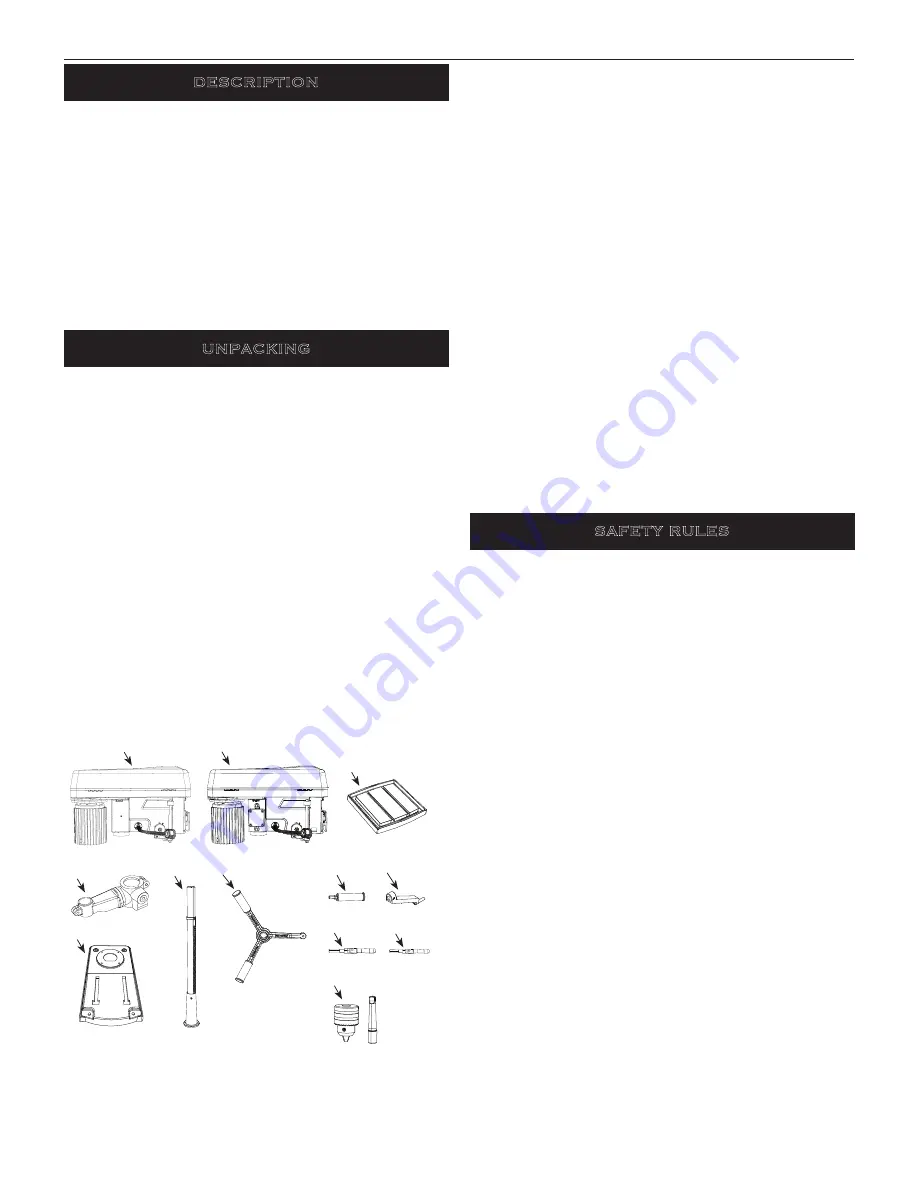
2
Palmgren Operating Manual & Parts List
80177
DESCRIPTION
Palmgren Drill Presses feature a heavy cast iron base, column collar,
work table and head. Work table height is adjustable using rack and
pinion. Table can be tilted 45° both right and left, and rotates 360°
on a vertical axis. Work table surface is precision ground and features
T-slots for secure, accurate mounting of workpiece and also a coolant
trough. Digital readout displays spindle RPM. Other features of the
Palmgren drill press are an enclosed ball bearing quill assembly,
quick belt change and tension mechanism, positive quick-adjust
feed depth stop and a 1 HP, 16 speeds motor. Chuck and chuck arbor
are included.
Palmgren drill presses are ideal for use in home shops, maintenance
shops and light industrial applications. Spindle speeds are adjustable
for drilling steel, cast iron, aluminum, wood and plastic.
UNPACKING
Refer to Figure 1.
WARNING:
Be careful not to touch overhead power lines, piping,
lighting, etc., if lifting equipment is used. Drill press weighs up to
183 lbs, proper tools, equipment and qualified personnel should be
employed in all phases of unpacking and installation.
