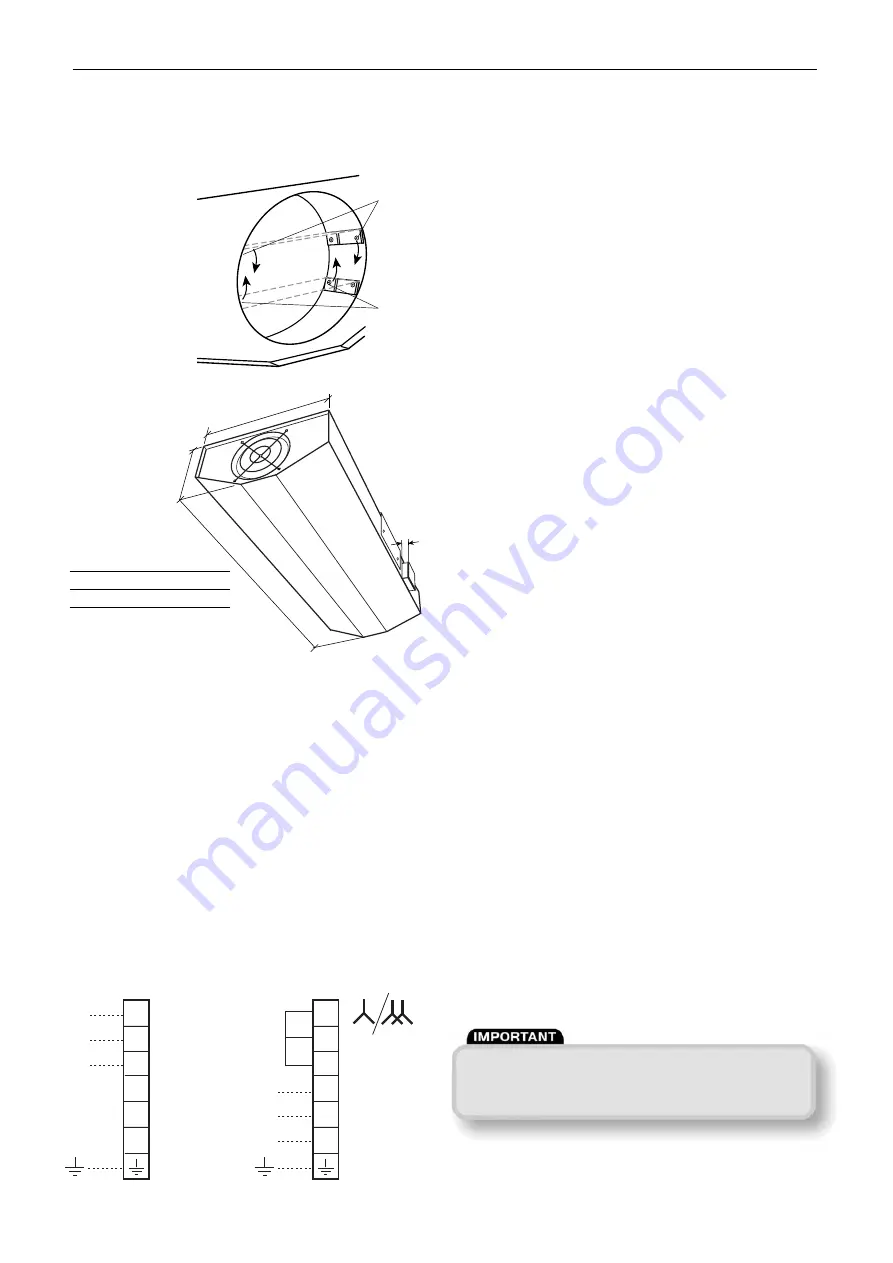
Installation and Maintenance
AXUS SVT2 High Temperature Impulse Axial Fans
2
3) Adjusting the SVT2 Deflector blades
The Deflector blades are factory set for horizontal discharge
(default setting) but can be adjusted for downward deflection
using the following procedure.
