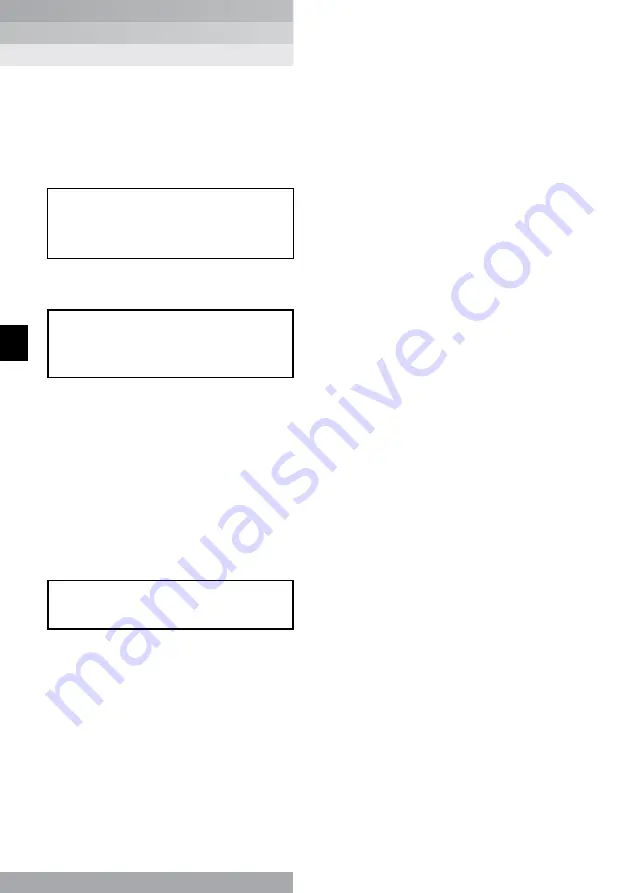
4
8
Fluid Sampling
Optimum sampling to verify fluid condition can be achieved
by the use of sampling adaptors installed in place of or in
combination with the differential pressure device. For more
information consult Pall or your local Pall Distributor.
Pall offers a fluid contamination analysis service – consult the
Pall sales office.
9
Warranty, Limitation of Liability and
Remedies
THERE IS NO WARRANTY OF MERCHANTABILITY OR
FITNESS FOR ANY PARTICULAR PURPOSE WITH RESPECT
TO ANY OF THE PRODUCTS, NOR IS THERE ANY OTHER
WARRANTY EXPRESS OR IMPLIED, EXCEPT AS PROVIDED
FOR HEREIN.
For a period of twelve months from the date of delivery from
Seller or three thousand hours of use, whichever occurs
first (the “Warranty Period”), Seller warrants that products
manufactured by Seller when properly installed and
maintained, and operated at ratings, specifications and
design conditions, will be free from defects in material and
workmanship. By way of explanation and not limitation, the
Seller does not warrant the service life of the filter element as
this is beyond the Seller’s control and depends upon the
condition of the system into which the filter is installed.
Seller’s liability under any warranty is limited solely (in Seller’s
discretion) to replacing (FOB original ship point), repairing
or issuing credit for products that become defective during
the Warranty Period. Purchaser shall notify Seller promptly in
writing of any claims and provide Seller with an opportunity
to inspect and test the product claimed to be defective.
Buyer shall provide Seller with a copy of the original invoice
for the product, and prepay all freight charges to return any
products to Seller’s factory, or other facility designated by
Seller. All claims must be accompanied by full particulars,
including system operating conditions, if applicable.
Seller shall not be liable for any product altered outside of
the Seller’s factory except by Seller or Seller’s authorized
distributor, and then, as to the latter, only for products which
have been assembled by the distributor in accordance with
Seller’s written instructions. Nor shall Seller be liable for a
product subjected to misuse, abuse, improper installation,
application, operation, maintenance or repair, alteration,
accident or negligence in use, storage transportation or
handling. In no event will Seller be liable for any damages,
incidental, consequential or otherwise, whether arising out of
or in connection with the manufacture, packaging, delivery,
storage, use, misuse, or non use of any of its products or any
other cause whatsoever.
7
Filter element installation / servicing
During servicing the external surfaces of the filter assembly
must be cleaned to remove any dust deposits.
Servicing must be conducted using suitable tools that do not
present a hazard. Servicing must also not be carried out when
a potentially explosive atmosphere is present.
Refer to Product Datasheet (TRG410TEN) for item numbers for
applicable replacement element series. Remove and replace
element as follows:
7.1 Turn off and depressurize the system.
7.2 Unscrew and remove the filter bowl assembly (2) from
head (1) counter-clockwise when viewed from below.
7.3 Filter element replacement (G300 Series): Remove filter
element (5), if already fitted by turning clockwise by
¼ turn and pulling down, and carefully inspect the
interior surface (flow through the element is out-to-in) for
visible contamination. Normally no dirt should show, but
visible dirt or particles can be an early warning of system
component failure. Discard both the filter element
and its O-ring. The filter element is NOT CLEANABLE.
Any attempt to clean the filter element can cause
degradation of the filter medium and allow
contaminated fluid to pass through the filter element.
7.4 To replace the filter element, Lubricate element O-ring
with clean system fluid, align arrows on filter element
end cap to arrows on the filter head. Push up and rotate
anti-clockwise through ¼ turn to a stop.
Use the replacement filter element as indicated by
the part number on the filter element end cap.
7.5 DO NOT run the system without a filter element installed.
Check that the O-ring between the bowl (2) and head (1)
is not damaged. Replace if damaged. It is recommended
that the o-ring head-to-bowl seal is changed at each
element service.
7.6 Lightly lubricate head-to-bowl O-ring with clean system
fluid and reassemble the housing until thread bottoms.
The bowl should be torque tightened to 74 ft/lb or 100 Nm.
O-ring sealing is not improved by over tightening
7.7 Bleed the system and check for leaks as per section 4.8.
7.8 After element change ENSURE DIFFERENTIAL
PRESSURE DEVICE IS RESET; both visual and electrical
switches reset automatically. When system reaches
normal operating conditions, check that the electrical
switch has not actuated and/or the visual warning button
has returned to white.
WARNING:
FAILURE TO DEPRESSURISE THE FILTER BEFORE
SERVICING ELEMENT COULD RESULT IN EXPLOSIVE
LOSS OF FLUID, DAMAGE TO EQUIPMENT AND
POSSIBLE PERSONAL INJURY.
WARNING:
DO NOT ATTEMPT TO CLEAN OR RE-USE THE
ELEMENT.
CAUTION:
Filter elements should be replaced upon indication
or at specified intervals, six months maximum is
recommended. Failure to change the element will cause
the filter to go on bypass.
G410
V E r S a l o N H I G H P r E S S U r E F I l T E r S
EN
G410 Series
s e r v i c e
i n s t r u c t i o n s