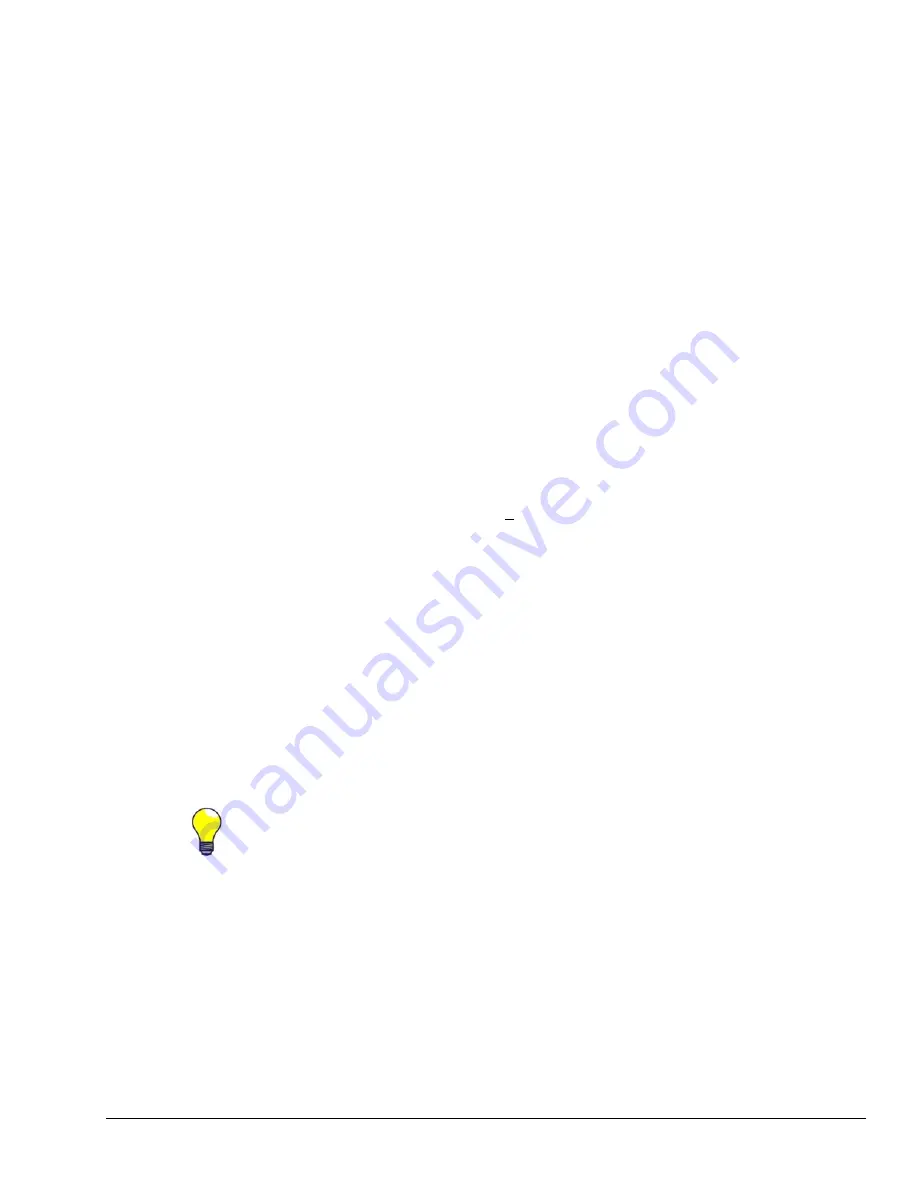
Adjust the Offset
For the associated channel, apply the first calibrated load to each gage (typically no-load) and set the
voltage to 0.0V for each transducer. This is accomplished by adjusting the trimpot labeled OFFSET. If the
first point is actually a calibrated load, you will need to move the load to each gage, one at a time, to adjust
its associated offset.
Adjust the Input and Scale Amplifier Gain
Complete the following steps to adjust the channel gain.
