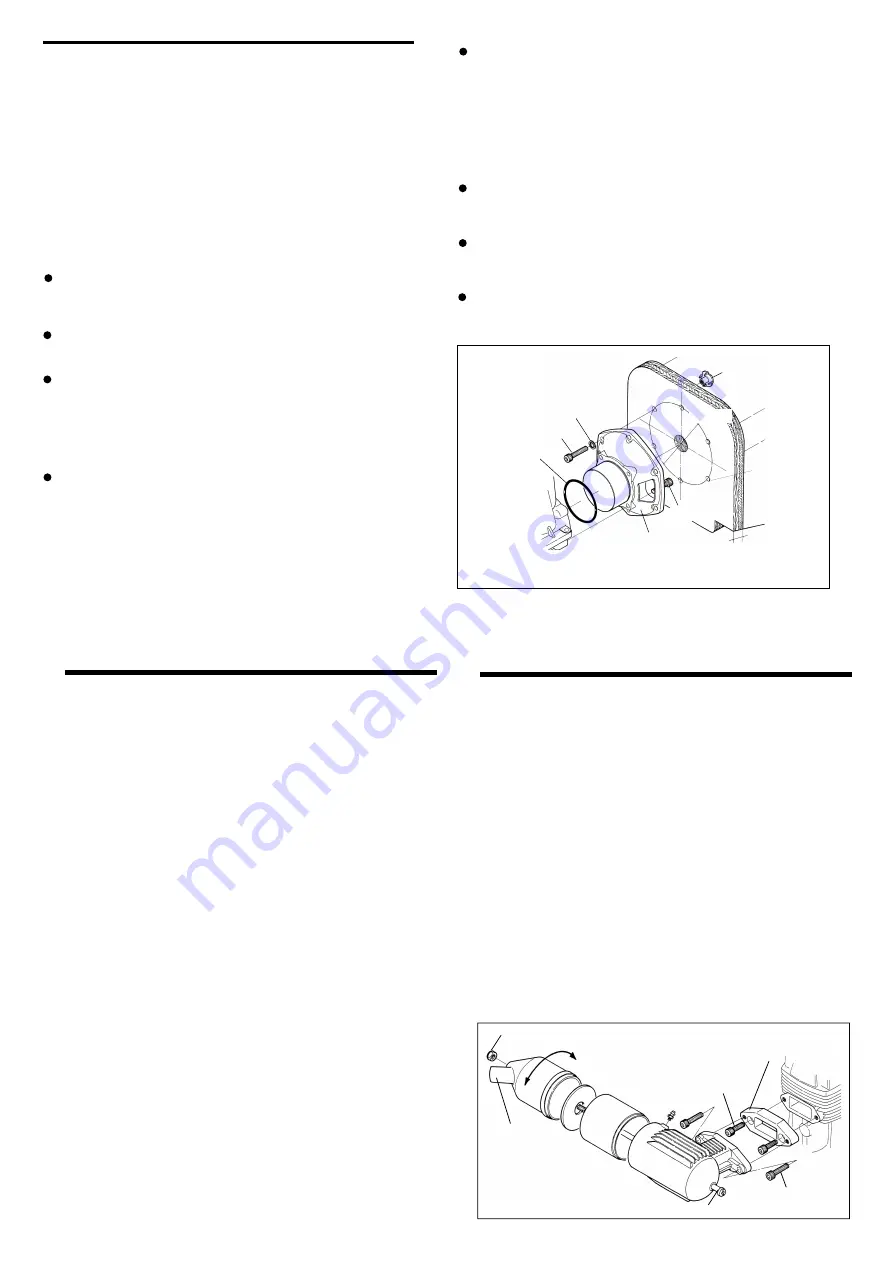
6
There are two methods of installing the engine in the aircraft:
(a) standard beam mounting, using the engine's integral
crankcase mounting lugs, and (b) radial mounting, using the
backplate mount supplied, to bolt the engine to the front
bulkhead or firewall. Whichever method is chosen, make sure
that the structure to which the engine is attached (i.e.
horizontal bearers or vertical bulkhead), is of sturdy
proportions and very firmly integrated with the airframe. This
is necessary both for safety and for the realisation of
maximum performance.
INSTALLATION
Beam mounting
Use heavy, rigid, hardwood bearers or a metal mount and
keep unsupported length as short as possible to reduce
frontal overhang.
Make sure that the bearers are parallel and that their
mounting surfaces are in the same plane.
Use 5mm or 10-24 steel cap-head screws, such as Allen
hexagon socket type, with locknuts, for bolting the engine
to the bearers.
Radial mounting
Draw vertical and horizontal centre lines on the firewall to
correspond with the required thrust-line. Use these to find
the centre of the 100mm (3.93 in.) diameter bolt-circle
required to correctly locate the backplate mount.
Depending on whether the engine is to be installed with
the cylinder upright, inverted, angled or horizontal, position
the backplate mount so that the access hole in the side of
the mount is conveniently located to receive the fuel line
and muffler-pressure line from tank to engine. Place the
mount against the firewall so that its six mounting holes
are accurately aligned on the bolt ciircle. Mark off the bolt-
hole centers and drill six 6.5mm holes through the firewall.
Remove the crankcase cover plate from the engine.
Carefully slide the O-ring seal from the cover plate and fit
it, to the retaining groove on the backplate mount.
Fit the backplate mount to the engine in the required
position and secure it firmly with the four M5x22 Allen
screwa provided.
Bolt the complete engine and backplate mount assembly
to the firewall, using the six M5x25 Allen screws, toothed
lock washers and blind nuts supplied.
Firewall
Toothed lock washer
M5x25
O-ring
Backplate mount
At least 15mm rigid
hard plywood
M5 Blind nut
6.5mm hole
M5x22
100mm
7
Before connecting the throttle-lever / servo linkage, make
sure that no part of the linkage interferes with the internal
structure of the aircraft or wiring, etc., when the throttle is
fully open or fully closed.
Set the throttle lever linkage so that the throttle rotor is (a)
fully open when the transmitter throttle stick is fully
advanced and (b) fully closed when the throttle stick is fully
retarded. Adjustment of the throttle rotor opening at the
idling position can then be made with the throttle trim lever
on the transmitter. (Select throttle-lever and servo-horn
hole positions that will avoid excessive pushrod travel
causing the throttle to bind at either end.)
THROTTLE LINKAGE
When adjusting the throttle lever angle, relative to the
rotor,hold the rotor at about half-way between the open
and closed positions while loosening and tightening the
fixing screw, otherwise the rotor, rotor guide
screw,throttle stop screw or carburetor body may
become burred and damaged.
Note:
•
•
INSTALLATION OF SILENCER(MUFFLER)
To fit the standard silencer
Fix the exhaust adaptor plate to the engine with the two M5
x15 Allen screws supplied.
1.
Now fit the silencer to the exhaust adaptor with M5x20
Allen screws, also provided.
2.
In order to prevent the leakage of exhaust oil from
between the engine and adaptor, and between the
adaptor and silencer, apply a suitable silicone sealant to
the joint faces during assembly.
NOTE:
The angled exhaust outlet is agjustable and can be rotated to
any desired position in the following manner.
Loosen locknut and assembly screw.
Set the exhaust outlet at the required angle by rotating the
rear part of the silencer.
Re-tighten the assembly screw, followed by the locknut.
1.
2.
3.
M5x15
M5x20
Lock nut
Exhaust Outlet
Turn to required position
Exhaust adaptor
Assembly screw