115 volt, 60 Hz power source.
GROUNDING INSTRUCTIONS
WARNING:
Improper connection of equipment grounding con-
ductor can result in the risk of electrical shock. Equipment should
be grounded while in use to protect operator from electrical shock.
Check with a qualified electrician if grounding instructions are not
understood or if in doubt as to whether the tool is properly
grounded.
This tool is equipped with an approved 3-conductor cord rated up
to 150V and a 3-prong grounding type plug (see Figure 14) for
your protection against shock hazards.
Grounding plug should be plugged directly into a properly
installed and grounded 3-prong grounding-type receptacle, as
shown (Figure 14).
Do not remove or alter grounding prong in any manner. In the
event of a malfunction or breakdown, grounding provides a path
of least resistance for electrical shock.
WARNING:
Do not permit fingers to touch the terminals of plug
when installing or removing from outlet.
Plug must be plugged into matching outlet that is properly
installed and grounded in accordance with all local codes and
ordinances. Do not modify plug provided. If it will not fit in outlet,
have proper outlet installed by a qualified electrician.
Inspect tool cords periodically, and if damaged, have repaired by
an authorized service facility.
Green (or green and yellow) conductor in cord is the grounding
wire. If repair or replacement of the electric cord or plug is neces-
sary, do not connect the green (or green and yellow) wire to a live
terminal.
Where a 2-prong wall receptacle is encountered, it must be
replaced with a properly grounded 3-prong receptacle installed in
accordance with National Electric Code and local codes and ordi-
nances.
WARNING:
This work should be performed by a qualified
electrician.
A temporary 3-prong to 2-prong grounding adapter (see Figure
15) is available for connecting plugs to a two pole outlet if it is
properly grounded.
Do not use a 3-prong to 2-prong grounding adapter unless permit-
ted by local and national codes and ordinances.
(A 3-prong to 2-prong grounding adapter is not permitted in
Canada.) Where permitted, the rigid green tab or terminal on the
side of the adapter must be securely connected to a permanent
electrical ground such as a properly grounded water pipe, a prop-
erly grounded outlet box or a properly grounded wire system.
Many cover plate screws, water pipes and outlet boxes are not
properly grounded. To ensure proper ground, grounding means
must be tested by a qualified electrician.
EXTENSION CORDS
•
The use of any extension cord will cause some drop in voltage
and loss of power.
•
Wires of the extension cord must be of sufficient size to carry
the current and maintain adequate voltage.
•
Use the table to determine the minimum wire size (A.W.G.)
extension cord.
•
Use only 3-wire extension cords having 3-prong grounding
type plugs and 3-pole receptacles which accept the tool plug.
•
If the extension cord is worn, cut, or damaged in any way,
replace it immediately.
EXTENSION CORD LENGTH
Wire Size. . . . . . . . . . . . . . . . . . . . . . . . . . . . . . . . . . . . . . . . . . . . . . . . . . . A.W.G.
Up to 25 ft.. . . . . . . . . . . . . . . . . . . . . . . . . . . . . . . . . . . . . . . . . . . . . . . . . . . . . 18
25-100 ft. . . . . . . . . . . . . . . . . . . . . . . . . . . . . . . . . . . . . . . . . . . . . . . . . . . . . . . 16
100-150 ft. . . . . . . . . . . . . . . . . . . . . . . . . . . . . . . . . . . . . . . . . . . . . . . . . . . . . . 14
NOTE: Using extension cords over 150 ft. long is not recommended.
7
Palmgren Operating Manual & Parts List
80341A & 80342A
Figure 13 - Secure Drill Press to Bench or Stand
Mounting Holes
(Mounting bolts not included)
Figure 14 – 3-Prong Receptacle
Grounding Prong
3-Prong Plug
Properly Grounded Outlet
Figure 15 – 2-Prong Receptacle with Adapter
Make Sure This Is
Connected To A
Known Ground
2-Prong Receptacle
Grounding Lug
Adapter
3-Prong Plug