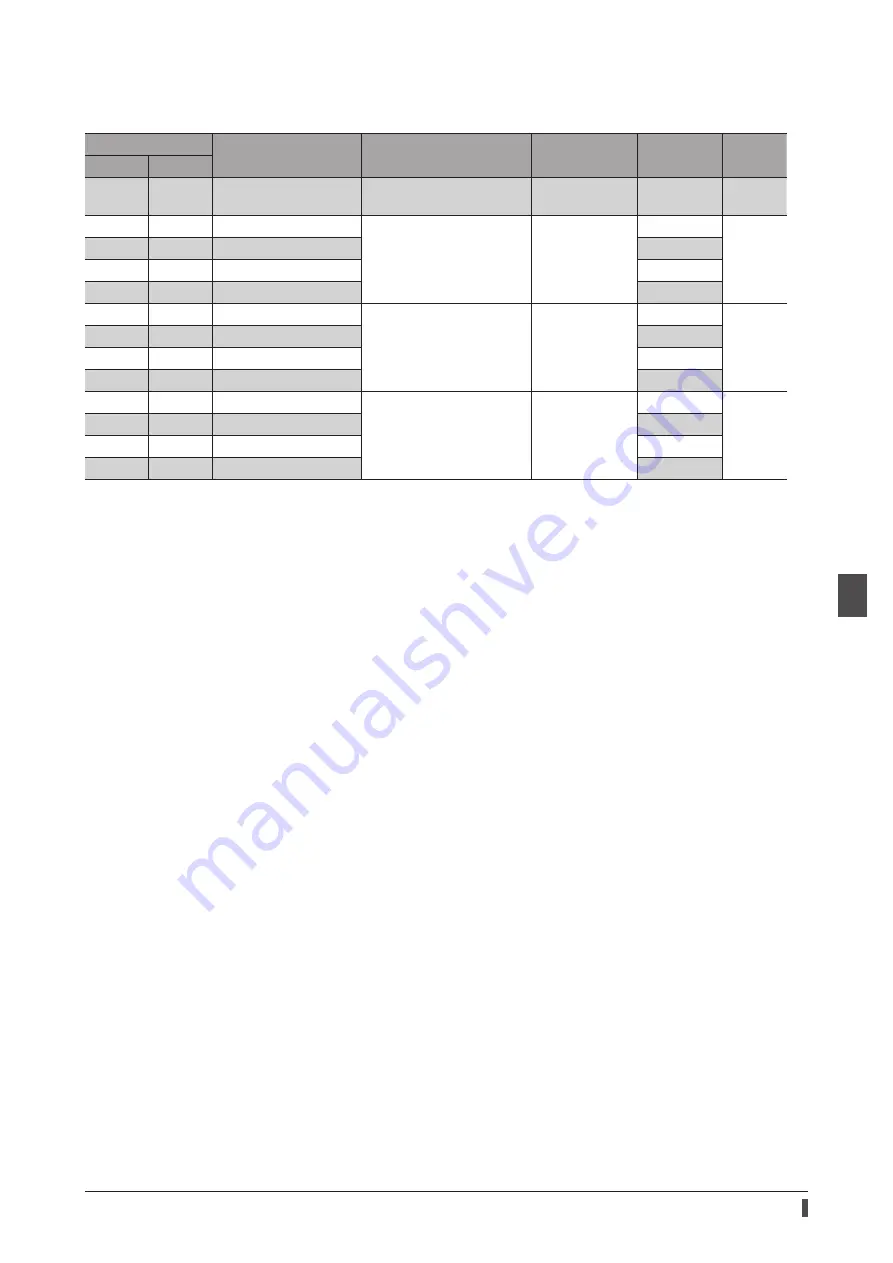
Parameter R/W commands
4 P
ar
93
z
IP address setting parameters
These are set using the
MEXE02
software. They cannot be read or written via Implicit communication.
Parameter ID
Name
Description
Setting range
Initial value
Update
Dec
Hex
−
−
Configuration Control
Sets how to obtain the IP
address.
0: Parameter
2: DHCP server
2
D
−
−
IP Address 1
Sets the IP address.
0 to 255
192
D
−
−
IP Address 2
168
−
−
IP Address 3
1
−
−
IP Address 4
1
−
−
Network Mask 1
Sets the subnet mask.
0 to 255
255
D
−
−
Network Mask 2
255
−
−
Network Mask 3
255
−
−
Network Mask 4
0
−
−
Gateway Address 1
Sets the default gateway.
0 to 255
0
D
−
−
Gateway Address 2
0
−
−
Gateway Address 3
0
−
−
Gateway Address 4
0
Содержание A Step AZ Series
Страница 14: ...1 Introduction 14 ...
Страница 64: ...3 Implicit communication 64 ...