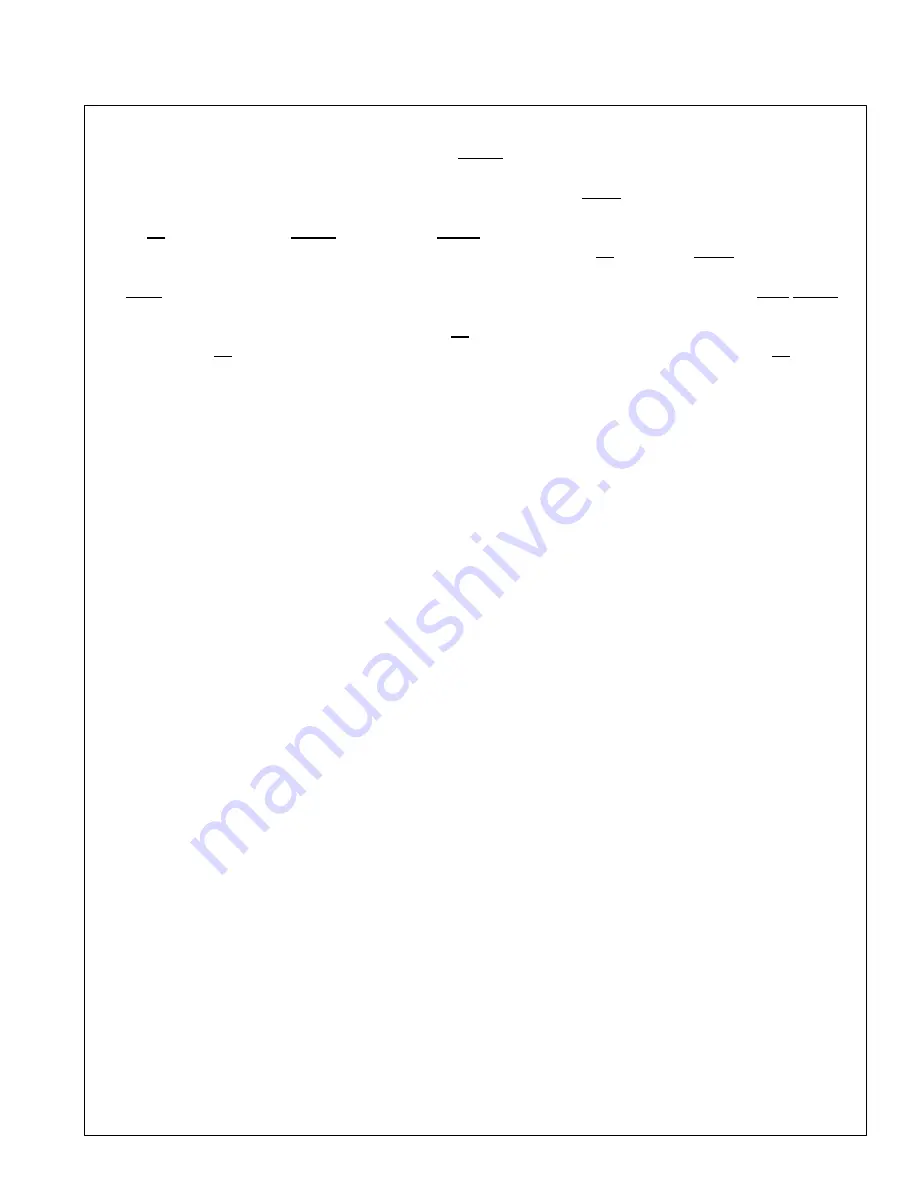
INSTRUCTIONS
Before operating and/or attaching/detaching the pads, you must read these instructions:
*
The machine can be lowered in the back, which raises up the front for ease of transportation and pad
attachment/detachment.
* The machine arrives in Position No. 1 (the operating position). To lower the back of the machine to
Position No. 3 (the pad changing position), hold operator handle with one hand and move the Release
Knob up with other hand. Lower the machine slowly. Let go of Release Knob after machine begins to
lower. The machine will stop in Position No. 2. Move Release Knob up again and lower the machine
slowly to floor (Position No. 3). Pad can now be easily attached/detached.
* To raise machine to Position No. 2 (the transport position), lift up on Operator handle with both hands.
The machine will stop in Position No. 2. The machine can now be transported.
* To raise the machine back to Position No. 1, lift up on Operator handle with one hand and move
Release Knob up with the other hand. Let go of Release Knob after machine starts to raise up. The
machine will stop in Position No. 1.
* After attaching a new pad and placing machine in Operating position, adjust Pad Pressure Knob until
the arrow (Below Left) points to the Release Knob.
* Push machine forward when starting to avoid possible damage to the floor.
* Increase or decrease Pad Pressure as needed, after machine starts.
Pad Installation
Remove the pad that is supplied in the battery compartment of the machine. Remove the center hole of
the pad and step on the center of the pad to compress the edges around the center hole. This will allow
easier installation of the pad holding cup.
With the machine in the pad changing position, #3, carefully center the pad on the driver. Place pad
grabber in the center hole of the pad. Holding the pad grabber, turn the pad driver clockwise until the pad
cup is tight and stops turning.
Caution:
Pads
must
be installed concentric (evenly aligned) with the outside edge of the pad driver.
Failure to follow these precautions will cause excessive machine vibration, a reduction in pad life and
produce unsatisfactory burnishing results.
Failure to install the pad grabber tightly may allow the
pad to be thrown from the driver. Never operate the machine without a Flexiwall Shield in
position over the pad.
Setting Pad Pressure
Pad pressure relates to buffing performance. Too much pad pressure will give uneven results and may
cause circuit breaker to blow. Too light pad pressure will also give poor results and no contact with the
floor. New pads are manufactured in different thicknesses; however, ALL pads will thin down during use
and require periodic adjustment of pad. Therefore, follow procedure below:
ALWAYS start with ALL
pad pressure
OFF
the floor. Increase pad pressure on the floor in
small increments to prevent damage to the floor.
CAUTION:
Too Much pad pressure may permanently damage floor.
The adjustment knob is a simple method of setting the pad pressure based on the thickness of
the pad.
To increase pad pressure, turn the knob counter clockwise.
To decrease pad pressure, turn the knob clockwise.
If the circuit breaker blows on the machine, immediately reduce pad pressure by one full turn or
more on the adjustment knob clockwise. Reset circuit breaker and try machine.
NEW PADS
- Always
decrease
pad pressure three turns after installing a new pad. Move
machine forward while starting machine and fine tune operating amps. Failure to decrease pad
pressure can cause an amp overload, blowing machine circuit breaker.
Содержание 2300BP
Страница 3: ......
Страница 4: ......
Страница 9: ...BASE ASSEMBLY ...
Страница 11: ...SHIELD AND PAD DRIVER ASSEMBLY ...
Страница 13: ...CONTROL FRAME ASSEMBLY ...
Страница 15: ...HOUSING ASSEMBLY ...
Страница 19: ...WIRING DIAGRAM ...