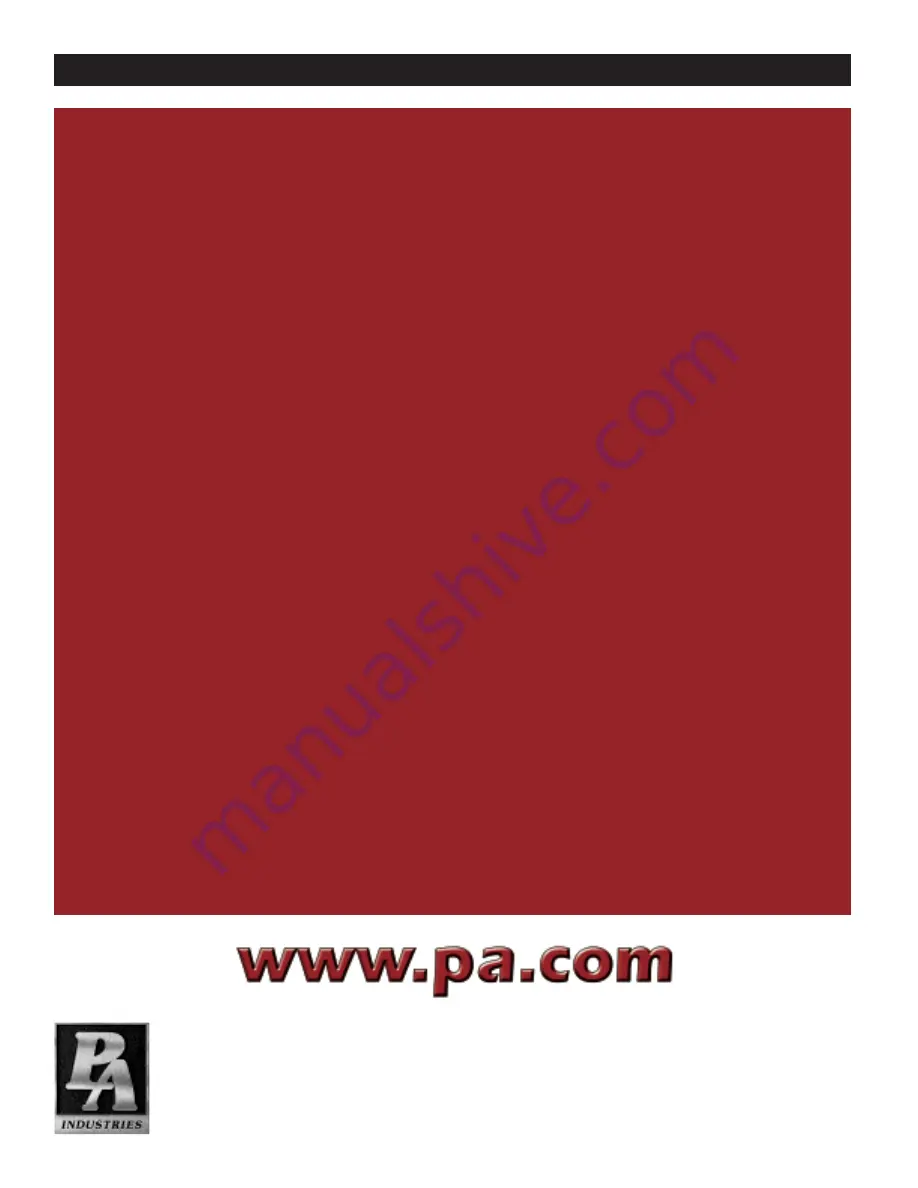
®
P/A INDUSTRIES INC.
P/A Technology Park
Toll Free: 1-800-243-8306
522 Cottage Grove Rd.
Worldwide: 1-860-243-8306
Bloomfield, Connecticut
Fax: 1-860-242-4870
06002-3191 USA
E-Mail: [email protected]
FORM 1114 3-08
Warning
This equipment offers various means of operating or controlling
machines. The operator must not be in or near the point-of-
operation of the machine, or the operating parts of any
equipment installed on the machine, or bodily injury could result.
The EMPLOYER must post adequate warning signs onto the
machine with proper warnings for his machine and the specific
application to which the machine and equipment are being
applied.
Occupational Safety and Health Act (OSHA) Sections 1910.211,
1910.212, and 1910.217 contain installation information on the
distance between danger points and point-of-operation guards
and devices. No specific references have been made to which
paragraph of OSHA 1910.211, 1910.212, 1910.217 or any other
applicable sections because the paragraphs may change with
each edition of the publication of OSHA provisions.
All equipment manufactured by us is designed to meet the
construction standards of OSHA in effect at the time of sale,
but the EMPLOYER installs the equipment so the EMPLOYER
is responsible for installation, use, application, training, and
maintenance, as well as adequate signs on the machine onto
which this equipment will be installed.
Remember, OSHA says that the EMPLOYER must use
operating methods designed to control or eliminate hazards to
operating personnel.
It shall be the responsibility of the EMPLOYER to establish and
follow a program of periodic and regular inspections of his
machine to insure that all their parts, auxiliary equipment, and
safeguards are in a safe operating condition and adjustment.
Each machine should be inspected and tested no less than
weekly to determine the condition of the machine. Necessary
maintenance or repair of both shall be performed and completed
before the machine is operated. The EMPLOYER shall maintain
records of these inspections and the maintenance work
performed.
Our Company is not responsible to notify the user of this
equipment of future changes in State or Federal laws, or
construction standards.
Safety Program
Accident free operation will result from a well developed,
management sponsored and enforced safety program.
Of vital importance to any successful program is the proper
selection of guards and devices. However, there is no safety
device that will bring “automatic” safety to your operation.
Of equal importance to this proper selection of the guard and the
device is the training of your personnel. Each person must be
trained as to the operation of the guard or safety device,
highlighting why they have been provided on the equipment.
Rules for safe operating should be written and enforced at all
times. A final major concern of an effective safety program is
regularly scheduled inspection and maintenance of all of the
equipment.
To ensure continued safety at all times, top management, line
supervision, safety engineers and all employees must assume
their proper share of the responsibility in the program. Only as a
group, one that knows your own operation and its problems, can
you carry out an effective safety program.
To assist you in the development of and continued use of safety
programs, many safety minded groups have made guidelines
available to you. However, you must know when and how to
apply these guidelines. The manufacturer provides information
to assist you in properly adjusting and maintaining your
equipment. There is no short cut to proper safety; therefore, it
is recommended that you comply with their recommendations at
all times.
Warranty
We warrant our new parts against defects under normal use and
service for a period of 12 months after date of shipment. Our
obligation under this warranty is limited to replacing or repairing
(at our option) the defective part without charge, F.O.B. our plant
in Bloomfield, Connecticut. The defective part must be forward-
ed or repair. EXCEPT AS EXPRESSLY PROVIDED HEREIN,
THIS WARRANTY IS IN LIEU OF ALL OTHER WARRANTIES,
EXPRESS OR IMPLIED, INCLUDING A WARRANTY OF
MERCHANTABILITY OR FITNESS FOR A PARTICULAR
PURPOSE. Furthermore, the seller does not warrant or
represent that the equipment complies with the provisions of any
law, particularly including the Occupational Safety and Health Act
of 1970, and regulations promulgated thereunder. In no event
shall we be liable for special, indirect incidental or consequential
damages, however rising.
WARRANTY AND SAFETY PROGRAM