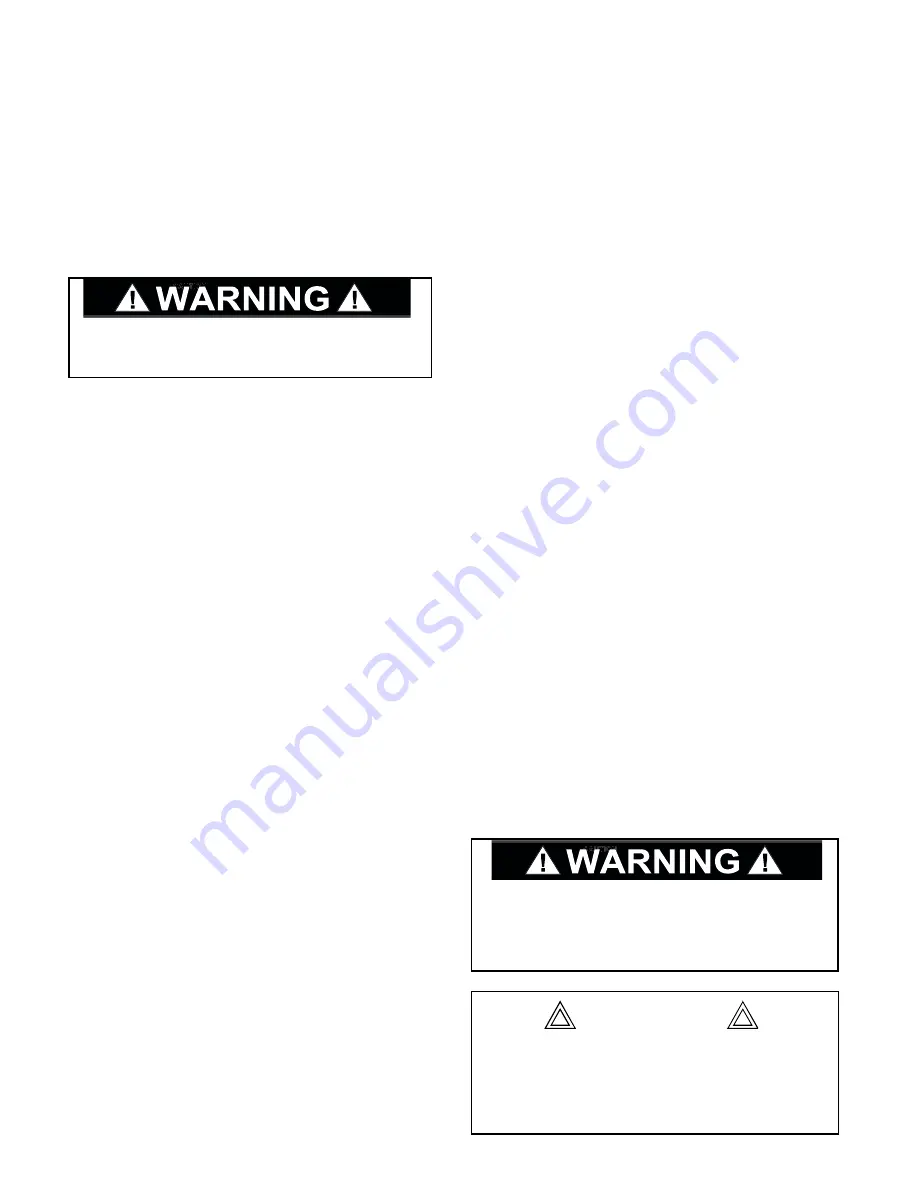
3
GENERAL SAFETY
RECOMMENDATIONS
Safety for operators and ground personnel is of prime con-
cern. Always take the necessary precautions to ensure
safety to others as well as yourself. To ensure safety, the
prime mover and winch must be operated with care and
concern by the operator for the equipment, and a thorough
knowledge of the machine's performance capabilities. The
following recommendations are offered as a general safety
guide. Local rules and regulations will also apply.
1. Read all warning tag information and become familiar
with all controls
BEFORE
operating winch.
2.
NEVER
attempt to clean, oil or perform any mainte-
nance on a machine with the engine running, unless
instructed to do so in the service manual.
3.
NEVER
operate winch controls unless you are proper-
ly seated at the operators station on the prime mover
and you are sure personnel are clear of the work area.
4. Assure that personnel who are responsible for hand
signals are clearly visible and that the signals to be
used are thoroughly understood by everyone.
5. Ground personnel should stay in view of the prime
mover operator and clear of winch drum.
DO NOT
allow ground personnel near winch line under tension.
A safe distance of at least 1½ times the length of the
cable should be maintained.
NEVER
allow anyone to
stand beneath a suspended load
6. On machines having hydraulically, mechanically and/or
cable controlled equipment, be certain the equipment is
either lowered to the ground or blocked securely before
servicing, adjusting and/or repairing the winch. Always
apply the prime mover parking brakes and lower equip-
ment before dismounting the prime mover.
7. Inspect rigging, winch and hydraulic hoses at the
beginning of each work shift. Defects should be cor-
rected immediately.
8. Keep equipment in good operating condition. Perform
scheduled servicing and adjustments listed in the
"Preventive Maintenance" section of this manual.
9. An equipment warm-up procedure is recommended for
all start-ups and is essential at ambient temperatures
below +40ºF. Refer to "Warm-up Procedure" listed in
the "Preventive Maintenance" section of this manual.
10. Be sure of equipment stability before operating winch.
11. The winches described herein are neither designed nor
intended for use or application to equipment used in
the lifting or moving of persons.
12.
DO NOT
exceed the maximum pressure (PSI) or flow
(GPM) stated in the winch specifications.
13. Operate winch line speeds to match job conditions.
14. Leather gloves should be used when handling winch
cable.
15.
NEVER
attempt to handle winch cable when the hook
end is not free.
16. When winding winch cable on the winch drum,
NEVER
attempt to maintain tension by allowing winch cable to
slip through hands. Always use "hand-over-hand"
technique.
17
NEVER
use winch cable with broken strands. Replace
winch cable.
18.
DO NOT
weld on any part of the winch.
19.
DO NOT
use knots to secure or attach winch cable.
20. Use recommended hydraulic oil and gear lubricant.
21. Keep hydraulic system clean and free from contamina-
tion at all times.
22. Use correct size cable anchor for cable and pocket in
winch drum.
23. The BRADEN wire rope anchors are capable of sup-
porting the rated load only when installed properly. For
additional safety,
ALWAYS
maintain a minimum of five
(5) wraps of wire rope on the drum.
Safety informational callout's used in this manual include:
FAILURE TO OBEY THE FOLLOWING SAFETY
RECOMMENDATIONS MAY RESULT IN PROPER-
TY DAMAGE, PERSONAL INJURY OR DEATH.
This emblem is used to warn against hazards and
unsafe practices which COULD result in severe per-
sonal injury or death if proper procedures are not fol-
lowed.
This emblem is used to warn against potential or
unsafe practices which COULD result in personal
injury or product or property damage if proper proce-
dures are not followed.
CAUTION
SHOP ONLINE at www.airlinehyd.com
800-999-7378