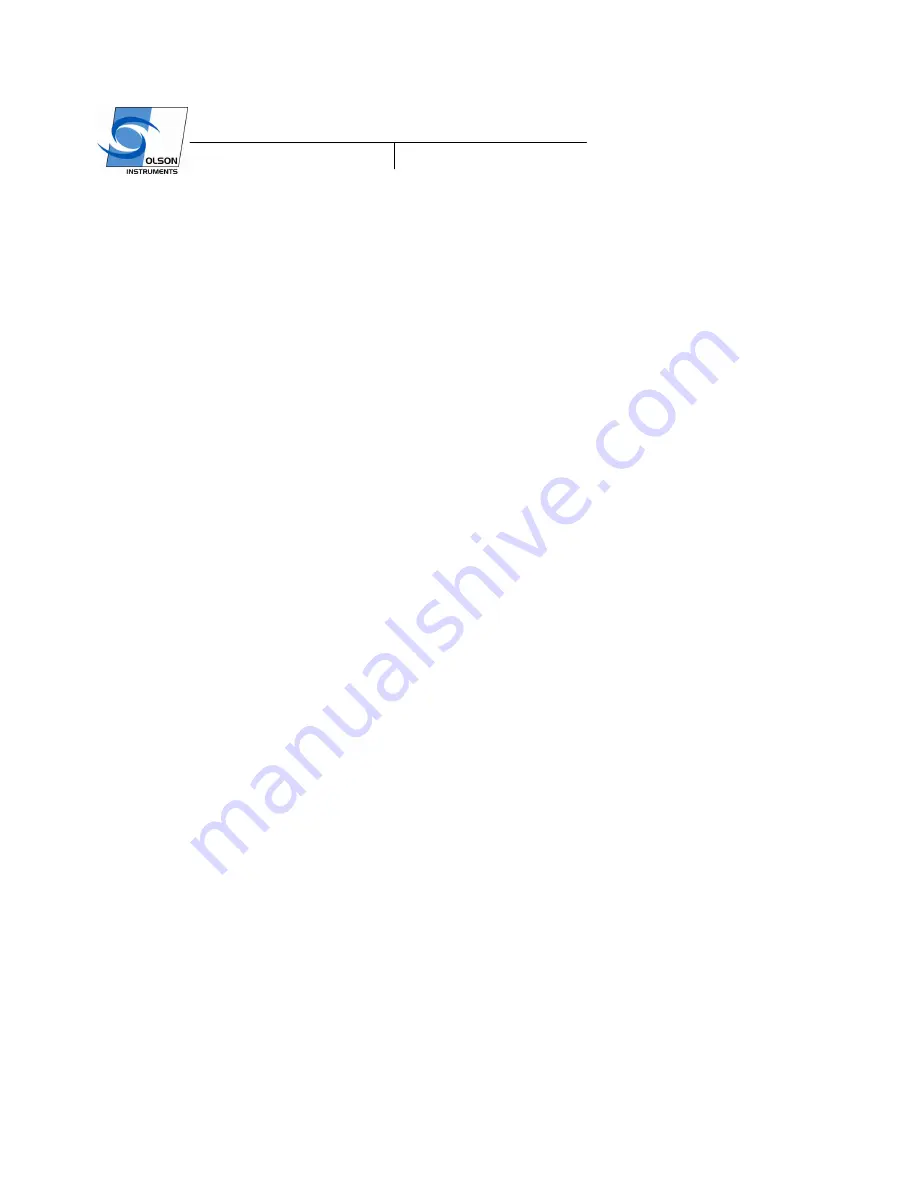
I
MPACT
E
CHO
(IE)
www.olsoninstruments.com
www.olsonengineering.com
INTRODUCTION
Post-tensioned systems have been widely used for infrastructure bridge transportation systems since late
1950s. However if a good quality control plan is not implemented during construction, there is the
potential problem during construction that the duct may not be fully grouted. This results in voids in
some areas or inefficient protection for prestressing steel. Over the long term, water can enter the tendon
ducts in the void areas resulting in corrosion of the tendon. The collapse of the Brickton Meadows
Footbridge in Hampshire (UK) in 1967 is the first serious case of corrosion of tendons leading to major
catastrophe (1). In 1985, the collapse of a precast segmental, post-tensioned bridge in Wales (Ynys-y-
Gwas Bridge) was attributed to corrosion of the internal prestressing tendons at mortar joints between
segments (1 and 2). Corrosion-related failures of post-tensioning tendons have been found in several
major segmental bridges such as the Niles Channel Bridge near Key West, FL in 1999 and Midway
Bridge near Destin, FL in 2000 (3). In addition to actual failures, corrosion damage was found in many
post-tensioned bridge ducts in bridges still in use in Florida and East Coast areas (4).
In post-tensioned structures, quantifying the incidence of corrosion is further complicated by
limitations in techniques for detecting corrosion. Condition surveys of post-tensioned structures are often
limited to visual inspections for signs of cracking, spalling and rust stain. This limited technique may
overlook corrosion activity. Corrosion damage in post-tensioned elements has been found in situation
where no exterior indications of distress were apparent (4). As a matter of fact, the Ynys-y-Gwas Bridge
in Wales had been inspected 6 months prior to the collapse, and no apparent signs of distress were
observed (2). Examples such as this one lead some to fear that inspection based on limited exploratory
or visual inspections may be unconservative and may produce a false sense of security. The X-ray
method is the oldest technique applied successfully to detect unfilled ducts. However, the method suffers
from many disadvantages. The first disadvantage is that the X-Ray test needs accesses to both sides of
the structure, which is not usually practical in testing bridge ducts. Second, the inspection areas are
relatively small and the test time relatively large resulting a slow testing process. Finally, the need for
sufficient radiation protection and personnel evacuation is usually a problem. Therefore, it is important to
develop a reliable method to practically inspect the quality of grout fill inside the ducts non-destructively
after the grouting process is complete and for inspection of older bridges.
BACKGROUND OF THE IMPACT-ECHO TECHNIQUE
The Impact-Echo test involves dynamically exciting a concrete structure with a small mechanical
impactor and measuring the reflected wave energy with a displacement transducer. The resonant echoes
in the displacement responses are usually not apparent in the time domain, but are more easily identified
in the frequency domain. Consequently, linear amplitude spectra of the displacement responses are
calculated by performing a Fast Fourier Transform (FFT) analysis to determine the resonant echo peak
frequencies in the frequency domain from the displacement transducer signals in the time domain. The
relationship among the echo frequency peak f, the compression wave velocity V
P
, and the echo depth
D
is
expressed in the following equation:
(1)
D =
β
V
p
/(2*f)
where
β
is a shape factor which varies based on geometry. The value of
β
was found by theoretical
modeling to be equal to 0.96 for a slab/wall shape (5).