1. Adjust top blade (A)
by removing the
2 screws at the front
either side of the blade,
tilt down and replace
the screws.
2. Adjust bottom blade
(B) by removing the
2 screws at the back
either side of the blade,
tilt upwards and replace
the screws.
Dimensions (mm)
Electrical Information
Motors are totally enclosed and protected to IP55 (Dust and
low pressure water jets). Motors comply with BS5000,
EN600034 and IEC34-1. Enclosures are to IP55 with class H
insulation. Motors are tested in accordance with EN12101-3
2002.
N.B. Please note the requirements for maintenance of
the motor. Failure to comply with the recommendations will
invalidate any warranty claim.
Wiring
Electrical supply wiring connection is to an externally mounted
terminal box on the case exterior. The box is pre-wired to the
motor with heat resisting cable.
NOTE: If a two speed starter is used it must have 3 contactors.
Individual wiring diagrams are included with each unit.
A matched Nuaire Inverter Speed Control is available. Please
contact Nuaire.
Two speed 3 phase TAP/PAM wound motors (D.O.L.
starting both speeds)
Leaflet Number 671409 February 2009
Connection details
Check that the voltage full load and starting current on the fan
rating label is suitable for your supply.
Two speed motors
Two speed motors are supplied Tap or Pam single winding.
All two speed types are designed for Direct On Line starting
on both speeds only unless otherwise specified.
Note: Tap wound motors require a three contactor control.
Individual wiring instructions are included with each unit.
Start up procedure
Ensure that the impeller rotation follows the label arrow
indicator on the casing. Should the direction be incorrect on
three phase units, reverse any two of the supply leads. Care
should be taken to set correct rotation as incorrect rotation
may result in damage to the motor. Equipment should be run
for approx. 30 minutes to ensure correct operation. If any fault
occurs, the equipment should be switched off.
Do not re-start
until the fault has been rectified.
Maintenance
General
Nuaire recommends all products maintained in accordance with
the HVCA “Standard Maintenance Specification for Mechanical
Services in Buildings” - Volume II Ventilating and Air
Conditioning. For guidance only due to the different periods
of operation from the time of installation and conditions of
use, no rigid inspection and maintenance periods can be
recommended. We suggest, therefore that the inspection and
if necessary cleaning should be carried out at regular intervals
of 1000 hours of operation or 3 months, whichever is the sooner.
For a routine inspection, check the tightness of all nuts, keys,
grub screws and endbolts etc. Remove any build up of dirt or
dust with a brush.
Motors
On going maintenance - Induction motors, by their very nature
require minimal maintenance. However, a regular regime of
inspection is recommended to ensure minor problems do not
escalate into breakdowns. Typical intervals would be 1000
hours of operation or 3 months, whichever is the sooner.
Checklist
■
No visible damage i.e. impeller cracked, fan cowl bent, foot
cracked etc.
■
No accumulation of dust or fibres on the frame or around
the fan inlet.
■
No significant corrosion of the lifting lugs/eyebolts.
■
No excessive vibration.
■
No loose fasteners.
■
Cables and earths are sound.
■
Sealing of the motor and gland plate in good condition.
■
Insulation resistance adequate, imperative this is checked
after prolonged shutdown.
1U
1V
1W
2U
2V
2W
400V 3 phase
50Hz supply
Link
(if no control
is used)
High speed
Low speed
L1
L2
L3
1U
1V
1W
2U
2V
2W
L1
L2
L3
For good EMC engineering practice, any sensor cables
or switched live cables should not be
placed within 50mm of other cables or on the same
metal cable tray as other cables.
C
B
A
Terminal
Box
55mm
Dimensions A x B x C
SVT2-1
2300 x 320 x 700*
SVT2-2
2300 x 403 x 700*
*Please allow an additional 55mm
for the width of the Terminal Box.
Figure 4.
Figure 5.
To adjust
Deflector
Blade (A)
To adjust
Deflector
Blade (B)