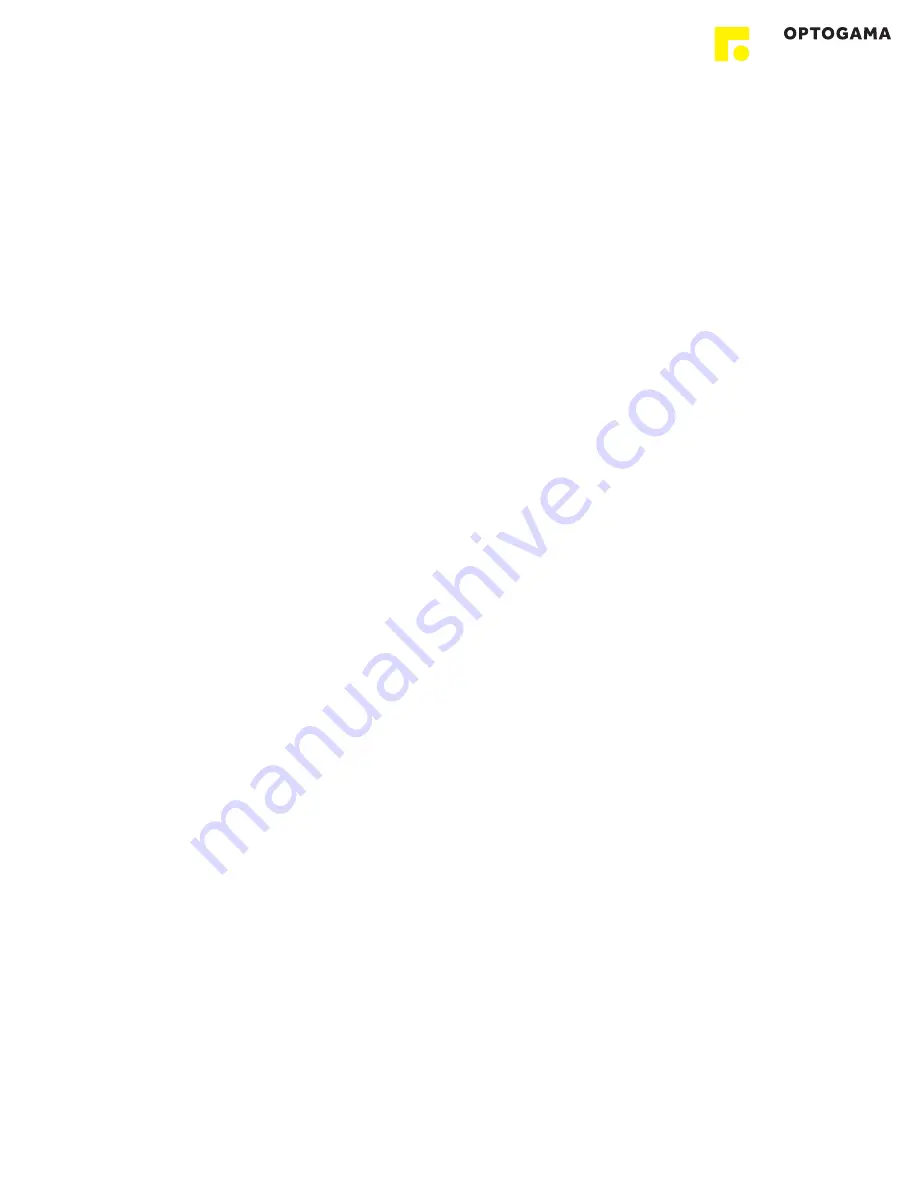
5. Troubleshooting
5.1. STATUS bits explanation
Bit0 – driver error. This bit is high when some error in motor
driver happens.
Bit1 – driver high temperature warning. Bit is high when
motor driver is in pre-warning temperature range which
exceeds 120°C.
Bit2 -
driver over temperature. Bit is high when motor driver
reaches 150°C. After triggering this temperature the driver
remains switched off until the system temperature falls
below 120°C. The thermal shutdown is just an emergency
measure and temperature rising is prevented by the design.
Bit3 – dome type of error in the driver load. Motor driver
power stages are pMROected against a short circuit
condition. Once a short condition is safely detected the
corresponding driver bridge becomes switched off, and flag
becomes set.
Bit4 - load warning – open load on phase A or B of stepper
motor driver. However, the flag have just informative
character and do not cause any action of the driver. This
flag works only at low motor velocity operation, which is not
the case.
Bit5 – under voltage error. Indicates an under voltage on the
motor driver charge pump. The driver is disabled in this
case.
Bit6 – external memory error working/calibration data may
be corrupted. Flag is set if there was an error reading data
from EEPROM.
Bit7 – reset has occurred. Indicates that the motor driver
has been reset since the last read access to STATUS All
registers have been cleared to reset values.
Bit8/Bit9 – left/right limit switch is pressed. Limit switches
are used as reference point in homing procedure.
Bit10 – StallGuard is active. Signal that motor stall is
detected. StallGuard provides sensor-less stall detection
and mechanical load measurement.
Bit11 – motor is stand still. This flag indicates motor stand
still in each operation mode.
Bit12 – motor target velocity reached. Signals, that the
target velocity is reached. This flag becomes set while
actual and maximum speed match.
Bit13 – target position reached. Signals, that the target
position is reached. This flag becomes set while actual and
target position match.
Bit14 – Homing procedure was run after the reset.
Indicates, that after power on stepper motor was homed
and is ready for precise position control.
Bit15 – Device calibration is done. Indicates, that
“MRO>DEF!” command was send and minimum laser
power position is known.
19
Содержание MRO
Страница 1: ...MANUAL v3 3 MRO MOTORISED ROTATOR KEY for DISCOVERIES ...
Страница 20: ...5 2 Serial communication example in Python 20 ...
Страница 21: ...6 Technical information 6 1 MRO drawings 21 ...
Страница 23: ...6 3 Power supply 23 ...
Страница 24: ...6 4 RS232 cables 24 ...
Страница 25: ...OPTOGAMA UAB Mokslininku str 2A LT 08412 Vilnius Lithuania 37052194884 sales optogama com www optogama com ...