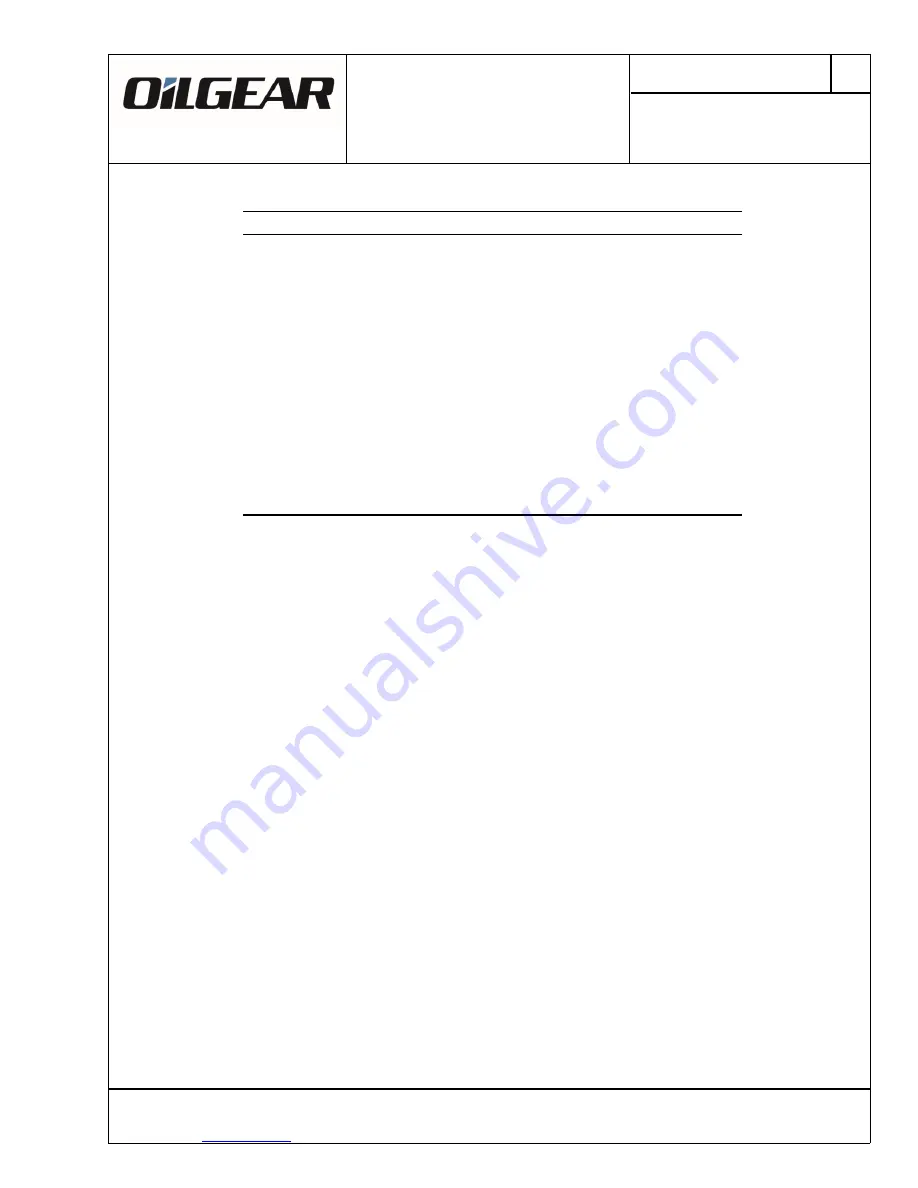
EPC
SERVO AMPLIFIER MODULE
Part Number L723888-3xx
ELECTRONIC
Telephone: (231) 929-1660
Oilgear
Fax:
(231) 929-7879
1424 International Dr
Issued May 31, 2018
Web Site:
www.oilgear.com
Traverse City, MI USA 4 9 6 8 6
Bulletin 836260F
13
4.2.3 Pressure Control Programs (40x, 41x)
Program Item Range
Description
400
1 to 100
Program 1: Pressure Command Preset
401
0 to 5
Program 1: Pressure Command Source
402
1 to 5
Program 1: Pressure Feedback Source
403
0 to 1
Program 1: Program Output Destination
404
0 to 100
Program 1: KP
405
0 to 100
Program 1: KI
410
1 to 100
Program 2: Pressure Command Preset
411
0 to 5
Program 2: Pressure Command Source
412
1 to 5
Program 2: Pressure Feedback Source
413
0 to 1
Program 2: Program Output Destination
414
0 to 100
Program 2: KP
415
0 to 100
Program 2: KI
Table 4: Pressure Control Programs Configuration
Function Programs 1 and 2 provide for basic Pressure Control. Program 1 is configured in program
items 400 through 405 or from the Program 1 Form. Program 2 is configured in program items 410
through 415 from the Program 2 Form.
Pressure Command Preset
: The Pressure Command Preset allows for direct numeric input for the
control program. The preset is configured as a percentage, with 0% being equivalent to a 0VDC input
signal and 100% being equivalent to a +10VDC signal.
Pressure Command Source
: The Pressure Command Source selects the source of the pressure
command for the program. Valid entries are (0) Preset Value, (1) Analog Input 1, (2) Analog Input
2, (3) Analog Input 3, (4) LVDT 1 (Analog Input 4), or (5) Ramp 1. If the Preset Value is chosen,
the Pressure Command Preset is used as the program command.
Pressure Feedback Source
: The Pressure Feedback Source selects the source of the pressure
feedback for the program. Valid entries are (1) Analog Input 1, (2) Analog Input 2, (3) Analog
Input 3, (4) LVDT 1 (Analog Input 4), or (5) Ramp 1.
Program Output Destination
: The Program Output Destination selects the output of the program.
Valid entries are (0) Pump Controller or (1) Direct. If the Pump Controller is chosen, the output of the
Program will be the input to the Pump Controller module. If Direct is chosen, the output of the Program
will by-pass the Pump Controller module and is passed directly to the servo driver. Under most
circumstances, the Pump Controller should be chosen as the output destination.
KP
and
KI
: KP and KI provide the proportional and integral constants, respectively, for the PI
control algorithm. Both terms are expressed as 0 to 100% of a maximum value. The PI control
loop can be made a P-only control loop by setting the KI term to 0. Likewise, the PI control loop
can be made an I-only control loop by setting the KP term to 0.