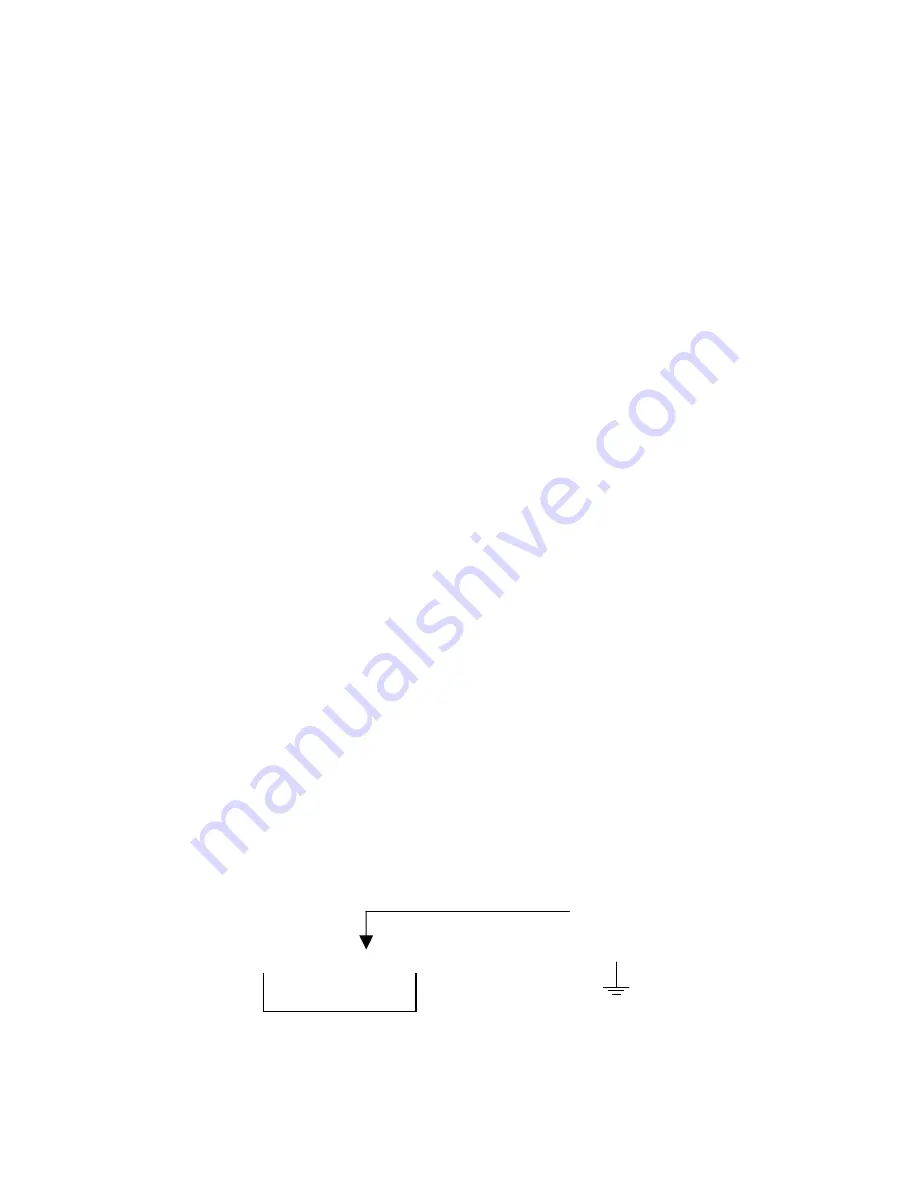
MGN 2800N HP 11
Air/Gas Ratio Controller
The air/gas ratio controller varies the gas pressure in response to changes in combustion air pressure
to ensure that the air/gas ratio remains constant over the operating range of the burner. A separate
gas pressure governor is not necessary. Three impulse pipes (all factory supplied) are connected to
the air/gas ratio controller. The first is connected to the burner body and supplies air pressure to the
ratio controller. Note that in installations with negative air pressure in the combustion chamber, this
pipe must always be under positive pressure. A second pipe connected to the gas line downstream of
the valve set provides gas pressure to the ratio controller whilst the third pipe is vented to
atmosphere.
Valve Proving Systems
A valve proving system, as shown schematically below, is standard on all burners with outputs
greater than 1200 kW (nett) or 1325 kW (gross).
Landis & Staefa LDU11
When the burner operating sequence is initiated, the burner control box energises the proving
system, which then carries out the following checks.
a) Valves V1, V2 and V3 are initially closed. The proving system then opens V3 (in the start gas line)
and then closes it after 2 seconds.
b) V1, V2 and V3 remain closed for 23 seconds while the minimum side of the gas pressure switch
(PS) checks for an increase in pressure. If no increase occurs there is no leakage past V1 and
the sequence continues.
c) V1 is opened for 2 seconds and then closed. V1, V2 and V3 again remain closed for 23 seconds
while the maximum side of the gas pressure switch checks for a decrease in pressure. If no
decrease occurs there is no leakage past V2 or V3 and the burner operating sequence will
continue.
C
ONTROLS
The control package is fitted on the left hand side of the burner viewed from the rear. It includes a
sequence control box of the cyclic type, ignition transformer and all necessary contactors, terminal
strip, motor starter, On/Off switch and two neon lights. The amber light indicates “BURNER ON” and
the red light is illuminated when the burner stops as a result of “EXCESS TEMPERATURE” in the
appliance.
F
LAME
M
ONITOR
An ultraviolet cell is fitted as standard.
BOOSTER WIRING DETAILS
Link terminals 4 to 7
Live wire from burner to terminal 13 on the burner
terminal block
BOOSTER WIRING:
This applies to a Nu-way single booster wired to drawing numbers
WA4-6278 or WA4-6770 only. For further details please refer to Nu-way.
1 2 3 4 5 6 7 8 9 10
Booster terminals
Содержание MGN 2800N
Страница 1: ...MGN 2800N Gas Burner Installation Maintenance Manual...
Страница 5: ...MGN 2800N HP 4 BURNER COMPONENT IDENTIFICATION 1 8 15 4 6 17 13 2 3 16 7...
Страница 31: ......