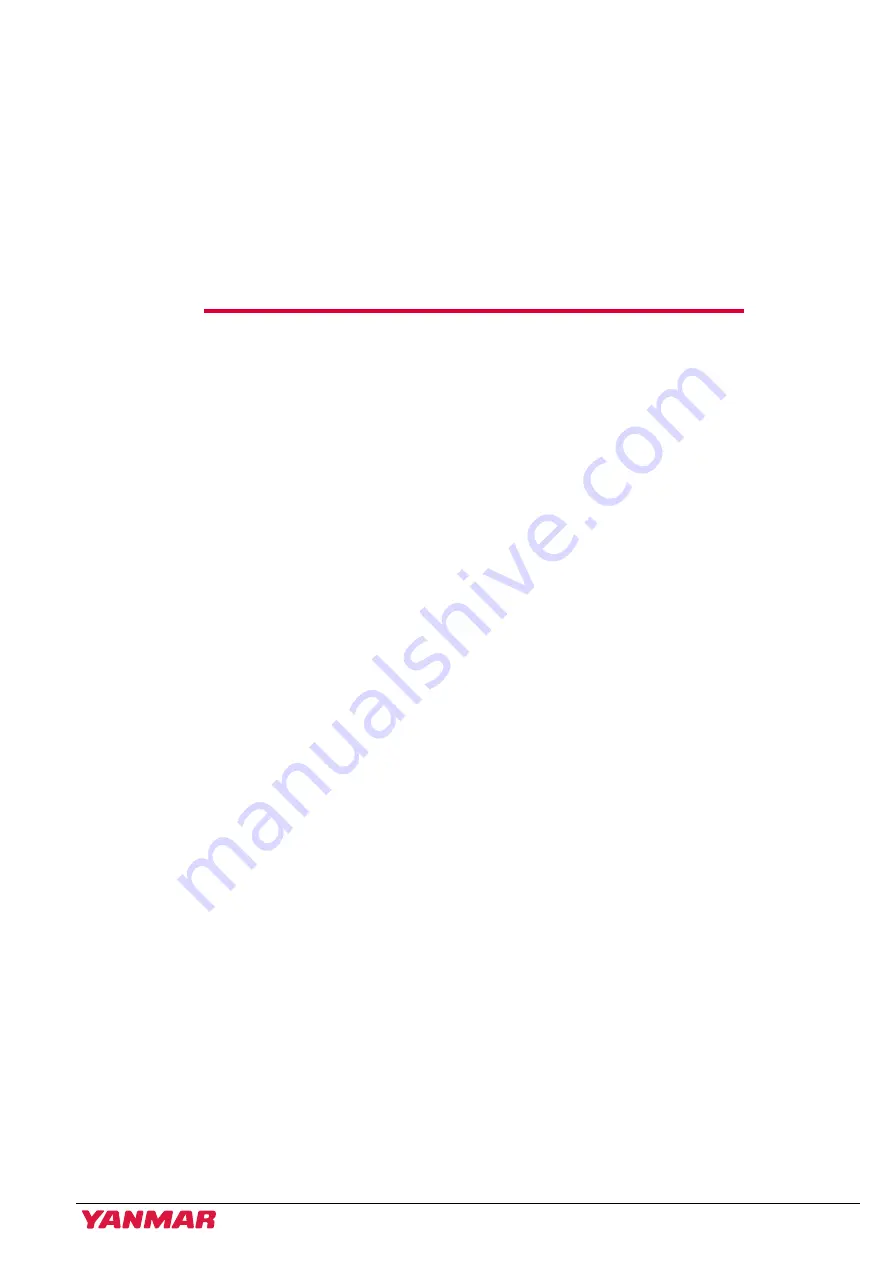
6LT Series Operation Manual
i
TABLE OF
CONTENTS
6LT Series Operation Manual
Page
............................................................................................. 1
Record of Ownership........................................................................... 2
........................................................................................................ 3
Safety Precautions .............................................................................. 4
.................................................................................... 9
Yanmar 6LT Common Rail Series Features and Applications ............ 9
New Engine Break-in........................................................................... 9
Component Identification................................................................... 10
Nameplates ....................................................................................... 14
Vessel Control System (VC20).......................................................... 16
Control the Backup Panel.................................................................. 22
Engine Management from Relay Box................................................ 23
............................................................................... 25
Diesel Fuel Specifications ................................................................. 26
Refilling.............................................................................................. 28
.................................................................................. 29
Summary of Contents for 6LT Series
Page 4: ...TABLE OF CONTENTS iv 6LT Series Operation Manual This Page Intentionally Left Blank ...
Page 12: ...SAFETY 8 6LT Series Operation Manual This Page Intentionally Left Blank ...
Page 42: ...ENGINE OPERATION 38 6LT Series Operation Manual This Page Intentionally Left Blank ...
Page 68: ...ENGINE MALFUNCTIONS 64 6LT Series Operation Manual This Page Intentionally Left Blank ...
Page 70: ...SPECIFICATIONS 66 6LT Series Operation Manual This Page Intentionally Left Blank ...
Page 71: ...6LT Series Operation Manual 67 6LT Series Operation Manual EPA WARRANTY USA ONLY ...
Page 74: ...EU DECLARATION OF CONFORMITY 70 6LT Series Operation Manual EU DECLARATION OF CONFORMITY ...
Page 75: ...EU DECLARATION OF CONFORMITY 6LT Series Operation Manual 71 ...
Page 76: ...EU DECLARATION OF CONFORMITY 72 6LT Series Operation Manual ...