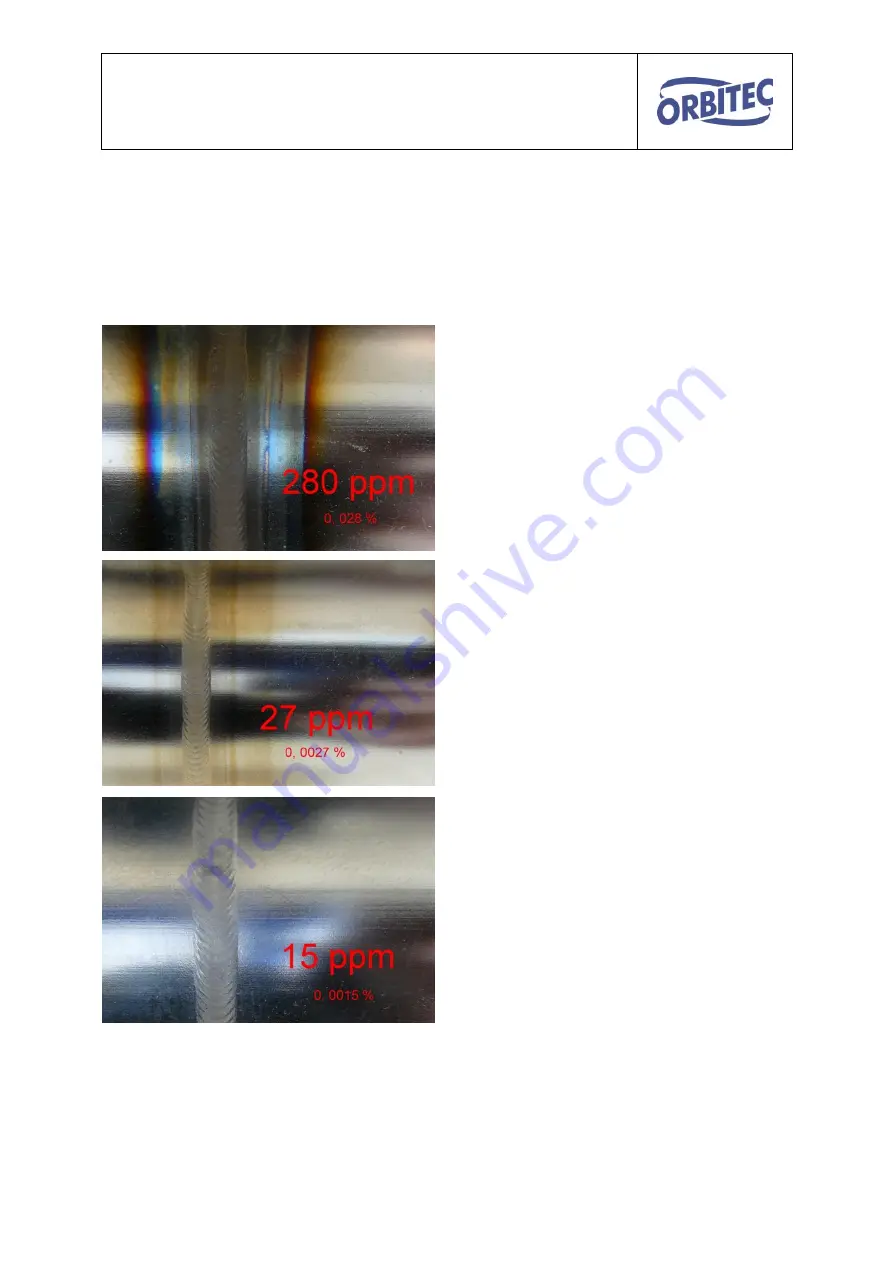
Instruction Manual OXY-
SMART
3
1.
Preface
Correct formatting is imperatively required for quality assurance when welding
high-alloy, corrosion-resistant components.
Only at very low residual oxygen content during the welding process
it is possible to attain neat and corrosion-resistant welding seams with little colouring
on the inner surface of the tube.
An insufficient gas protection results in
annealing colouring or carburization in the
heat affected zone as well as a reduction
of the corrosion resistance of the welding
seam and thus it is unsuitable for any tube
installation.
To monitor the quality of the flushing gas
before the welding process, it is necessary
to use measuring devices to check the
residual oxygen content.
The welder or the operator can use the
measuring device Oxy-
SMART
to check
and document the residual oxygen
content. The ppm value to be entered in
the display can be freely selected. If not
otherwise imperatively prescribed, a value
of < 30 ppm is generally sufficient at the
beginning of the welding process. If the
measured value falls below the entered
value, the colour on the display changes
from red to green.
It is possible to start the welding process.
The mobile measuring device Oxy-
SMART
serves to record the residual oxygen
content in flushing, welding and forming
gases in the welding technique.
Residual oxygen concentration can be
measured and determined in the following
gas mixtures: Inert gases and forming
gases. Inert gases are among others
nitrogen, argon, helium and other rare
gases. Forming gases are gas mixtures consisting of nitrogen or argon and
hydrogen. There are different gas mixtures with different H2 fractions, the maximum
fraction of hydrogen must not exceed 10 %.
The measuring device is not suitable to perform measurements of explosive gas
mixtures, in particular it is not suitable to measure pure hydrogen. There is a risk of
explosion!