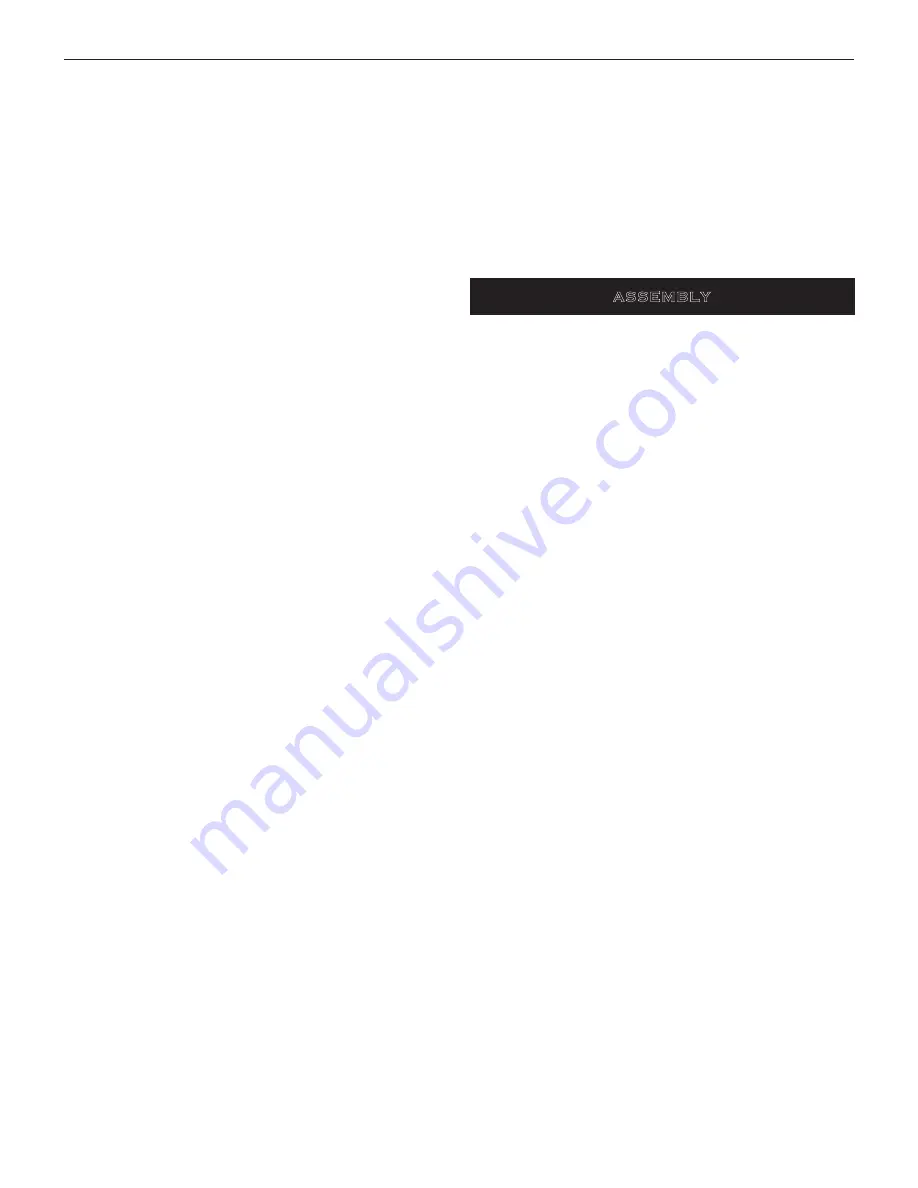
3
Palmgren Operating Manual & Parts List
80177
WORK AREA SHOULD BE READY FOR JOB
●
Keep work area clean. Cluttered work areas and work benches
invite accidents.
●
Do not use power tools in dangerous environments. Do not use
power tools in damp or wet locations. Do not expose power tools
to rain.
●
Work area should be properly lighted.
●
Proper electrical outlet should be available for tool. Three-prong
plug should be plugged directly into properly grounded, three-
prong receptacle.
●
Extension cords should have a grounding prong, and the three
wires of the extension cord should be of the correct gauge.
●
Keep visitors at a safe distance from work area.
