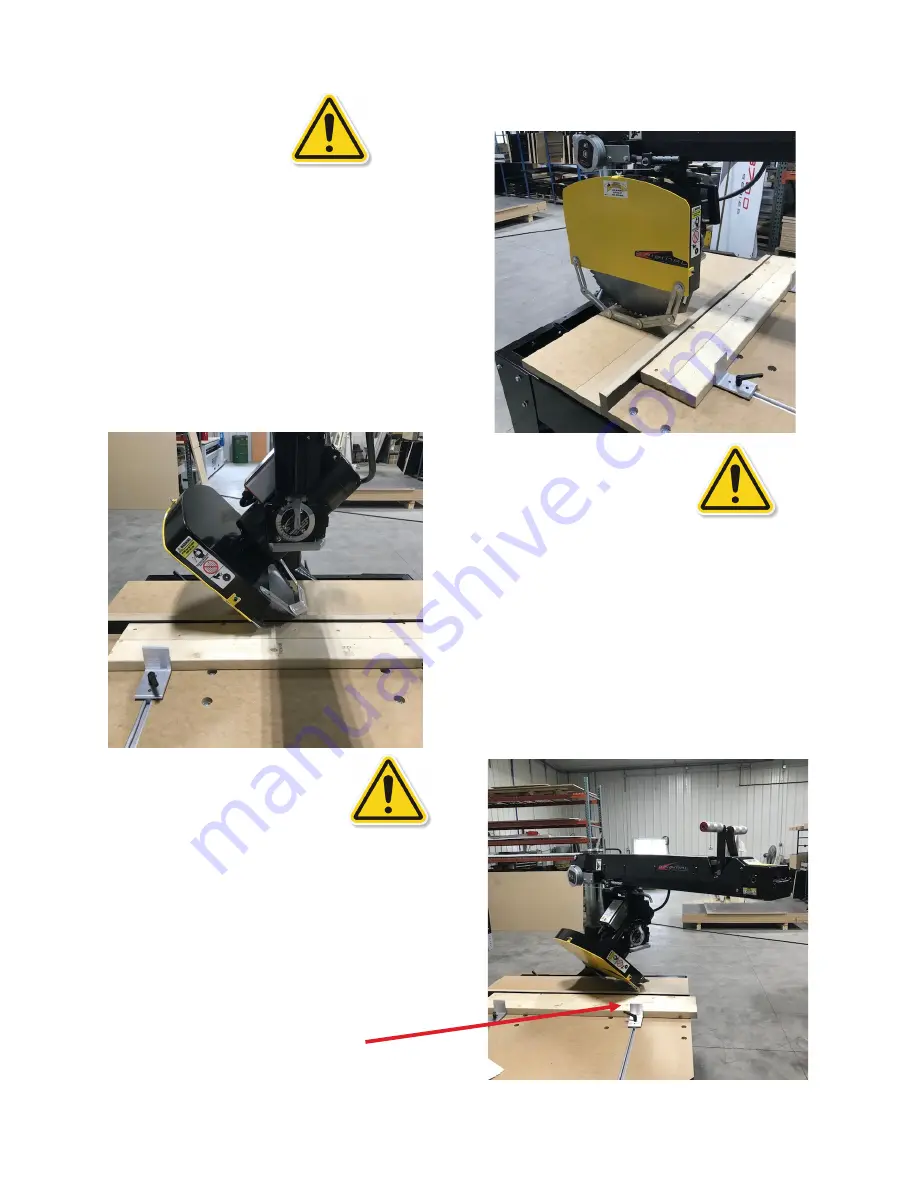
22
Bevel Cutting
Lock the arm in the cross cutting position. Raise
the motor by rotating the elevation crank. Re-
lease the bevel clamp and the bevel latch and
tilt the motor in the yoke. The bevel angle is
shown on the bevel scale. Lock the bevel latch
and clamp. Lower the arm into cutting position.
Adjust the bevel stop to assure clearance be-
tween blade and base. Pull the saw through as
you would for cross cutting. Make sure rear of
blade as clearance between it and base. (Page
28)
Compound Miter Cutting
The compound miter is merely a combination of
the bevel cut and the miter cut. Set up the ma-
chine for bevel cutting. Release the arm clamp
handle and the miter latch handle. Swing the
arm into the required position and lock the miter
latch and arm clamp. Adjust bevel stop to assure
clearance between blade and base. Pull the
blade through as you would for cross cutting.
Note: pay attention to blade to clamp clearance
See Clamps section to allow for clamp clearance
on miter cuts. (Page 22)
Cross Cutting
Lock the arm in the 0
o
position. Place the ma-
terial securely against the guide strip
–
keep
hands well away from the blade. Draw the saw
blade across the material. After the cut has
been completed return the blade behind the
guide strip. Observe this order of operation for
all cross cuts. Never push the saw blade into
the material. Pull the blade slowly and firmly
across the material from the rear of the arm
using the operating handle. The saw blade
should cut into the table about 1/ 16” when
cutting through the material. Raise the anti-
kickback (when installed) to just clear the ma-
terial being cut. Adjust for varying wood thick-
ness or warped material.
Operating
Instructions
Содержание 3553
Страница 34: ...34 Intentionally left blank ...