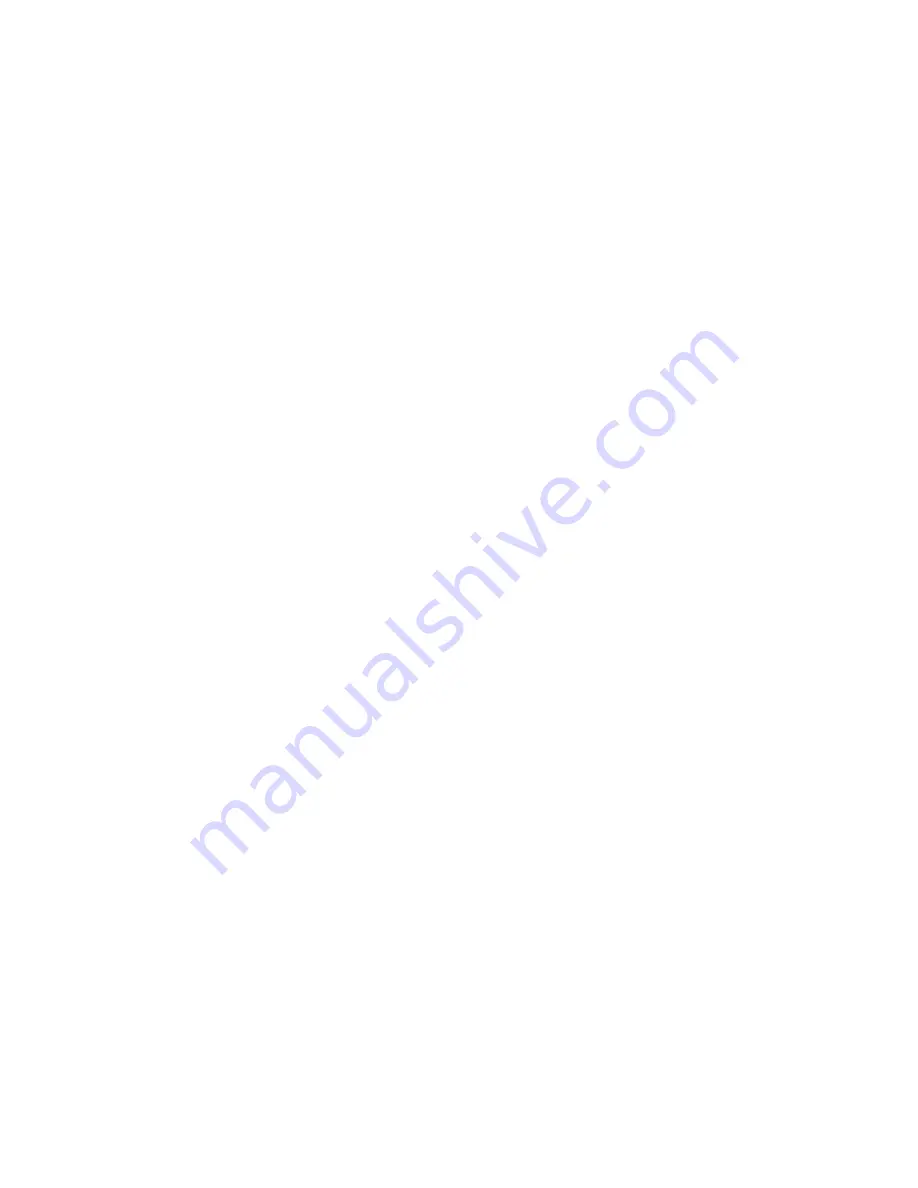
2
SAFETY AND GENERAL INFORMATION
Save these instructions.
For your safety, read, understand, and follow the information provided with and on this
device before using. The owner and/or operator shall have an understanding of the device, its operating characteristics
and safety operating instructions before operating the equipment. The owner and/or operator shall be aware that use
and repair of this product may require special skills and knowledge. Instructions and safety information shall be read
to and discussed with the operator in the operator's native language, making sure that the operator comprehends
their contents, before use of this equipment is authorized. If any doubt exists as to the safe and proper use of this
device, remove from service immediately.
Inspect before each use.
Do not use if abnormal conditions such as cracked welds, damaged, loose or missing
parts are noted. Any equipment that appears damaged in any way, is found to be worn, or operates abnormally shall
be removed from service until repaired. If the equipment has been or is suspected to have been subjected to an
abnormal load or shock, immediately discontinue use until inspected by a factory authorized repair facility (contact
distributor or manufacturer for list of authorized repair facilities). It is recommended that an annual inspection be
made by an authorized repair facility. Labels and Operator's Manuals are available from the manufacturer.
PRODUCT DESCRIPTION
Hydraulic Truck Jacks are designed to lift, but not support, rated capacity partial vehicle loads consisting of one end
of a vehicle. Immediately after lifting, support loads with a pair of appropriately rated jack stands.
PREPARATION
Reference Replacement Parts pages 6 and7 for parts location & assembly sequence. Assemble, align and insert the
handle assembly and handle position bar into the handle sleeve, then tighten the bolt on handle sleeve to prevent
accidental removal of handle while in use.
Before Use
1. Verify that the product and application are compatible, if in doubt call Omega Technical Service (888) 332-6419.
2. Before using this product, read the operator's manual completely and familiarize yourself thoroughly with the
product, its components and recognize the hazards associated with its use.
3. To familiarize yourself with basic operation, locate and turn the release valve (handle knob):
a.
Clockwise
until firm resistance is felt to further turning. This is the ‘
CLOSED
’ release valve position used to
raise
the load.
b.
Counter-clockwise
, no more than 1 full turn from closed position. This is the ‘
OPEN
’ release valve position used
to
lower
the load. The further the release valve is turned counter-clockwise, the faster the load descends.
4. With ram fully lowered, remove the oil filler screw. Check oil level. Proper oil level should be just below the rim of
the opening. Reinstall the oil filler screw.
5. Pour a teaspoon of good quality air tool lubricant into the air supply inlet of the lift control valve. Connect to air
supply, then squeeze the lift control valve for 3 seconds to evenly distribute lubricant.
NOTICE:
These models are equipped with 1/4" NPT air couplers. If installing a different air coupler, ensure thread
tape or compound is used on connections. To ensure dependable, trouble free operation an inline air dryer and oiler
is recommended.
6. Ensure that jack rolls freely. Raise and lower the unloaded ram throughout the lifting range before putting into
service to ensure the jack operates smoothly. Replace worn or damaged parts and assemblies with Omega
authorized replacement parts only.
Bleeding/Venting Trapped Air
Model 23301C only:
With the release valve in the OPEN position (Step 3b above) and with ram fully lowered, locate
and remove the oil filler screw. This will help release any pressurized air which may be trapped within the reservoir.
Activate air motor for 10 seconds to vent reservoir pressure. Reinstall the oil filler screw.
Models 23221C and 23222C only:
1. Open oil filler plug.
2. Open release valve.