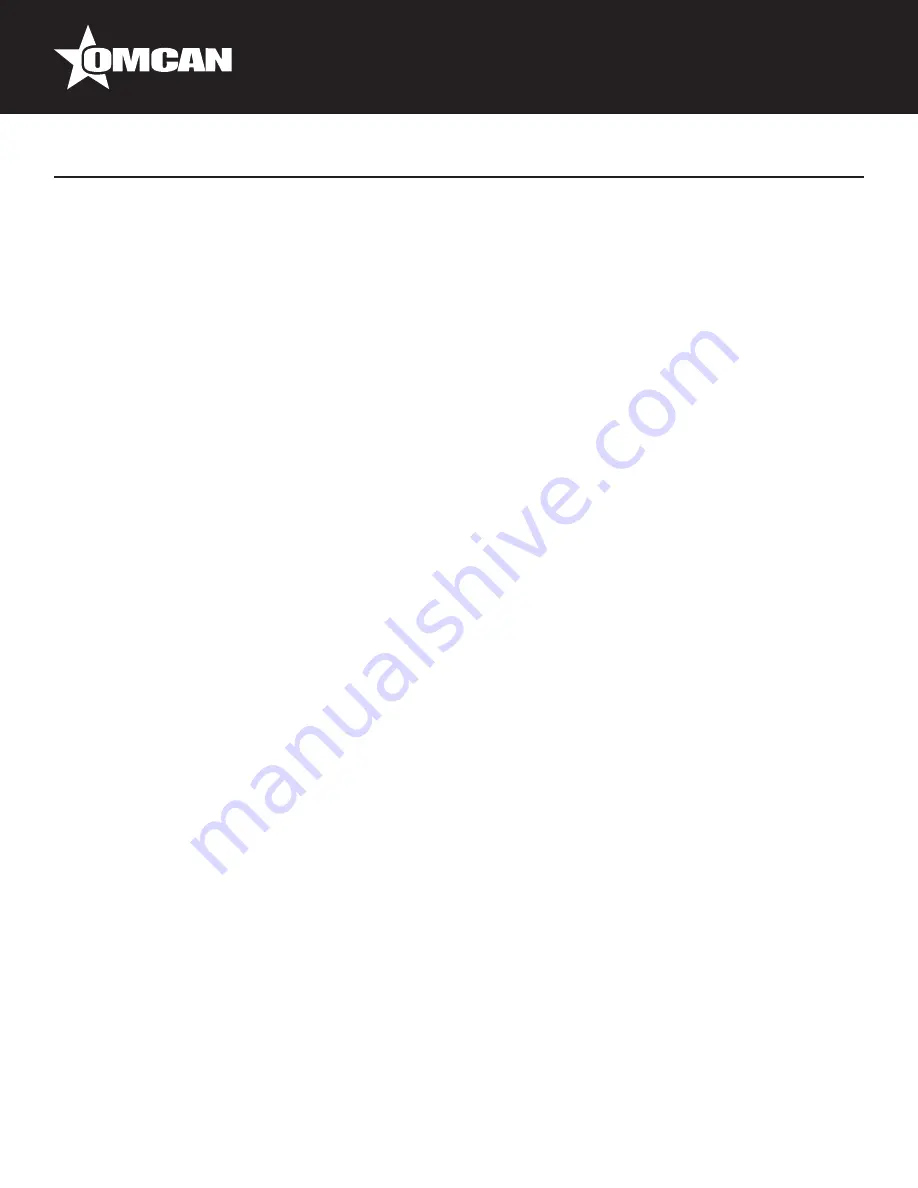
15
Maintenance
pressure at which the machine is run, the presence of humidity or residual water, etc. Normally it can last
between 2.500 and 5.000 hours of service. If the oil loses viscosity, becomes impure, or turns a whitish color
from having had water pumped into it, drain the oil by emptying the housing via the plug located at the bottom
of the machine. Refill the oil following the instructions found in the INSTALLATION section above. Because
there is no natural loss of oil or oil vapors, an adequate level of hydraulic oil should last several years, making
it unnecessary to check the oil level regularly. If the oil level is insufficient, the piston will not move smoothly,
since air will be entering the circuit.
Changing the hydraulic oil:
Remove the oil outlet plug located at the bottom of the base and drain the
reservoir, emptying the oil into an appropriate recipient (please recycle used oil). Replace the plug and seal
the oil outlet site hermetically. Using a funnel, fill the reservoir with 10 liters (for H15/H20 models), 15 liters
(for H26/H31 models) or 25 liters (for H42/H52 models) of hydraulic oil via the tank opening. Do not fill the
reservoir to the top since a certain amount of air must be present to allow for expansion. Use oils for medium
pressure hydraulic assemblages (approx. 100 bar), and of a viscosity of approximately 5º Engler (equivalent to
IS03498: cat HL VG46 or DIN8659: HL-46). After filling the reservoir, raise and lower the piston several times
to eliminate air pockets from the hydraulic circuit.
Oil filter:
Located inside the oil reservoir, the oil filter is not accessible to the user and should only be replaced
by a qualified technician. To remove the oil filter remove the two screws that attach the closing clamp to the
filter and pull the filter outward. Normally, the filter should not become dirty or present any abnormality. If
the filter must be changed, use a similar filter with a thread of 3/8” BSP and a filtering capacity of 10 liters
per minute, (5 liters per minute for H15/H20). After reassembling the unit, the closing clamp must be sealed
hermetically.
Oil temperature:
Because of the pressure transmitted by the pump, after prolonged periods of use the
hydraulic oil may reach temperatures of up to 60ºC (140ºF) and the base side panel may become warm to the
touch. This machine is not designed to withstand permanent, uninterrupted use at high pressure, but rather to
run intermittently with pauses to allow for the dissipation of the heat generated, the amount of which depends
on the consistency of the mixture.
Cylinder ram:
In order to lengthen the life of the hydraulic cylinder ram, leave the piston head at the bottom of
the cylinder when the machine is not in use. The ram will thus be completely submerged in hydraulic oil.
Lid closure:
The lid of the barrel can be shut more or less tightly depending on how watertight the closure
should be. If the mixture is customarily dry, the closure can be loosened, making it easier to close the lid. If,
however, the mixture contains more liquid, the closure should be tighter to avoid leaks. To loosen the lid in E
models, loosen the upper lid screws until the desired seal is obtained. For P models, loosen the nuts located
beneath the clamp and either loosen or tighten the 2 lid fixing bolts. Then retighten the 2 lock nuts completely.
To keep crystallized residue (from salts, spices, etc.) from impeding the proper closure of the lid, remember to
rinse the lid bolt and bearing with hot water after using the machine.
Lack of power:
If the machine seems to lack power, notify the service department of the dealer where the
machine was purchased. They should verify the following points: that the air holes located at the base of the
barrel are completely free of obstruction, that the piston and the piston gaskets are perfectly clean and free
of residue which could inhibit the movement of the piston, that the voltage of the power source is compatible