●
Keep children out of workplace. Make workshop childproof. Use
padlocks, master switches or remove switch keys to prevent any
unintentional use of power tools.
TOOL SHOULD BE MAINTAINED
●
Always unplug tool prior to inspection.
●
Read operating instructions manual for specific maintaining and
adjusting procedures.
●
Keep tool lubricated.
●
Use sharp cutters and keep the tool clean for safest operation.
●
Remove adjusting tools. Form the habit of checking that
adjusting tools are removed before turning on the machine.
●
Keep all parts in working order. Check to determine that the
guard or other parts will operate properly and perform their
intended function.
●
Check for damaged parts. Check for alignment of moving parts,
binding, breakage, mounting and any other condition that may
affect a tool’s operation.
●
Damaged parts should be properly repaired or replaced. Do not
perform makeshift repairs. (Use the parts list provided to order
replacement parts.)
KNOW HOW TO USE TOOL
●
Use the right tool for the job. Do not force tool or attachment to
do a job for which it was not designed.
●
Disconnect tool when changing accessories such as bits, cutters
and the like.
●
Avoid accidental start-up. Make sure switch is in OFF position
before plugging in.
●
Do not force tool. It will work most efficiently at the rate for which
it was designed.
●
Handle workpiece correctly. Secure work with clamps or vise.
Leave hands free to operate machine. Protect hands from possible
injury.
●
Never leave a tool running unattended. Turn the power off and
do not leave tool until it comes to a complete stop.
●
Do not overreach. Keep proper footing and balance.
●
Never stand on tool. Serious injury could occur if tool is tipped or
if cutter is unintentionally contacted.
●
Keep hands away from moving parts and cutting surfaces.
●
Know your tool. Learn its operation, application and specific
limitations.
●
Feed work into a bit or cutter against the direction of rotation of
bit or cutter.
●
Turn the machine off if it jams. A cutter jams when it digs too
deeply into the workpiece. (The motor force keeps it stuck in
workpiece.)
●
Use recommended accessories.
●
Clamp workpiece or brace against column to prevent rotation.
●
Use recommended speed for drill accessory and workpiece
material.
WARNING:
Think Safety! Safety is a combination of operator common
sense and alertness at all times when drill press is being used.
INSTALL COLUMN TO BASE
Refer to Figure 7.
●
Place base (Ref. No. 3) on flat level surface.
●
Mount column assembly (Ref. No. 7) to base using four hex bolts
(Ref. No. 10).
INSTALL TABLE TO COLUMN ASSEMBLY
Refer to Figure 7.
●
Insert the worm gear (Ref. No. 34) into the table crank handle
hole from inside the table bracket (Ref. No. 25). Make sure the
worm gear (Ref. No. 34) meshes with the inside raising/lowing
gear.
●
Install the table bracket locking handle (Ref. No. 33) into the hole
at the rear of the table bracket (Ref. No. 25).
NOTE:
Install the handle from left to right, so it enters the
non-threaded side of the table bracket first.
●
Place the rack (Ref. No. 13) inside the table bracket (Ref. No. 25),
making sure the worm gear (Ref. No. 34) on the inside of the
table bracket is engaged with the teeth of the rack and the arrow
stamped on the rack is pointing up.
●
Slide the table bracket with the rack onto the column.
●
Engage the bottom of the rack with the lip of the column
support. Tighten the table bracket lock handle to lock the table
bracket to the column.
●
Install the rack ring (Ref. No. 36) on the column so the top lip of
the rack sits into the rack ring.
IMPORTANT:
The bottom of the collar MUST NOT be pushed
all the way down onto the top of the rack. MAKE SURE the top
of the rack is under the bottom of the collar and that there is
enough clearance to allow the rack to freely rotate around the
column. Tighten the set screw of the rack ring.
NOTE:
To avoid column or collar damage, DO NOT OVERTIGHTEN
the set screw.
●
Install the table crank handle (Ref. No. 31) onto the worm gear
shaft on the side of the table bracket.
●
Line up the flat side of the worm gear shaft with the set screw
(Ref. No. 28) in the table crank handle (Ref. No. 31) and tighten the
screw with the 3 mm hex wrench provided.
●
Attach table (Ref. No. 24) to table bracket (Ref. No. 25) using the
table locking handle (Ref. No. 22).
ASSEMBLY