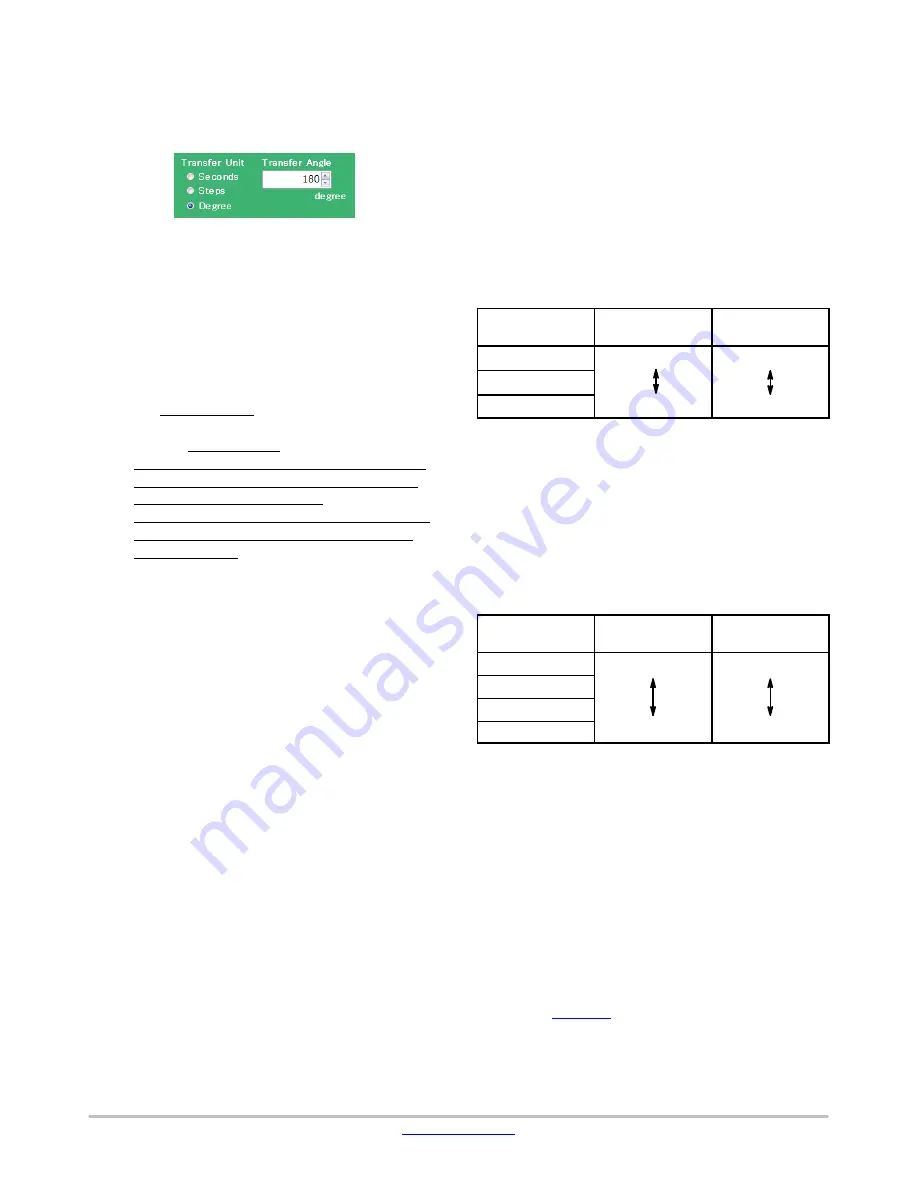
LV8702VSLDGEVK
10
xample 3: Rotating the motor
180 degrees
Transfer Unit =
Degree
Transfer Angle =
180 [degree]
9. When the Start button is pressed, the motor will
rotate. If changes to the Output Current, Excitation
or Motor Speed are made, the changes will take
effect upon pressing the Start button.
To change the direction of rotation, it is
recommended to stop the motor first with the Stop
button, change the value, and then press the Start
button to begin the motor rotation.
Pressing the Stop button causes the motor to stop,
and hold the torque.
When the Free button is pressed, the motor will
stop and lose the torque.
To maintain the position while the motor rotates,
or to pause the motor and restart from the same
position, select the Stop button.
At this time, because of
the current still flowing
to the motor,
attention must again be paid to
heat generation.
10. Set the specifications of the power supply and
motor to be used.
Supply Voltage... Power supply voltage
MAX Supply Current... Maximum power supply
current
Motor Rated Current... Motor Rated Current
Motor Winding Resistance... Motor coil resistance
Max Output Current Set buttons ... Calculate the
maximum output current from the above four
setting values, and 5 limit the set range of the
output motor current to enable safer motor driving.
11. Set the high
−
efficiency drive function.
(This function does not work in slow speed and
fast speed range where the feedback signal can’t
be stably detected. This function cannot be
selected when Full Step is set.)
The high
−
efficiency drive function automatically
optimizes the motor current according to the motor
load and rotational speed. By turning on this
function, power consumption, heat, vibration, and
noise can be reduced. The high
−
efficiency drive
function consists of the following three
parameters.
Efficiency
... ON/OFF of high
−
efficiency drive
function
When the high
−
efficiency drive function is turned
on, the motor current is automatically adjusted
within the range of the limit set in 5.
Drive Margin
... Margin adjuster Function
Adjust the margin from the minimum current that
can rotate the motor.
When the margins are set to Small, the current
consumption is the smallest, but the number of
boost
−
ups may be increased for small
load
−
changes.
For this reason, set the margin to be larger for
applications with excessive load variation.
Drive Margin
Current
Consumption
Robustness
Small
Low
Normal
Weak
Strong
Middle
Large
Boost Up
... boost
−
up adjuster function
This process increases the motor current rapidly
and temporarily in order to maintain the motor
rotation in response to load variation.
Increasing the boost increases the rush load
resistance, but increasing the boost increases the
rotational stability.
The worsened of rotational stability can be
suppressed by increasing the Drive Margin.
Boost Up
Robustness
Rotational
Stability
Min
Weak
Strong
Stable
Unstable
Low
High
Max
12. Set the reset function.
The reset function resets the excitation position
and locks the motor.
[ON] ... Reset ON
[OFF] ... Reset OFF
Neither is turned off the power.
13. Voltage reading function
14. Status check function
15. GUI Language Settings
16. GUI Tool Tip Display
17. Help function
for more information)