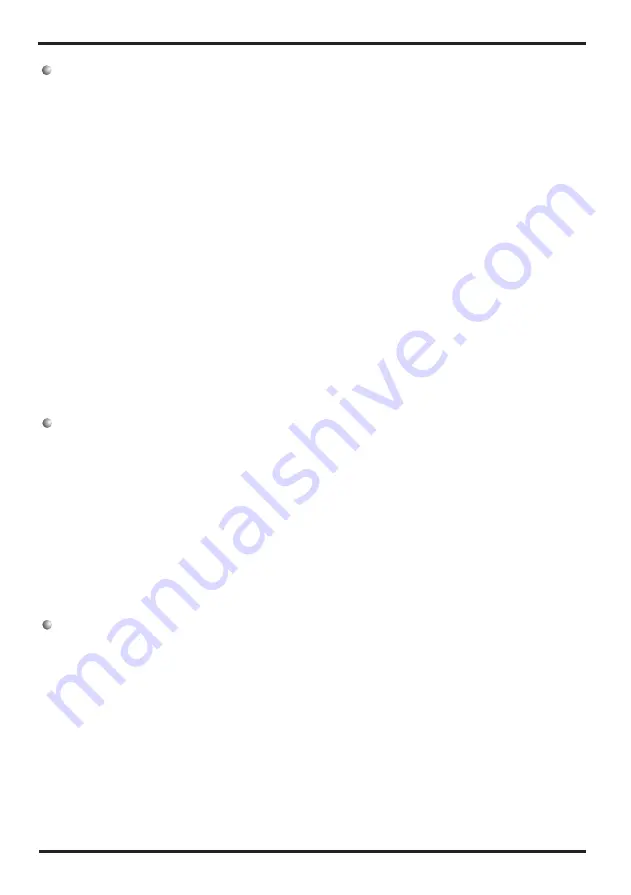
Charging procedures
In addition to conventional charging procedures, the following requirements shall be
followed.
–
Ensure that contamination of different refrigerants does not occur when using charging
equipment. Hoses or lines shall be as short as possible to minimise the amount of
refrigerant contained in them.
–
Cylinders shall be kept upright.
–
Ensure that the refrigeration system is earthed prior to charging the system with
refrigerant.
–
Label the system when charging is complete (if not already).
–
Extreme care shall be taken not to overfill the refrigeration system.
Prior to recharging the system it shall be pressure tested with OFN. The system shall be
leak tested on completion of charging but prior to commissioning. A follow up leak test shall
be carried out prior to leaving the site.
Decommissioning
Before carrying out this procedure, it is essential that the technician is completely familiar
with the equipment and all its detail. It is recommended good practice that all refrigerants
are recovered safely. Prior to the task being carried out, an oil and refrigerant sample shall
be taken in case analysis is required prior to re-use of reclaimed refrigerant. It is essential
that electrical power is available before the task is commenced.
a) Become familiar with the equipment and its operation.
b) Isolate system electrically.
c) Before attempting the procedure ensure that:
. Mechanical handling equipment is available, if required, for handling refrigerant cylinders;
. All personal protective equipment is available and being used correctly;
. The recovery process is supervised at all times by a competent person;
. Recovery equipment and cylinders conform to the appropriate standards.
d) Pump down refrigerant system, if possible.
e) If a vacuum is not possible, make a manifold so that refrigerant can be removed from
various parts of the system.
f) Make sure that cylinder is situated on the scales before recovery takes place.
g) Start the recovery machine and operate in accordance with manufacturer's instructions.
h) Do not overfill cylinders. (No more than 80 % volume liquid charge).
i) Do not exceed the maximum working pressure of the cylinder, even temporarily.
j) When the cylinders have been filled correctly and the process completed, make sure that
the cylinders and the equipment are removed from site promptly and all isolation valves on
the equipment are closed off.
k) Recovered refrigerant shall not be charged into another refrigeration system unless it
has been cleaned and checked.
30
5. MAINTENANCE AND INSPECTION
5. MAINTENANCE AND INSPECTION
The safety wire model is 5*20_5A/250VAC,And must meet the explosion-proof
requirements
29
Removal and evacuation
When breaking into the refrigerant circuit to make repairs or for any other purpose
conventional procedures shall be used. However, it is important that best practice is
followed since flammability is a consideration. The following procedure shall be adhered to:
. Remove refrigerant;
. Purge the circuit with inert gas;
. Evacuate;
. Purge again with inert gas;
. Open the circuit by cutting or brazing.
The refrigerant charge shall be recovered into the correct recovery cylinders. The system
shall be "flushed" with OFN to render the unit safe. This process may need to be repeated
several times. Compressed air or oxygen shall not be used for this task.
Flushing shall be achieved by breaking the vacuum in the system with OFN and continuing
to fill until the working pressure is achieved, then venting to atmosphere, and finally pulling
down to a vacuum. This process shall be repeated until no refrigerant is within the system.
When the final OFN charge is used, the system shall be vented down to atmospheric
pressure to enable work to take place. This operation is absolutely vital if brazing
operations on the pipe-work are to take place.
Ensure that the outlet for the vacuum pump is not close to any ignition sources and there is
ventilation available. working on them.
5. MAINTENANCE AND INSPECTION
5. MAINTENANCE AND INSPECTION
Labelling
Equipment shall be labelled stating that it has been de-commissioned and emptied of
refrigerant. The label shall be dated and signed. Ensure that there are labels on the
equipment stating the equipment contains flammable refrigerant.
Recovery
When removing refrigerant from a system, either for servicing or decommissioning, it is
recommended good practice that all refrigerants are removed safely.
When transferring refrigerant into cylinders, ensure that only appropriate refrigerant
recovery cylinders are employed. Ensure that the correct number of cylinders for holding
the total system charge is available. All cylinders to be used are designated for the
recovered refrigerant and labelled for that refrigerant (i.e. special cylinders for the recovery
of refrigerant). Cylinders shall be complete with pressure relief valve and associated shut-
off valves in good working order. Empty recovery cylinders are evacuated and, if possible,
cooled before recovery occurs.
The recovery equipment shall be in good working order with a set of instructions
concerning the equipment that is at hand and shall be suitable for the recovery of
flammable refrigerants. In addition, a set of calibrated weighing scales shall be available
and in good working order. Hoses shall be complete with leak-free disconnect couplings
and in good condition. Before using the recovery machine, check that it is in satisfactory
working order, has been properly maintained and that any associated electrical
components are sealed to prevent ignition in the event of a refrigerant release. Consult
manufacturer if in doubt.
The recovered refrigerant shall be returned to the refrigerant supplier in the correct
recovery cylinder, and the relevant Waste Transfer Note arranged. Do not mix refrigerants
in recovery units and especially not in cylinders.
If compressors or compressor oils are to be removed, ensure that they have been
evacuated to an acceptable level to make certain that flammable refrigerant does not
remain within the lubricant. The evacuation process shall be carried out prior to returning
the compressor to the suppliers. Only electric heating to the compressor body shall be
employed to accelerate this process. When oil is drained from a system, it shall be carried
out safely.
Содержание I19
Страница 1: ...SWIMMING POOL HEAT PUMP UNIT Installation Instruction Manual...
Страница 2: ......
Страница 42: ...Note...
Страница 43: ......
Страница 44: ...Code 20190508 0001...