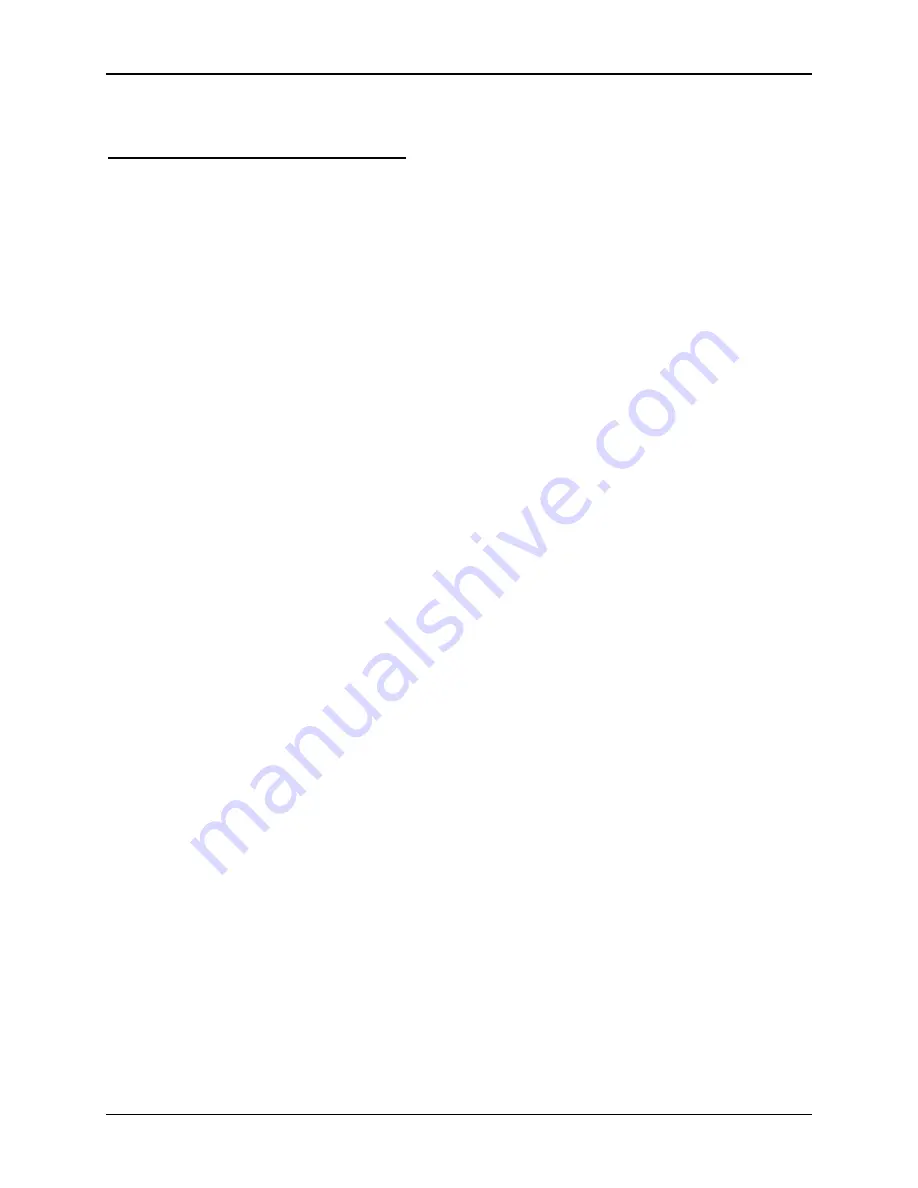
Instruction and Service Manual
Field Troubleshooting
Pacific Scientific REDI-LINE Generators
25
7. FIELD TROUBLESHOOTING
Field Service
Pacific Scientific recommends that field troubleshooting be performed whenever a
problem is encountered with the REDI-LINE generator, to correct or eliminate
problems caused by faulty installation or load changes, and thereby avoid
unnecessary returns.
The following pages contain troubleshooting procedures that should be followed if
there is a problem in the field. The procedures are oriented toward the installation
itself, and are intended to assist in correcting any problems that are a result of an
installation problem. If the problem cannot be resolved using these procedures, the
Redi-Line generator should be returned to the distributor for additional testing and
possible repair.
Most field problems can be traced to installation problems; following these
procedures closely can eliminate unnecessary returns and keep the Redi-Line
generator in service.
For your convenience we have included a Field Troubleshooting Checklist Form
which you should copy and fill out as you perform field troubleshooting. If you
should find it necessary to return the unit for repair, include the form with the
generator. This will reduce the bench time required by your dealer to diagnose a
problem, and thereby reduce your repair costs.
Use of Flow Charts
Locate your specific symptom or symptoms in the troubleshooting flow chart in
Figure 7-1. Each symptom will advise you to return the unit for repair, or refer you to
an additional flow chart, which will provide a series of inspections, checks, or
actions which will either enable you to return the unit to service, or advise you to
return the unit for repair.
Field inspection and checkout often consists of a review of installation procedures,
materials, and techniques. The areas to be reviewed are specifically identified by
the flow chart. Specific checkout procedures not associated with installation are
found in the subsection titled “Troubleshooting Checkout Procedures” following the
troubleshooting flow charts
Conditional Branches
Where there are conditional branches (diamonds labeled either “Okay” or “Or”),
follow the most appropriate path. The conditions for the “Okay” diamonds, shown
adjacent to the arrows leaving the diamond, refer to the inspection procedure
immediately preceding the diamond, that is, if the arrow is labeled “yes”, the
condition inspected was found to be satisfactory.
Additional Troubleshooting and Repair
Section 8, Bench Troubleshooting, provides bench troubleshooting procedures, for
use by repair personnel at the distributor’s facility or at the factory. If you have the