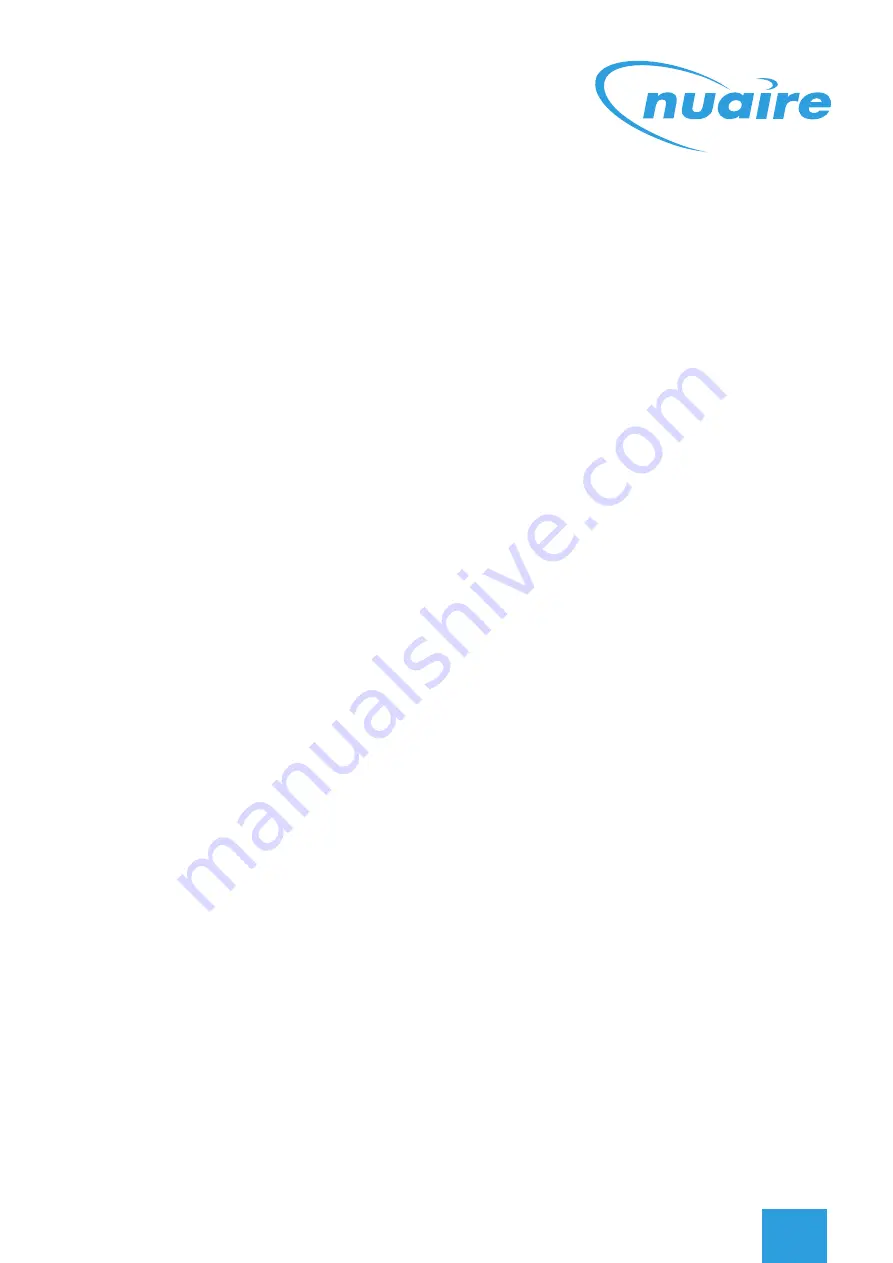
05. 11. 20. Leaflet Number 671829
BOXER BPS
ECOSMART ADAPT (TREND) CONTROL (AT)
15
7.0 DESCRIPTION OF CONTROL - SOFTWARE STRATEGY
The system incorporates a web enabled Trend iQ4E/12/LAN/BAC/230 controller, and is augmented by application
specific unit interface and diagnostic circuits. Controller software is optimised and pre-configured, each unit/
control assembly is fully functionally tested at works (refer to technical documentation for full controller functional
specification).
