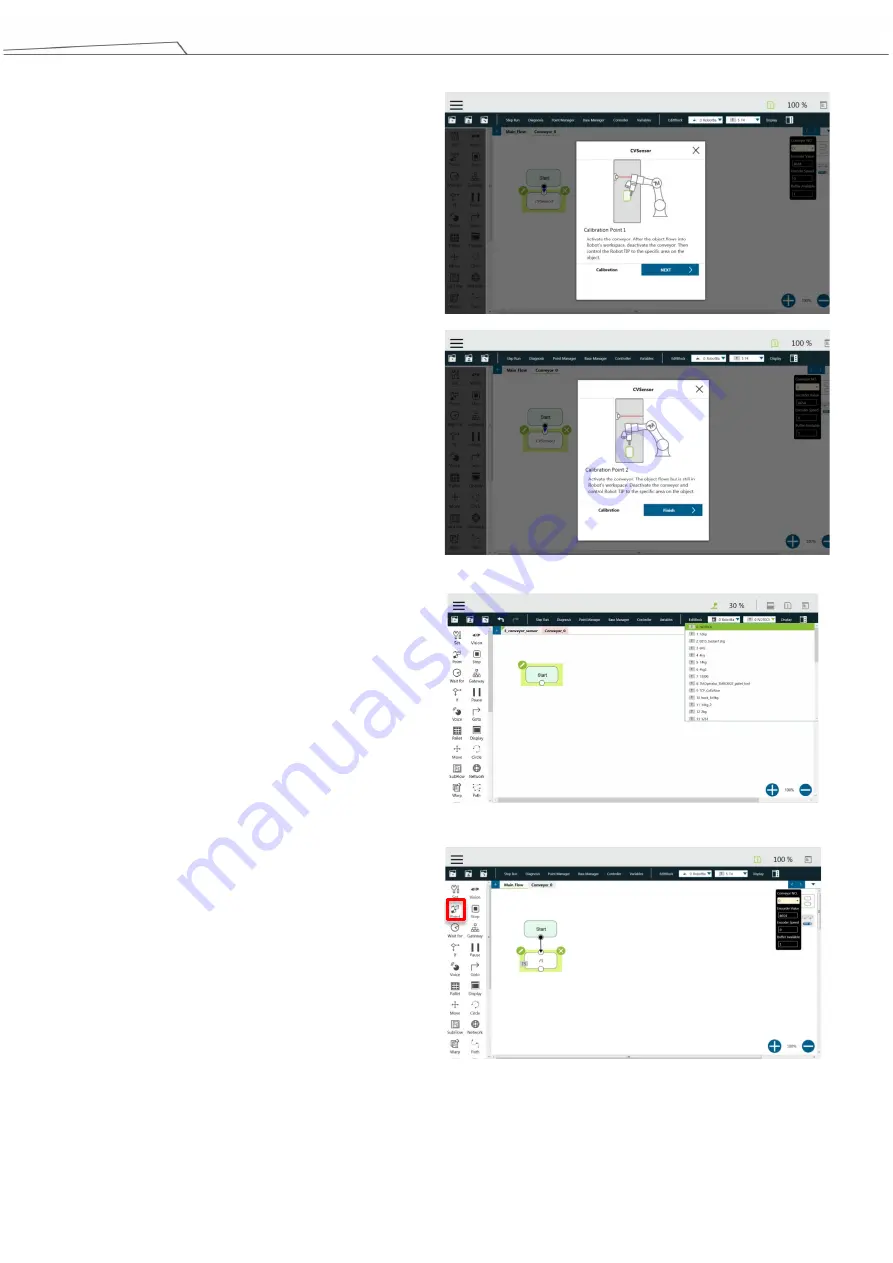
TM Conveyor Tracking
Software version: TMflow 1.76
27
6
Calibration
•
When the conveyor is stopped as
instructed in the last step, move the
robot so it detects or contacts the
object to set Calibration Point 1.
Click NEXT.
•
Activate the conveyor again to set
it in motion. Stop the conveyor
when the part is in the robot's
working area.
•
Hand-guide the robot to detect or
contact the same point of the
object to set Calibration Point 2.
Click “Finish” to complete
calibration.
Figure 23 Two calibration points
7
Select Tool
•
Switch back to main thread to
select the tool you will use during
the application
Figure 24 Switch tool
8
Set initial point
•
Drag Point Node to the screen and
set it as the robot’s initial work
point.
•
(T5 is the selected tool in this
example)
Figure 25 Point Node