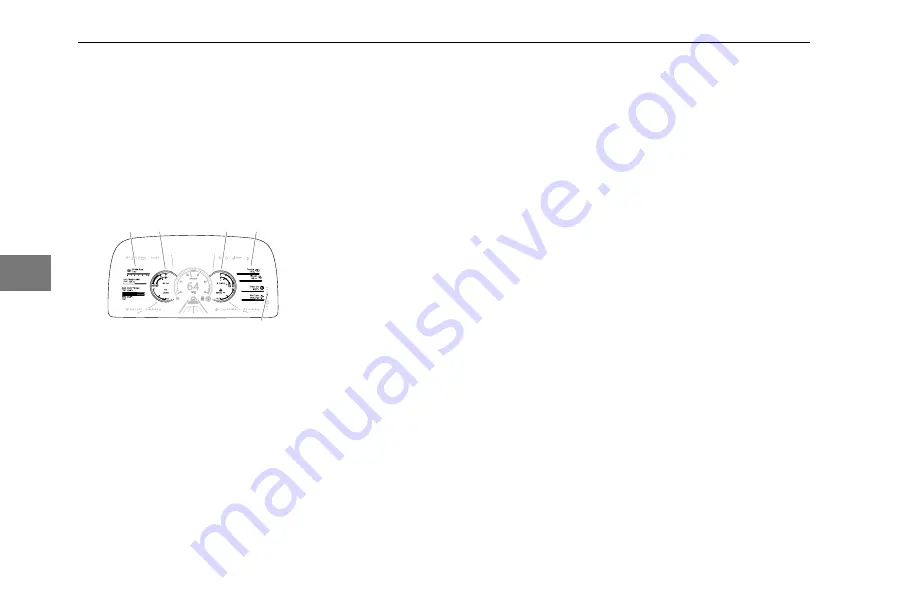
•
Periodically, to ensure system
integrity
To check for Air System leaks
1.
Start the engine if not already
running.
2.
Scroll
to either the Basic or
Enhanced View to monitor Primary
and Secondary Air Pressures: see
(1) of Enhanced View.
2
2
1
3
1
3.
Build up air pressure in the system
until the system cutout setpoint or
until 120 psi (827 kPa) is reached.
4.
Turn the Ignition Switch to OFF
(stopping the engine) and then
back to the ON position, but don't
start the engine.
The Basic or Enhanced View will
appear.
5.
Release the service brakes, and
observe the rate of air pressure
drop. This rate should not exceed
2.0 psi (14 kPa) per minute.
6.
Start the engine and build up air
pressure again.
7.
Turn the Ignition Switch to OFF
(stopping the engine) and then
back to the ON position, but don't
start the engine.
8.
Apply the brakes fully, holding the
pedal down for five minutes. The
pressure drop should not exceed
3.0 psi (21 kPa) per minute.
9.
If you detect excessive leakage (air
pressure loss greater than 3.0 psi
(21 kPa) after five minutes of brake
application), a leakage test should
be made at the air line connections
and at all air brake control units.
These tests should determine
where air is escaping.
Air Compressor
All compressors, regardless of make or
model, run continuously while the engine is
running. System pressure is controlled by
the governor. The governor acts in
conjunction with the unloading mechanism
in the compressor cylinder block to start
and stop compression of air. The
compressor is unloaded when the system
pressure reaches 120 psi (827 kPa) and
compression is reestablished when system
pressure falls to 100 psi (690 kPa).
Preventive Maintenance
The following service checks are provided
for your information only and should be
performed by a certified mechanic. Contact
your dealer or the engine manufacturer's
Maintenance Manual for further information
on servicing air compressors. After
completing any repairs to the air system,
always test for air leaks, and check the
brakes for safe operation before putting the
vehicle in service. Below is a list of areas
to maintain for the air compressor:
•
Inspect compressor air filter
element, if so equipped, and
replace element if clogged. Check
compressor mounting and drive for
alignment and belt tension. Adjust
if necessary.
•
Remove compressor discharge
valve cap nuts and check for
presence of excessive carbon. If
excessive carbon is found, clean or
replace the compressor cylinder
head. Also, check compressor
discharge line for carbon, and
clean or replace the discharge line
if necessary.
MAINTENANCE - Air Compressor
238
Y53-6126-1A1 (01/21)
5
Содержание Peterbilt 567 2021
Страница 1: ...567 M O D E L ...
Страница 2: ......
Страница 3: ...Safety 1 Emergency 2 Controls 3 Driving 4 Maintenance 5 Information 6 Contents ...
Страница 5: ......
Страница 7: ...Daily Checks 35 Weekly Checks 36 Systems Check 37 SAFETY Y53 6126 1A1 01 21 5 1 ...
Страница 41: ...SAFETY Systems Check Y53 6126 1A1 01 21 39 1 ...
Страница 63: ...1 Additional Switches 2 Ignition Switch CONTROLS Instrument Cluster Y53 6126 1A1 01 21 61 3 ...
Страница 131: ...CONTROLS Cab Accessories Y53 6126 1A1 01 21 129 3 ...
Страница 331: ......