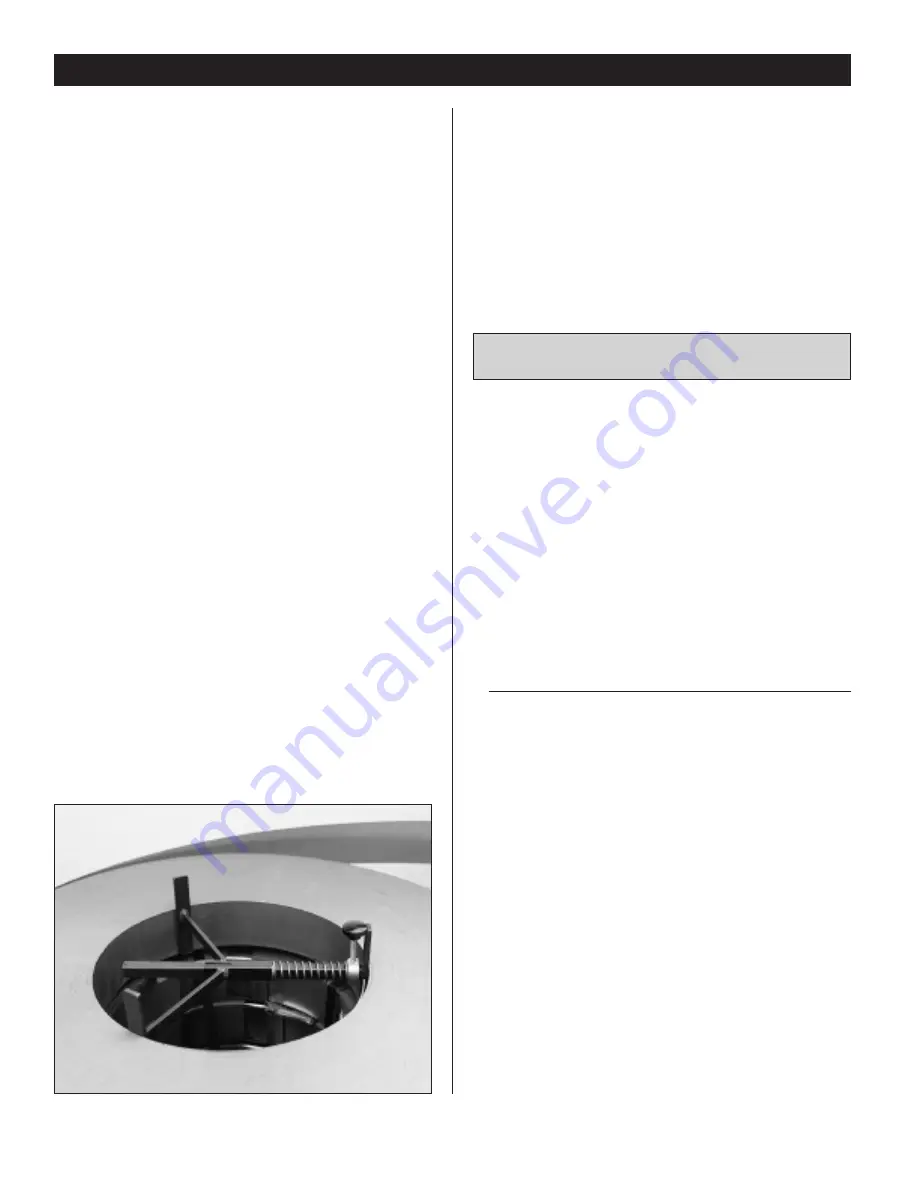
8
PALLETIZER
WARNING - DO NOT PERFORM ANY MAINTENANCE FUNCTIONS
WITHOUT FIRST DISCONNECTING POWER.
Figure 8
Counter-Weight Tension System
Begin operation with two weights on each cable. Pull cable
upwards through top of Weight Channel. Weights are easily
added or removed by positioning the Cable Toggle to slip
weights on or off.
Extra weights are stored on the Base Arm.
The weight on the cables should be sufficient to draw the
Guide Drum back to the off position when material demand
stops. Weight/tension should not be so great as to cause
undue stress on the stock or erratic motion of the Guide
Drum.
There is no formula or specific rule regarding how much
tension weight is needed. The goal is to balance the
weight of the strip loop with the back tension created by
the weights. Variables of strip width, thickness, loop
weight, feed length and press speed in a wide range of
combinations preclude a specific guiding rule.
Proper weight/tension balance is a matter of beginning with
two weights on each cable, running the forming equipment,
observing results at guide drum, and then adjusting
weights.
Optional Coil-lock (Figure 8)
The Coil-Lock will prevent the top coil from shifting off
center or pulling off the coil stack as its weight diminishes
toward the inside diameter of the coil. The Coil-Lock fits
inside the open space at the core of the coil stack.
Trial fit the Coil-Lock.
Adjust the length and tension of the Coil-Lock by
positioning the Stop Collar at the appropriate location. The
Stop Collar is secured with the black knob. Set the Stop
Collar in a position that results in a Coil-Lock length slightly
longer than the I.D. dimension.
The Coil-Lock is compressed and placed in the open I.D.
space, then released to snugly press outward against the
coil.
The vertical legs of the Coil-Lock should connect with the
top coil and however many of the lower coils as strip width
will allow.
MAINTENANCE
Proper care and maintenance of the Pallet Reel will ensure
efficient operation and will extend service life of the
machine.
We recommend that upon receipt of your Pallet Reel,
arrangements be made to have your Pallet Reel added to
the plant maintenance schedule to ensure regular and con-
sistent maintenance attention.
Cleaning
Periodically wipe clean the surface areas of the Pallet Reel
including the tabletop, Control Box and Guide Drum.
Frequency of cleaning will be dictated by shop conditions
of dirt, dust, oil, etc.
Lubrication
•
Edge Guide Roller - At 30-day intervals apply a thin
coat of light machine oil.
•
Reduction Gear- Manufacturer’s product information
contains detail on this maintenance procedure. The
following summarizes lubrication change schedules.
Petroleum
Synthetic
Lubricant
Lubricant
Initial Change:
250 hours
1500 hours
Regular Change:
2500 hours
5000 hours
or six months
•
Linear Shaft – At thirty-day intervals wipe polished rod
and spray with DTE Light Oil or other light machine oil.
Electric Motor
Manufacturer’s product information contains detail on care
of the motor.
TROUBLE SHOOTING
Table Does Not Rotate or Tight Loop
•
Check Supply Power and Line Voltage.
•
Check Circuit Breaker inside the motor control.
•
Check if Reset Light on Control is illuminated. Reset by
either pushing Reset Button and/or pressing Linear Shaft
towards Motor Control (Figure 9).