1.
Apply the second load to each gage channel. The value of this load should approximate that of the
maximum expected load. For the best results, a gain should be selected so that the bridge’s maximum
output equals 90% of the A/D’s input range.
2.
Calculate the desired voltage for the second point using the following equation:
V
D
= (L
A
/L
M
) * V
I
* 90%
Where:
V
D
= Desired voltage for 2
nd
point of calibration
L
A
= Applied load used in calibrating the 2
nd
point
L
M
= Maximum load expected during usage
V
I
= Input voltage range
Example:
The load standard that will be applied to the gage as the 2
nd
point in the 2-Point calibration is
100lbs. The maximum expected load during usage is 150lbs. The programmable input range of
the data acquisition system is set for +5V. The desired output voltage of the strain gage signal
conditioning electronics is:
V
D
= (100/150) * 5 * 0.90 = 3V
In this example, we should adjust the GAIN and SCALE trimpots until a value of 3V is
measured.
If 150lbs is applied to the gage, a voltage of 4.5V will be measured.
V
D
= (150/150) * 5 * 0.90 = 4.5V
3.
Apply the second calibrated load to each gage and set the voltage to V
D
, as derived in step 2. Do this
for each transducer by adjusting the trimpots labeled GAIN and SCALE for the associated channel.
Note that the GAIN trimpot provides most of the amplification (course adjustment), while the SCALE
trimpot allows for fine-tuning.
Repeating the Process
Since adjusting the gain for the first time will have an affect on the offset, it is recommended that
offset and gain adjustment be performed twice for each channel.
DBK Option Cards and Module
879895
DBK16, pg. 27
Содержание OMB-DBK-34A
Страница 6: ...ii...
Страница 10: ...viii 917594 DBK Option Cards Modules User s Manual This page is intentionally blank...
Страница 32: ...pg 22 DBK Basics 967794 Daq Systems...
Страница 60: ...2 10 System Connections Pinouts 877095 DBK Option Cards and Modules...
Страница 84: ...5 8 Troubleshooting Tips 967094 DBK Option Cards and Modules...
Страница 94: ...DBK200 Series Boards DBK200 DBK201 DD 10 949794 Dimensional Drawings...
Страница 96: ...DBK205 DBK205 DD 12 949794 Dimensional Drawings...
Страница 97: ...DBK206 Dimensional Drawings 949794 DD 13...
Страница 98: ...DBK207 CJC These dimensions apply to the both the DBK207 and the DBK207 CJC DD 14 949794 Dimensional Drawings...
Страница 99: ...DBK208 Dimensional Drawings 949794 DD 15...
Страница 100: ...DBK209 DD 16 949794 Dimensional Drawings...
Страница 101: ...Dimensions for Miscellaneous Components DIN 1 Dimensional Drawings 949794 DD 17...
Страница 102: ...DIN 2 DD 18 949794 Dimensional Drawings...
Страница 103: ...POD 1 for DBK83 POD 1 for DBK83 Dimensional Drawings 949794 DD 19 Dimensional Drawings 949794 DD 19...
Страница 104: ...TB 100 Terminal Connector Option 68 pin SCSI III Screw Terminal Board DD 20 949794 Dimensional Drawings...
Страница 105: ...DBK Cards Modules Part 1 of 2...
Страница 106: ...DBK Cards Modules...
Страница 108: ...DBK Cards Modules...
Страница 148: ...DBK7 pg 14 879895 DBK Option Cards and Modules...
Страница 168: ...DBK15 pg 6 889094 DBK Option Cards and Modules...
Страница 182: ...DBK16 pg 14 879895 DBK Option Cards and Modules...
Страница 200: ...DBK16 pg 32 879895 DBK Option Cards and Modules...
Страница 206: ...DBK17 pg 6 879895 DBK Option Cards and Modules...
Страница 218: ...DBK20 and DBK21 pg 6 879795 DBK Option Cards and Modules...
Страница 232: ...DBK24 pg 8 879795 DBK Option Cards and Modules...