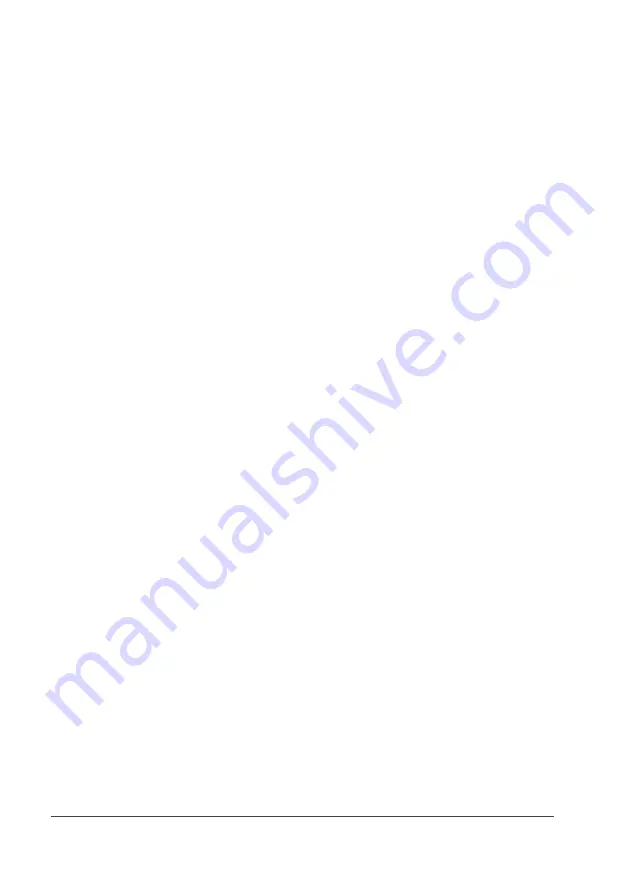
14
SERVICE
PROCEDURE
Commissioning and servicing
procedure
Prior to arriving on site to service or
commission a newly installed System,
check that the electrician has completed
the wiring in accordance with wiring
diagram supplied, and power is
connected to the house.
Confirm with owner that sufficient water
is available in the Tank to allow a proper
setting for aeration and sludge return.
1. Remove all lids to allow access to
all chambers as well as lid to Blower
Housing box.
2. Check that the 3 pin plugs for both
Irrigation pump and diaphragm
blower (air pump) are in and switched
ON.
3. Turn the PVC ball valve supplying air
to the sludge return to OFF, then
slowly adjust the sludge return pipe
to an acceptable flow.
4. Test the high water alarm float by
manually lifting the float, and check
that the audio-visual alarm installed
in the house is working.
5. Test the air alarm by switching the
blower off, or disconnecting the clear
tubing at join, and check the audio-
visual alarm in the house.
6. If insufficient water in the irrigation
chamber, lift pump float to confirm
working.
7. Double check the audio-visual alarm
and make sure the Mute button is in
the ON position.
8. Irrigation field inspection and
dripline line flushing.
Servicing procedure
1. Ensure correct NAME & ADDRESS
is on Service Report.
2. Identify yourself to home owner.
3. Visually inspect the treatment plant
including landscaping lines and
drippers.
4. Remove all Fibreglass/concrete/poly
lids.
5. Turn field isolator to ‘OFF’ position.
6. Remove gauze filter from air pump
and clean. Reposition gauze and
re-attach Blower lid.
7. If any floating contents on top of
clarifier and biomass, skim off surface.
8. Remove and clean filters as necessary
(effluent and irrigation).
9. Collect a sample from inside the
pump well and carry out tests for:
a) Clarity (average 70–100% reading)
b) pH 7.0–7.6 reading
10. Replace all covers accurately
and make sure the field isolator is
switched ON
(IMPORTANT).
11. Fill in Service Report Sheet
accurately.
Leave ONE copy with home owner.
One Copy to be sent to relevant
Council.
One copy to OASIS CLEARWATER
Retain one copy.
If the pH is not stable, ADD acid or
alkaline. If the dissolved oxygen level is
far too HIGH, provide artificial food by
way of ACTIZME or dog biscuits to the
aeration chamber (if D.O. Meter used) and,
if there are major problems contact your
Distributor.