Crates should be handled with care to avoid damage from dropping,
bumping, etc. Store and unpack crates with correct side up. After
uncrating drill press, inspect carefully for any damage that may have
occurred during transit. Check for loose, missing or damaged parts.
If any damage or loss has occurred, claim must be filed with carrier
immediately. Check for completeness. Immediately report missing
parts to dealer.
Drill press is shipped unassembled. Locate and identify the following
assemblies and loose parts:
A Head Assembly (~)
G Quill Feed Handle
B Head Assembly (3~)
H Feed Handle Bar
C Table
I
Table Crank Handle
D Table Bracket
J Table Bracket Locking Handle
E Base
K Table Locking Handle
F Column Assembly
L
Chuck & Spindle Arbor
IMPORTANT:
The tool has been coated with a protective coating.
In order to ensure proper fit and operation the coating must be
removed. Remove coating with mild solvents such as mineral spirits
and a soft cloth. Nonflammable solvents are recommended. After
cleaning, cover all exposed surfaces with a light coating of oil. Paste
wax is recommended for table top.
CAUTION:
Never use highly volatile solvents. Avoid getting
cleaning solution on paint as it may tend to deteriorate these
finishes. Use soap and water on painted components.
SPECIFICATIONS
Chuck size . . . . . . . . . . . . . . . . . . . . . . . . . . . . . . . . . . . . . . . . . . . . . .16 mm, JT3
Spindle taper . . . . . . . . . . . . . . . . . . . . . . . . . . . . . . . . . . . . . . . . . . . . MT2 x JT3
Spindle travel . . . . . . . . . . . . . . . . . . . . . . . . . . . . . . . . . . . . . . . . . . . . . . . . . . . 5”
Speeds . . . . . . . . . . . . . . . . . . . . . . . . . . . . . . . . . . . . . . . . . . . . . . . . . . . . . . . . . 16
RPM . . . . . . . . . . . . . . . . . . . . . . . . . . . . . . . . . . . . . . . . . . . . . . . . . . . . 138 - 3476
Table size . . . . . . . . . . . . . . . . . . . . . . . . . . . . . . . . . . . . . . . . . . 14-1/3 x 14-1/3”
Base size . . . . . . . . . . . . . . . . . . . . . . . . . . . . . . . . . . . . . . . . . . . 20-2/5 x 11-1/9”
Overall height . . . . . . . . . . . . . . . . . . . . . . . . . . . . . . . . . . . . . . . . . . . . . . . . . . 68”
Weight . . . . . . . . . . . . . . . . . . . . . . . . . . . . . . . . . . . . . . . . . . . . . . . . . . . . . 183 lbs
Motor:
Single phase . . . . . . . . . . . . . . . . . . . . . . 1 HP, 120/240 V, 10.2/5.1 A, 60 Hz
(Tool Prewired 120 V)
Three phase . . . . . . . . . . . . . . . . . . . . . . . . . . . . . . . . . . 1 HP, 240 V, 5 A, 60 Hz
PROPOSITION 65 WARNING:
Some dust created by power
sanding, sawing, grinding, drilling and other construction activities
contains chemicals known to the state of California to cause cancer,
birth defects or other reproductive harm.
Some examples of these chemicals are:
●
Lead from lead-based paints.
●
Crystalline silica from bricks and cement and other
masonry products.
●
Arsenic and chromium from chemically-treated lumber.
Your risk from these exposures vary, depending on how often you do
this type of work. To reduce your exposure to these chemicals: work
in a well ventilated area and work with approved safety equipment.
Always wear
OSHA/NIOSH
approved, properly fitting face mask or
respirator when using such tools.
Before any work is done, carefully read the cautions listed. Working
safely prevents accidents.
BE PREPARED FOR JOB
●
Wear proper apparel. Do not wear loose clothing, gloves, neckties,
rings, bracelets or other jewelry which may get caught in moving
parts of machine.
●
Wear protective hair covering to contain long hair.
●
Wear safety shoes with non-slip soles.
●
Wear safety glasses which comply with United States ANSI Z87.1.
Everyday glasses have only impact resistant lenses. They are NOT
safety glasses.
●
Wear face mask or dust mask if cutting operation is dusty.
●
Be alert and think clearly. Never operate power tools when tired,
intoxicated or when taking medications that cause drowsiness.
SAFETY RULES
A
B
C
D
E
F
Figure 1 - Unpacking
G
H
I
J
K
L
Not Shown: Worm Gear, four M10*1.5-40 Hex Bolts, Wedge,
3 and 5 mm Hex Wrenches, Chuck Key, Belt Tesion Handle,
Hardware Bag For Quill Feed Handle.