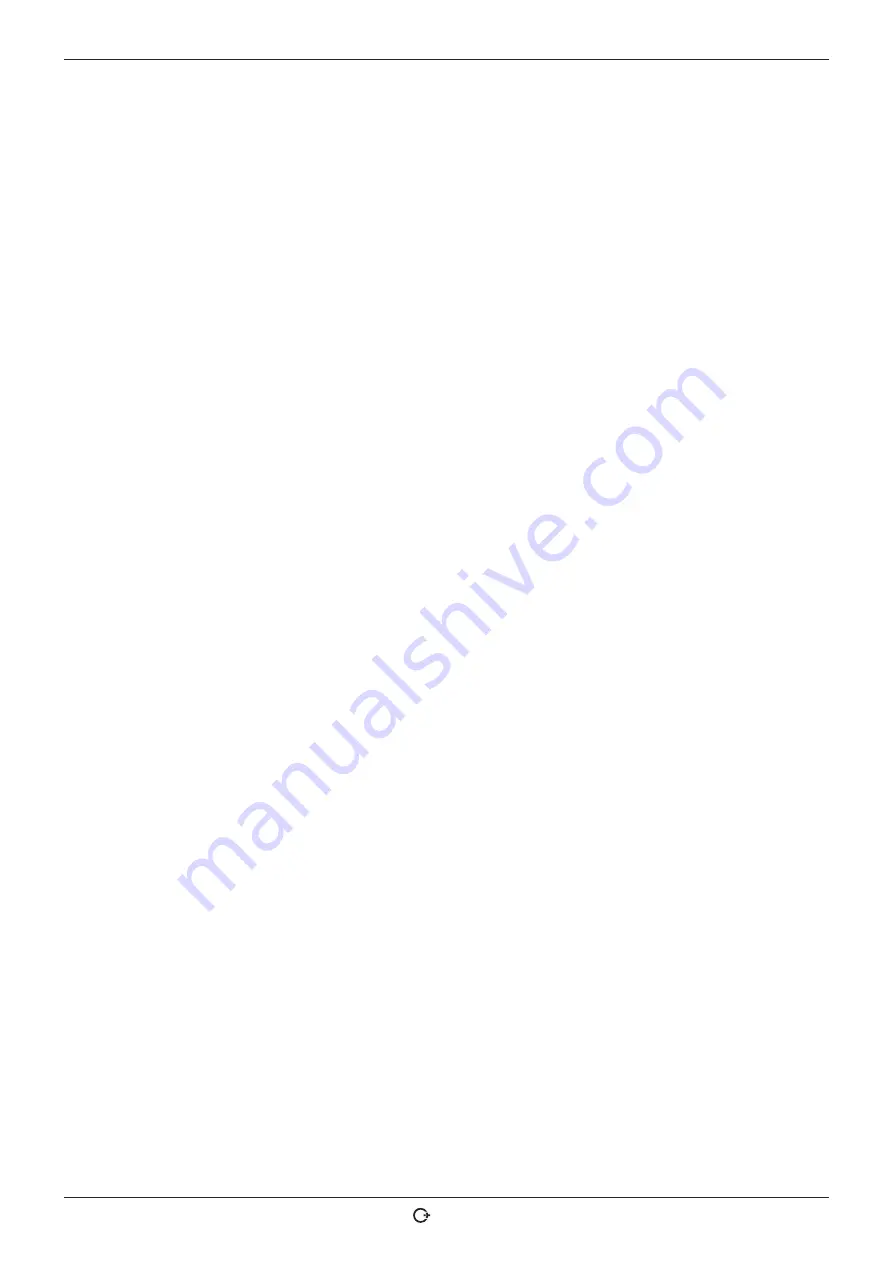
(12.03.18) OW_P16_P20_BA_831060202_03_EN
orbitalum tools
GmbH, D-78224 Singen, www.orbitalum.com, Tel. +49 (0) 77 31 792-0
15
P16, P16 AVC, P20
| Operating instructions
Use and maintenance
5. USE AND MAINTENANCE
5.1
Use of weld head
The high technology achieved with weld head puts this model as response on top of the international market demands.
This welding head is extremely simple and allows easily to perform all necessary adjustments for a proper welding,
guaranteeing a high standard of reproducibility.
Anyhow it is recommended, before starting production, to prepare a sufficient number of welding samples (about 50)
which correspond the later welding geometry. We recommend to adjust the wire arrival about 0,5 - 1,0 mm below the
electrode. The wire should arrive perpendicularly to the electrode and tangentially to the tube.
The welding head should be hooked up with an elastic balancer.
The orbital weld head allows to perform a great number of high quality weldings. In order to take advantage of this
feature it is recommended to organize in advance the welding position:
• Be sure to have enough gas bottles.
• Be sure to have enough electrodes (pre-cut and shaped).
• Prepare ceramic nozzles, wire nozzles, gas lenses, collets and wire spools.
The most important point to achieve a perfect weld is a perfect cleaning of the tubes and the joints to be welded.
Be sure that there is no oxide, chips, grease or any impurities.
5.2
Positioning of the welding head
The low weight and the efficient centering devices allow an easy and economic way of using the welding head.
Hook up the welding machine on a balancer (size up to 15 kg).
In order to obtain an efficient support on the tube sheet it is recommended to have to rope about 2 meters long and that
it may be angled 15 - 20° towards the tube sheet. In this case the welding head is slightly pressed on the tube plate.
5.3
Starting of the welding heads
In case the welding head is connected to a Orbitalum controller, pushing start / stop button the welding cycle will start (real
cycle or simulation).Pushing a second time the same button the welding will be stopped (cycle end with downslope).
5.4
Preparation and replacement of the electrode
A correct geometry of the electrode is very important in order to guarantee a good quality of the welding. This geometry
depends on the current you have chosen. For your reference see the enclosed table.
The electrode must be replaced every time you can see differences from the original geometry. In this case the welding
parameters will change and the reproducibility is no longer guaranteed.
For the replacement of the electrode unscrew the cover the collet and collet body. In this way you can extract the elec-
trode to be replaced.