7.11 CO
2
CONTROL
7.16 PARTIAL RECIRCULATION DAMPER (OPTIONAL)
7.12 SUPPLY TEMPERATURE CONTROL
7.13 FROST PROTECTION
7.15 MITSUBISHI REVERSE CYCLE DX (OPTIONAL)
7.14 NIGHT COOLING / SUMMER FREE COOLING
7.17 ALARMS
7.17.1 CRITICAL ALARM (LATCHING)
7.17.3 THERMAL TRIP
7.17.2 MAINTENANCE ALARMS (NON-LATCHING)
When a CO
2
sensor is selected via UI4 & 5 function knobs, and an enable signal
is received, ventilation will increase to reduce CO
2
concentration the target
CO
2
setpoint. The target CO
2
sensor setpoint can be changed as one of the
commissioning setpoints.
A minimum-on module is connected to the heat/cool relay in order to stop
frequent mode switching.
Although the controller outputs a variable 0-10v heating/cooling voltage, the
Mitsubishi condenser can only run at 7 discrete levels and so cannot supply an
accurate supply air temperature.
The PAC boards are powered from the BPS control so the only connections
required to the Outdoor condenser are S2 & S3. For the same reason, SW8-3
must be set to “ON” on the outdoor unit.
If a partial recirculation module is fitted, the recirculation damper will open/
close via iQ4-8DO Relay 6 according to the following strategy.
If the room temperature is more than 5°C(adjustable) from the setpoint and
free-cooling or free-heating is not available then partially recirculate the air.
This aids heating and cooling elements and also avoids thermal loss from the
room.
While an enable signal is present, this mode modulates heating, cooling &
heat exchanger bypass dampers with the aim of the supply air reaching the
temperature setpoint. Please note that heating and cooling outputs will only
function if the HeatingType or CoolingType setpoints are set to heating or
cooling options.
Should the internal temperature of the unit fall below a value defined in the
commissioning variables, the control will override all heating/cooling logic to
open the LPHW or CW control valves, if fitted. This is to allow any protective
flow through the heating/cooling coils. The supply fan will also stop and the
appropriate frost protection software module will enter an alarm state. This
period will last for a minimum of 5 minutes by default. The fault relay will also
open. Heat and cool demand relays will not operate but digital inputs “Frost
Protecting LPHW” or “Frost protecting CW” will enter an alarm state. Please
note that frost protection will only function if the HeatingType or CoolingType
setpoints are set to LPHW or CW.
For units for use with Mitsubishi reverse cycle condenser units, one or more
PACIF012B-E Interface boards are fitted inside the control panel. The controller
interacts with this board in the following ways:
•
Digital Output Heat/Cool selection from iQ4E relay 8. Another relay is
used to split output over multiple boards.
•
0-10v Heat/Cool demand from iQ4E OUT14.
•
Faults are monitored via iQ4E IN8 (Alarm circuit 2). A relay is fitted to
reverse the fault action.
•
The defrost status relay is connected to the enable input of the controller
to start the fans when the condenser enters defrost mode.
When Mitsubishi Reverse Cycle DX is fitted, this is selected in software by setting
the cooling type “3-Reverse Cycle”. A heating type is not required unless another
heating type is fitted (eg LPHW).
Once this is selected cooling and heating demand will share iQ4E OUT14 and
heat/cool is decided on the state of iQ4E relay 8. (Energised = Cool Demand)
For the cases where Reverse Cycle DX and another heating type are both fitted, a
schedule module is provided in the Trend strategy. When the schedule is on, the
heating output reverts to LPHW/Electric heating.
The enable run-on time must be set to 3 minutes for reverse cycle units. This is
required in order to keep the compressor running for at least 3 minutes for each
period.
