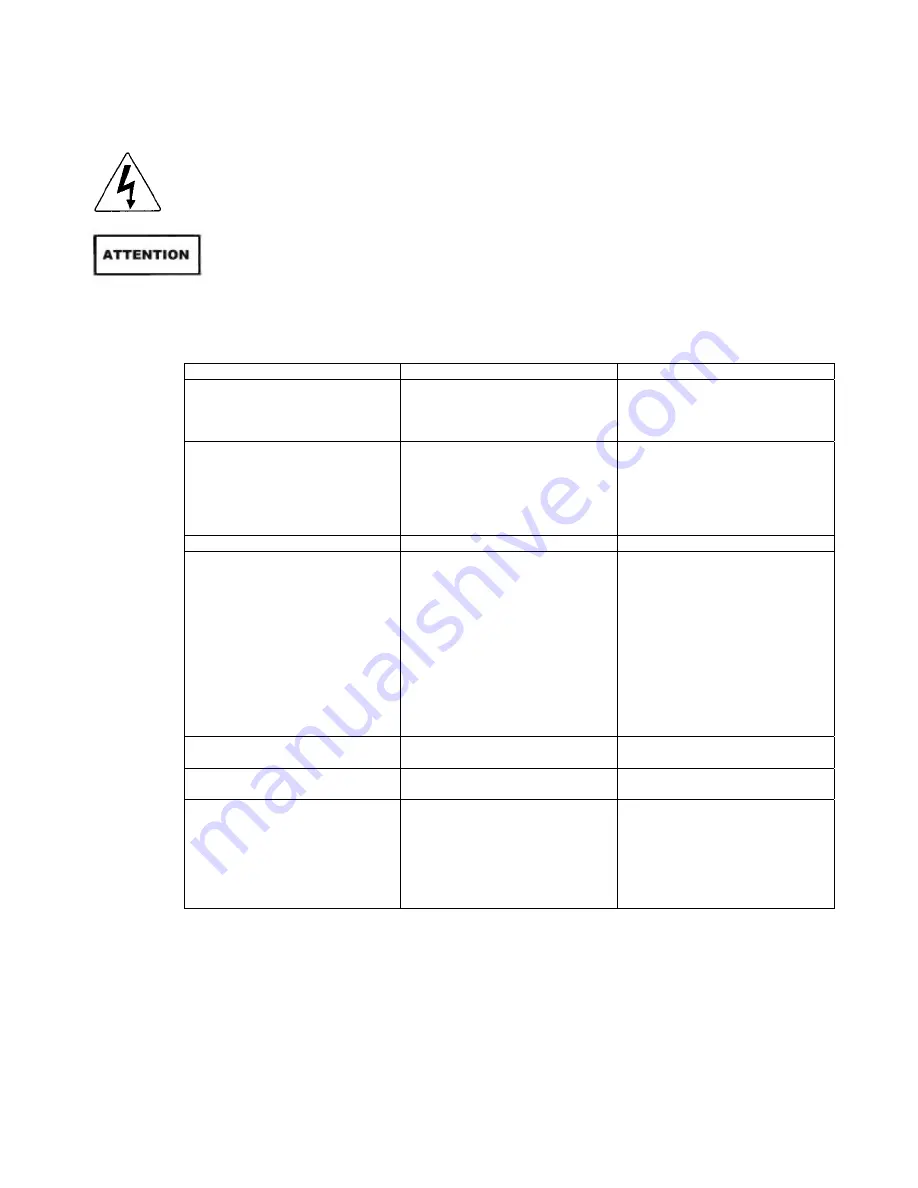
15
7.
Trouble Shooting
Electrical energy can cause severe injuries. Devective electrical
components to be immediately replaced, possible causes for accidents
to be eliminated without delay
Any repair work must only be carried out by qualified personnel.
Only original OERTZEN equipment to be installed, as otherwise
warranty and Declaration of Conformity will be void, health and
safety standards are not guaranteed.
During repair or maintenance work, unit to be disconnected from
electrical network.
Faiure Cause
Remedy
Motor stops
- Fuel tank empty
- Motor oil low level
- Petrol filter blocked
- Sparking plug burnt
- Fill tank
- Fill up oil up to max. mark
- Clean/replace filter
- Replace sparking plug
Motor springt nicht an
- Motor oil low level.
- Counter pressure high
- Battery exhaused
- Ignition switch in position "Off"
- Petrol cock closed
- Choke open
- Fill up oil up to max. mark.
- Release unloader valve
- Charge battery
- Put switch into position "On"
- Open petrol cock
- Close choke
Pump pressure high
- Nozzle clogged
- Clean remove and nozzle
Operating pressure not achived/
varies
- Air in unit
- Insufficient water supply
- Nozzle worn
- Incorrect nozzle
- Nozzle clogged
- Water strainer blocked
- Unloader valve leaking
- Suction side of pump leaking
- Suction valves sticking
- Vent unit
- Supply line to be min.
”
- Replace nozzle
- Install correct nozzle
- Remove/clean nozzle
- Clean filter
- Call service
- Tighten hose clamps
- Carefully loosen valves by
means of a scew driver, if
needed, remove and clean
valves.
Vibrations on high pressure hose
and spray pistol
- Air in unit
- Open handle on pistol unless
continuous pressure is achieved
Heavy vibrations on unit
- Plunger blocked
- Stop unit immediately,
call service
No detergent injection
- Detergent tank empty
- Dosing valve or regulating
handle closed
- Low pressure nozzel in double
lance blocked
- Non-return valve blocked
- Fill tank
- Open
- Remove and clean nozzle
- Blow compressed air into
detergent hose
Содержание M 240
Страница 16: ...16 ...