Once enabled in software, this routine uses an individual time schedule to cool
the fabric of the building at night using only the external air. This mode only
functions if the daytime temperature is above the setpoint, cooling is possible
and if the cooling air is not too cold.
Once in critical alarm state the unit will drive all heating and cooling outputs
to 0V. Other functions continue as normal. The critical alarm is latched and
required manual reset or power cycle to clear.
In case of software failure, as a final resort, the electric heater is protected by
a fail-safe thermal overload switch. This switch disables the heater controller
via a contactor once the temperature reaches 80°C. When this occurs, the
critical alarm will latch in software and the supply contactor will latch in the off
position.
Once the unit cools, the contactor will remain latched off until power cycle.
Once in maintenance alarm state the only action taken is de-energising of the
fault relay. Once the trigger is removed, the alarm will reset automatically.
Causes of critical alarm:
•
Fan fail via fault circuit 1.
•
Heater overtemp via fault circuit 1.
Causes of maintenance alarm:
•
Condensate pump fault via alarm circuit 2
•
dp Filter fault via alarm circuit 2.
•
IO damper fault via alarm circuit 2.
•
Thermal Wheel fault via alarm circuit 2.
•
Sensor failure
•
Low supply temperature, default 8°C (Can be set to stop fans if required).
•
Frost protection routine active, deafult 4°C (Only runs if water valves are
selected as fitted)
•
Excessively high supply temperature reading (Will stop heating).
If pump fault circuit is broken two additional events occur in order to stop
condensate production.
•
The heat exchanger will enter bypass mode.
•
Alarm 2 circuit will break, stopping cooling functions.
All alarms have a hold off period set by the setpoint “Alarm delay”.
Содержание B815H/ER/AT-L
Страница 25: ...05 11 20 Leaflet Number 671829 BOXER BPS ECOSMART ADAPT TREND CONTROL AT 25 Figure 10...
Страница 27: ...05 11 20 Leaflet Number 671829 BOXER BPS ECOSMART ADAPT TREND CONTROL AT 27 Figure 11...
Страница 29: ...05 11 20 Leaflet Number 671829 BOXER BPS ECOSMART ADAPT TREND CONTROL AT 29 Figure 12...
Страница 31: ...05 11 20 Leaflet Number 671829 BOXER BPS ECOSMART ADAPT TREND CONTROL AT 31 Figure 13...
Страница 33: ...05 11 20 Leaflet Number 671829 BOXER BPS ECOSMART ADAPT TREND CONTROL AT 33 Figure 14...
Страница 35: ...05 11 20 Leaflet Number 671829 BOXER BPS ECOSMART ADAPT TREND CONTROL AT 35 Figure 15...
Страница 37: ...05 11 20 Leaflet Number 671829 BOXER BPS ECOSMART ADAPT TREND CONTROL AT 37 Figure 16...
Страница 39: ...05 11 20 Leaflet Number 671829 BOXER BPS ECOSMART ADAPT TREND CONTROL AT 39 Figure 17...
Страница 41: ...05 11 20 Leaflet Number 671829 BOXER BPS ECOSMART ADAPT TREND CONTROL AT 41 Figure 18...
Страница 43: ...05 11 20 Leaflet Number 671829 BOXER BPS ECOSMART ADAPT TREND CONTROL AT 43 Figure 19...
Страница 45: ...05 11 20 Leaflet Number 671829 BOXER BPS ECOSMART ADAPT TREND CONTROL AT 45 Figure 20...
Страница 47: ...05 11 20 Leaflet Number 671829 BOXER BPS ECOSMART ADAPT TREND CONTROL AT 47 Figure 21...
Страница 49: ...05 11 20 Leaflet Number 671829 BOXER BPS ECOSMART ADAPT TREND CONTROL AT 49 Figure 22...
Страница 51: ...05 11 20 Leaflet Number 671829 BOXER BPS ECOSMART ADAPT TREND CONTROL AT 51 Figure 23...
Страница 53: ...05 11 20 Leaflet Number 671829 BOXER BPS ECOSMART ADAPT TREND CONTROL AT 53 Figure 24...